Plastic is as essential as its current manufacture is unsustainable. But locals are making big strides towards sustainability.
Ask someone (except perhaps a chemical engineer) what bioplastic is and the common answer will be plastic that is made from plants and is biodegradable. If only it was that simple.
The Australasian Bioplastics Association says that bioplastic comes in many forms, and that it is the chemical structure of the plastic that determines whether it is biodegradable, not the source material. It may not even be made from plants.
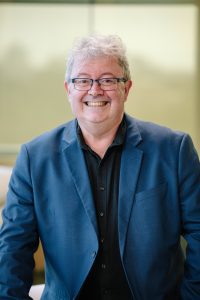
Among the variations are bioplastics made from plant material that are not biodegradable, and plastics created with fossil fuels that are called biodegradable because they include a pro-oxidant, such as manganese, to help speed up the fragmentation process.
The Director of Engagement at the ARC Training Centre for Bioplastics and Biocomposites, Professor Peter Halley, says he prefers the term ‘sustainable plastic’.
“It’s not just about its source or end of life – it should encompass all the processes that went into making it including energy, water consumption, pollution… making sure that you’re doing something better for the environment, and that those costs to the planet can be measured at each stage,” he says.
Building on history
Bioplastic is not a new concept. In the mid 1800s, the first man-made plastic was made from cellulose. In the 1930s, Henry Ford invested heavily in experiments with soybean-based plastics and built a concept car with a bioplastic body and accessories in 1941, but further development was stalled by WWII. Experiments continued during the 20th century, but oil was cheap and plentiful so the fossil fuel became the preferred input for plastic.
More recently, with the realisation that fossil fuels are finite and plastic, whether in landfill or left as litter, is contaminating air, water and soil, the push has been on to develop a material that provides all the benefits of the petroleum-based plastic but is much kinder on the planet.
Plant-based bioplastic is an important step to reducing plastic waste. As it is made from renewable biomass such as corn, sugarcane, or cellulose, it has the capacity to break down into carbon dioxide and water.
However for this to happen, it also needs to be compostable and that requires specific levels of heat and microbes to work. Currently, plant-based bioplastics that end up in landfill will degrade at the same rate as any other organic material: slowly.
BioPak is an Australian company that makes compostable packaging for the food industry, including bioplastic cutlery and bowls. Founder Richard Fine doesn’t believe we should ever be able to say that bioplastic is biodegradable.
“We should be looking at end-of-life options in a separate silo to the materials themselves. There’s so much confusion about bioplastics, compostability and even the term biodegradable – that term is incredibly misleading because ultimately, everything is biodegradable. Unless you specify the conditions and the timeframe, it’s pretty meaningless to say something’s biodegradable,” he says.
“We should really be focusing on where it makes sense to have something that is compostable: where it is contaminated with organic residue and can’t be mechanically or chemically recycled along with the other plastics streams. Then you choose a material, whether it’s bioplastic, or a plastic that is compostable. We should be looking at design cases, rather than just overall biodegradability. That’s a very narrow focus, which gets a lot of people into trouble.”
Some BioPak products are made from polylactic acid or polylactide (PLA), a polyester derived from renewable biomass, typically fermented plant starch, such as corn, cassava, sugarcane or sugar beet pulp. In commercial composting it will break down within 12 weeks. It can also be recycled, but not in traditional recycling streams.
A solution in sight
Mr Fine said a new generation of bioplastics, PHA (polyhydroxyalkanoate) – where bacteria feeding on carbon-based feedstocks creates a polymer within its cell which is then harvested using solvents – is the ‘holy grail’.
“It’s made from bacteria and it is biodegradable in the ambient environment, so even if it ends up in an ocean or river, it will biodegrade very rapidly,” Mr Fine says. This is especially important when such a large percentage of plastic escapes collection for recycling (Australians only recycle about 16% of their recyclable plastic).
Professor Halley agreed, saying his team investigated PHA when they realised the cell cultures used in wastewater treatment plants to break down sewage held PHA.
“So we could have a big local source of PHA and if they can make it in volume, it’s looking like it’s one of the most attractive polymers because of its water insensitivity, and it looks like it matches the properties of polypropylene. [His team members] say that they are aiming for the first products to be like polypropylene packaging for the [packaging and parcels],” he says.
Circular thinking
With the concept of a circular economy gaining momentum, Mr Fine says there were two ways to look at the role of bioplastics.
“We are manufacturing plastics from biobased resources which are renewable, such as sugarcane, and that can be recycled. Hopefully we’ll get to the point where the recycling industry for plastics improves significantly and we can recover a lot more of it.
“But then when we look at potentially, say PLA, for example, I’m producing it from plants, I’m using it for a food-service item, and at the end of its life it can either be incinerated, where it’s producing a net-zero emissions because the plant is absorbing carbon during its growth phase, or it can be turned to compost and returned back to the soil to grow more plants to create more plastic.”
Professor Halley believes there are three actions needed to drive the growth of bioplastics. The first is to improve collection methods of all types of plastics, the second is to educate people about the value of waste, especially that food scraps can be a source of biomass for the plastic, and finally to get plastic producers on board to see that bioplastic can perform just as well as fossil-fuel plastic.
Incentives, such as a sustainability tax on fossil-fuel plastics, would help put bioplastics on an even playing field.
“I encourage people to keep an open mind because now bioplastic means a number of things. It could be good because it’s based on a bioresource, or it could be good that it’s processed at a lower temperature compared to synthetic plastics, or it could be the end of life where it is composted or recycled.
“I would ask people just to wait – we’re catching up to matching the properties [of synthetic plastic]. And we’re looking at it holistically, from the source to end of life, so stay with us.”