Full-size pickups may seem very American, but the RAM utes being remanufactured in Melbourne can claim plenty of local engineering ingenuity.
The news in February that Holden would shutter the famous lion brand at the end of 2020 reminded many Australians of the way local car making came to a shuddering halt in 2017. At the time it seemed our proud history of automobile manufacturing was all but over.
Yet a few years later, green shoots are springing up in unexpected places, thanks to this country’s extensive network of skilled former auto-industry engineers, designers and executives.
One initiative is the Melbourne-based RAM Trucks Australia (RTA), which specialises in remanufacturing US-built RAM pickups for the Australian and New Zealand markets.
Since its first vehicle rolled off the line in December 2015, RTA has grown to be one of the country’s largest automotive manufacturing operations. The company has a staff of 150 working 24-hour shifts to produce 18 remanufactured trucks per day.
Last year, RTA produced 3300 V8 petrol and V6 diesel RAMs.
This takes place in a sprawling 13,000 m2 factory in south-east Melbourne that’s operated by the Walkinshaw Automotive Group, which also converts Chevrolet Camaros and Silverados. But with three of the four assembly lines dedicated to RAM, it’s clearly the focus of the operation.
Initially a joint venture partner in RTA, Walkinshaw was bought out by American Special Vehicles (ASV) in mid-2018 and is now contracted to handle the remanufacturing only.
That leaves the import and homologation of RAMs to ASV, which is a subsidiary of the Ateco Group, a long-established independent vehicle importer and distributor.
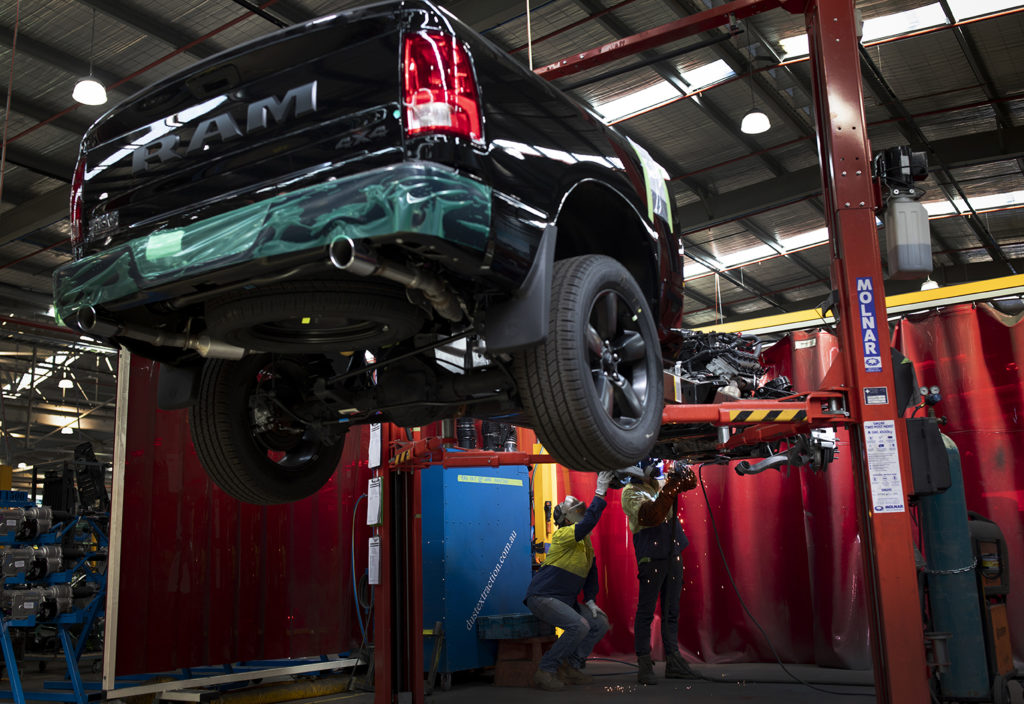
Delivering results
Ateco holds the import rights in New Zealand to Fiat Chrysler Automobiles (FCA) products, which is how RAM came to be part of its portfolio. Having identified the appetite in Australia and New Zealand for utes, Ateco believed the bigger and more heavy-duty RAM could also find a market.
But with the RAM built stateside in left-hand drive only, Ateco needed to find a conversion partner, scoping various specialist operations in Europe, the Philippines, New Zealand and Australia, before settling on the Walkinshaw Group.
RTA’s key point of contact at the plant, and the man who oversees both design and production engineering, is John Di Berardino, a former Holden Special Vehicles engineer with a Bachelor of Engineering in Mechanical and Computing from Monash University, backed up by an MBA from the Chifley Business School.
“Within RAM I currently have the program delivery responsibility, which relies on direction and advice from the engineering department, for the total design package for RAM remanufacture,” Di Berardino told create.
“I’m essentially the point of contact in this group for the customer [ASV]. As an engineer by trade, I help them get the engineering solution for the products that they’re choosing to bring in from FCA.
“The vehicle specification is first sent to the ASV team. Our job then is to receive that spec and design the re-manufacture to suit,” he said.
Doing that requires him to make regular visits to FCA’s vast Warren Truck Assembly Plant in Detroit, Michigan.
Reducing complexity
It was during one such visit that Di Berardino had his eureka moment, realising that despite the plant being highly automated, the process of fitting the RAM’s body to its frame was handled manually and involved just eight bolts.
Di Berardino reasoned that if the body was placed that way, the process could be reversed, obviating the need to get at the firewall from the front of the vehicle. This insight laid the groundwork for a reverse-engineering process that allows the engine and drivetrain to remain fixed to the chassis throughout, reducing complexity.
What this means in practice is installing a new firewall and fitting an RHD-specific steering system, an Australian designed, developed and manufactured dashboard, and an RHD-specific heating and ventilation system — all bookended by separating then re-marrying the body and chassis.
The detail in between these steps is informed by Unigraphics computer-aided design (CAD) programs, which are supplied by FCA for the entire vehicle.
“We’re very, very lucky that we get access to CAD because it’s the IP of FCA. We use it not only for designing parts and integrating them, but also for ADR certification,” Di Berardino said.
While Di Berardino’s role as Program Manager and Operations entails “very little day-to-day engineering design work,” his qualifications and experience are essential to understanding the issues faced by individual engineers along the progression of the design phase.
Spending big on tooling
Di Berardino has no hesitation in pinpointing the supply chain as the trickiest part of the entire RAM remanufacturing project.
“The design is quite straight forward. But how do you get that design into production?” he said.
“The more tooling you spend, the cheaper the piece cost. So, if there’s 400-odd parts for a conversion, that’s 400 times you’re making that decision.
“Then, if you outsource, what technique of tooling do you use? We could do a fibreglass dashboard, which is great for a boat, but it’s not good for 18 vehicles a day. You need injection-moulded plastic that’s OEM grade and accurate for every part, repeating itself 18 times every day.
“So, you tend to follow as much as possible the [original equipment manufacturer] style of manufacturing technique for the part. You make a plastic dashboard, just like the OEM does.”
Among the local suppliers providing components for the RAM 1500 is Melbourne company Lumin, which reworks the instrument panel electrical harnesses to original equipment standard for right-hand drive fitment. Another Melbourne company, Socobell, supplies the all-new dashboard substrate, trimmed to OEM quality.
Saving build time
There is a conspicuous lack of robots in the plant itself, which is set up in stations, each with trolleys and buckets of parts.
The process begins when a left-hand drive RAM is driven in, at which point a team of workers sets upon it. Within minutes the cabin has been neatly separated from the chassis and is wheeled away, while the team removes the dash, seats, seatbelts and other items.
Once the body is off it proceeds to the “cabin weld” station, where the original firewall is removed and a new Australian-designed and sourced firewall panel, complete with appropriate openings to facilitate the conversion, is stitched in by specially certified welders.
The chassis, meanwhile, rolls down a parallel line, allowing it to be worked on simultaneously to the cabin, which saves valuable build time.
One of the more significant modifications here involves plasma-cutting the chassis cross member to accommodate the relocated electric steering rack.
The modification is designed and tested using Finite Element Analysis (FEA) computer testing, said Di Berardino, adding that this, “gave us the ability to predict that we could cut a panel of that size, and carry a safety critical item like a steering rack”.
While there is a keen focus on reusing as many of the original vehicle parts as possible, safety critical items such as brake lines and brake fluid are not reused.
But stripped interior parts are transported to a separate sub-assembly area where plastic parts are removed, trimmed and finished for re-use. This includes reengineering new air conditioning boxes from the original left-hand drive parts.
Back on the production line, the finished cab is placed on a hoist and re-married to the chassis, which has been reassembled with new seat belts; dash; heating, ventilation and air conditioning system; and steering rack.
When the truck nears completion, a WiTech Access Gateway 1000 diagnostic tester connects to each car via a dongle, then with an FCA computer back in Detroit to check for software updates.
The finished trucks are driven out of the factory and over a series of staggered speed humps that settle the suspension, after which the RAM comes back for wheel alignment and a quality audit.
No shortcuts
Asked what differentiates the RTA process from that of other specialist converters, Di Berardino said, “everything you see here”, with a sweeping gesture about the busy factory floor.
“The governance required to do this at this volume is the same as an [original equipment] manufacturer. So, there’s no shortcuts. There can’t be.”
He believes the plant’s volume is greater than anywhere else in Australia, as is the investment in tooling for the 400-plus specific parts RTA required.
“There is probably about $5 million in parts sitting on the shelves. It’s a lot, for a company of our size. We need a three-month window [of parts] to be able to fight off things like coronavirus,” he added presciently.