Researchers and students from Swinburne University of Technology are finding pioneering ways to harness advanced manufacturing, digital and automation technologies to improve outcomes across a raft of industry sectors.
The pace of digitalisation and advances in machine learning are so fast that companies attempting to jump on the automation bandwagon need their own automation, digital and artificial intelligence (AI) algorithms to keep up with the almost daily technological breakthroughs.
But manufacturers tempted to bury their heads in the sand rather than embrace the new opportunities might not be able to remain competitive for much longer.
Their challenge is to explore the possibilities of innovation to find their own bespoke solution.
That’s not an easy task.
“I completely understand that it’s a very difficult situation to be in,” said Professor Suresh Palanisamy, Director of the Manufacturing Futures Research Platform (MFRP) at Swinburne University of Technology. “There are so many technologies available that it’s sometimes impossible to know where to start.
“A business leader might want to find ways to digitalise processes and automate the operation of their factory equipment, but where do they start in the big maze of the digital world?”
The government’s multi-billion-dollar National Reconstruction Fund and the Victorian Government’s Sovereign Manufacturing Fund are set to propel the manufacturing sector, and MFRP is partnering with corporations and research institutes to enable growth in MedTech, aerospace, defence and other priority areas.
World-leading expertise
Palanisamy sympathises with those facing such a dilemma. He and his team of key research leaders have engaged with plenty of industries struggling to figure out the answer.
It’s something for which the MFRP has become adept at finding solutions, acting as a conduit between research and industry to bring world-leading expertise to developing new materials, process and procedures for smart products, focusing on major themes: Industry 4.0, digital design, intelligent robotics, net-zero carbon materials and processes and digital supply chain.
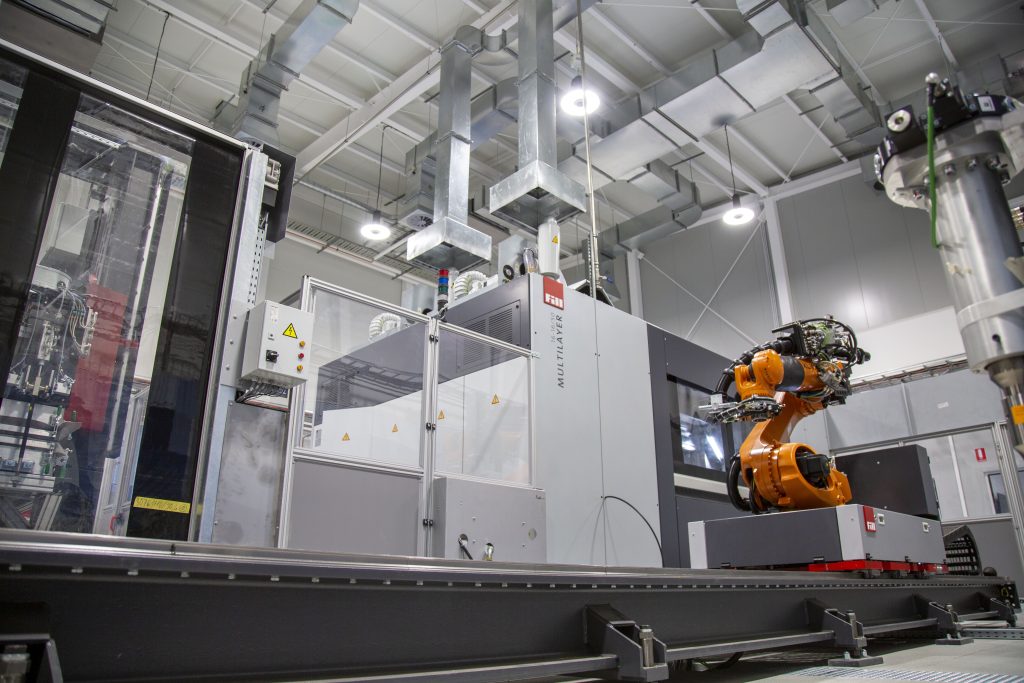
Over the past four years, the team has worked with nearly 100 organisations to help them transition to enhanced digitalisation and then commercialise the opportunities that open up.
“Whatever is being manufactured, we can take a look at what further efficiencies might be achieved through automation and data analytics and AI via the adoption of green and sustainable manufacturing.”
“Once our researchers have mapped the critical processes, we can begin transforming their business processes, enhancing their capability through research and training and developing sovereign capabilities to grow our Australian local supply chain.”
The MFRP has supported major industry players in doing everything from improving food quality, reducing machine breakdowns and advanced robotics to testing defence components and improving the manufacturing efficiencies.
“Our Factory of the Future (FoF) is a digital engineering space — the one of its kind in Australia,” Palanisamy said. “It’s where targeted industry collaborations are nurtured by students and researchers before they bloom into fully realised business models in digital manufacturing.” Similarly, our Industry 4.0 Testlab showcases the ability to transform green fields into manufacturing-ready future factories. Local manufacturing SME consider our TestLab provides a different perspective on their vision for a modern manufacturing factory.
Enhanced manufacturing
The Industry 4.0 Hub at FoF is the first Australian university initiative to educate manufacturing companies on harnessing the power of technologies such as robotics, 3D printing, the Internet of Things, augmented reality and digitisation.
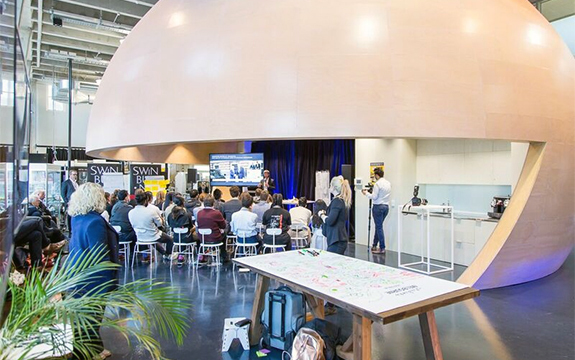
The MFRP has established a joint research centre with Sutton Tools to work on a number of digitisation projects, including automating the selection of cutting tools at each stage of the manufacturing process. Previously, the task involved searching through hard-copy catalogues to track down the right tools, a time-consuming process given the scale of operations.
Swinburne PhD students from MFRP work in the Sutton Tools factory itself and have found ways to digitalise and employ AI algorithms to expedite the process.
“Our students are often embedded into our industry partners’ workplaces so they can gain invaluable industry experience and learn skills that are highly transferable,” Palanisamy said. “Some have ended up joining the companies they’ve worked with on a permanent basis, as they’ve proved themselves to be highly capable and able to fit in with the culture.”
One such example is SPEE3D, a company based in Dandenong that builds 3D printing machines.
Students making a difference
“There’s a tremendous benefit to students as they get unbeatable, hands-on experience and can see how their work is making a tangible difference,” Palanisamy said. “For our partners, they not only get dedicated and passionate students, but the MFRP’s wealth of accumulated knowledge gleaned from all our projects and studies.”
Palanisamy was keen to stress that the concepts of “partnership” and “active collaboration”, both central to MFRP’s mission to deliver advanced manufacturing capabilities to Australian industries that will help them compete in global markets.
“We help our partners solve problems by developing next generation solution using our pioneering technologies,” he said. “But, with every single project completed, we also learn more about what’s possible, and push the technology boundaries a little further.”