Australia is lagging some distance behind Europe when it comes to the adoption of digital twins in manufacturing, and risks being excluded from global markets if more engineers aren’t upskilled to take advantage of the technique.
That’s the warning from Professor Boris Eisenbart, Research Director of Swinburne University of Technology’s National Industry 4.0 Testlab, who is developing new ways to test and perfect components before they are even produced.
Digital twinning involves designing products using virtual models that exactly replicate real world conditions. The entire life cycle of each one can be simulated in a number of different test conditions, allowing technicians to optimise the design.
“It’s becoming an essential process for getting it right first time without the need for a lengthy period of trial and error,” Eisenbart said.
“It’s widespread in many other parts of the world, but it’s only really just getting started over here, as not enough engineers have had the training necessary to harness it. And that’s a cause for concern in terms of our industries remaining competitive internationally.”
Eisenbart fears the slow adoption rate will become a serious issue as regulators such as the European Union tighten requirements for carbon footprint reporting and demand that details of supply chains and design process be included.
“When you’re using a digital twin, you have a complete record of how the design evolved from start to finish, so it’s much easier to assess the volume of emissions that were involved and present the evidence,” he said.
“Doing the calculations manually is a laborious undertaking. If Australian industries are perceived as lacking traceability, major manufacturers may look elsewhere.”
Showcasing benefits
Eisenbart and his team at the Swinburne-CSIRO National Industry 4.0 Testlab for Composite Additive Manufacturing have developed revolutionary new ways to devise and test carbon fibre and glass fibre composites, and their production using digital twins, which he hopes will showcase the many advantages of the process to manufacturers.
“We see it as part of our role to expose the industry to the potential so they can imagine how it would help them,” he said. “Basically, if you’re making a bespoke component at high volume, you’ll benefit from the digital twin, getting it right much faster than is the current standard.
“Over the next few years, rapid digitalisation and advances in artificial intelligence will mean anyone who hasn’t embraced digital twins is going to be left behind, especially if their rivals are already using them to achieve better results.”
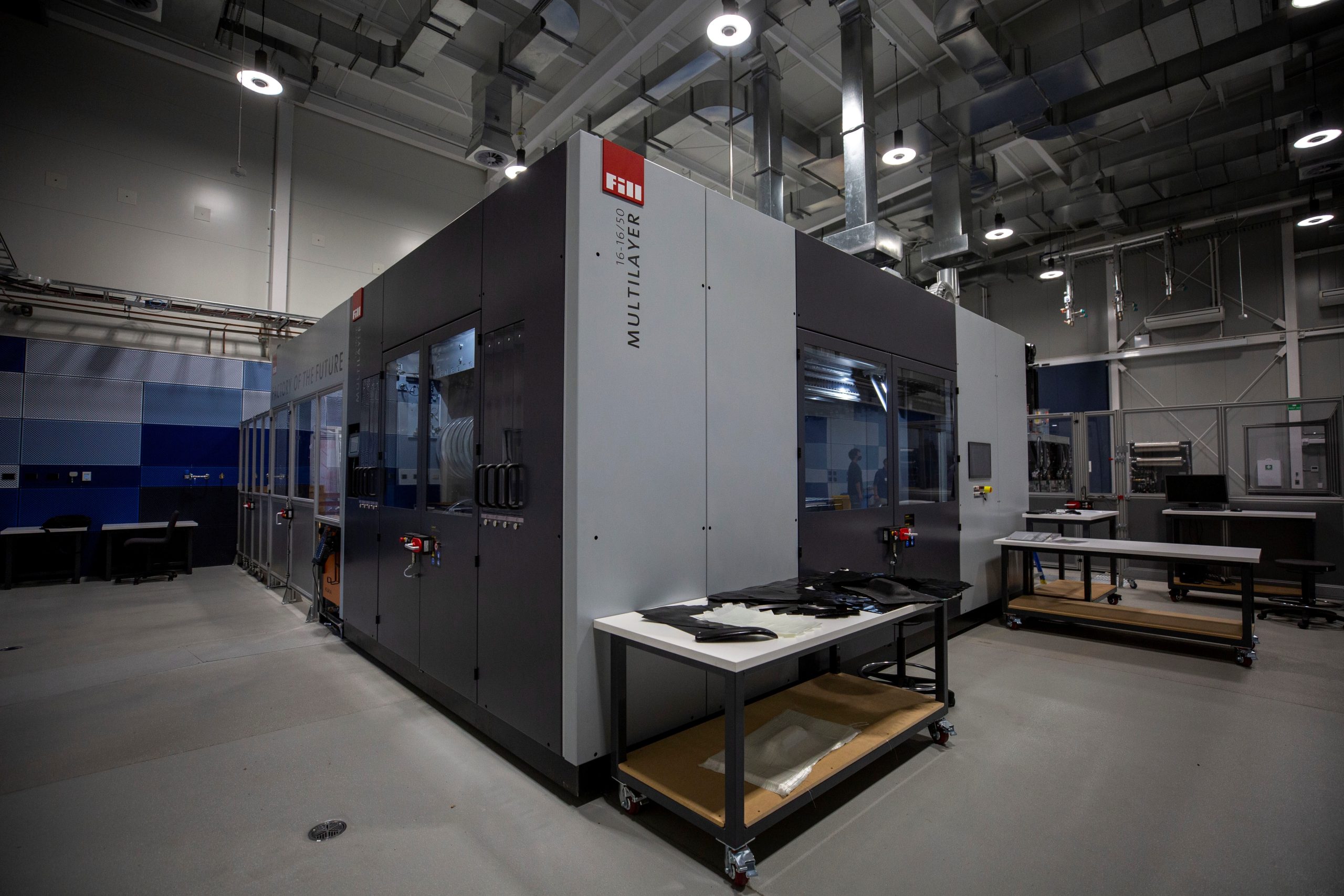
Eisenbart’s teams have been working with CSIRO on the design and manufacture of the fold-out petals for an orbiting satellite dish.
“In our lab, we’ve found ways to virtually replicate the laying process of the carbon fibre tapes, building those petals in a way that achieves accuracies of less than a millimetre,” he said. “Once such a dish has been shot up into space, the individual petals slowly open out on their hinges. Precision is absolutely vital as deviation would critically impact functionality.”
The same model could equally be used to design parts for drones, bicycles, cars or anything else that uses carbon fibre composite material. Recently, Swinburne researchers have been liaising with Boeing and Quickstep on ways in which digital twins might enhance production of aircraft and drone parts.
Performance criteria

But a digital twin doesn’t just identify the most efficient process; it can also weigh up a set of weighted criteria.
“A good example is aerospace, where high performance is critical,” Eisenbart said. “Whereas in automotive fields, a manufacturer may be prepared to accept slightly lower performance level if this comes with a much more manageable price tag.
“The digital twin can be programmed to consider factors such as production time, sustainability and how long a product is expected to last, then come up with a solution before any machines in the factory have even been turned on. What would normally take two or three days of manual work, we can do in an hour. There’s much less trial and error or wasted materials.
“What’s unique about the digital twins we’ve created at Swinburne is the extraordinary number of parameters that go into the calculations. They’re advanced and specialised to our needs and can make more reliable predictions of energy consumption, quality and production time.
“Our vision is to contribute to the decarbonisation of the manufacturing industry by identifying cost-effective, data-driven solutions that produce the fewest emissions. The progress we’ve made so far has been very encouraging and we hope more manufacturers will contact us to discuss how we can help them jump aboard the digital twin bandwagon.”