The picturesque coastal city of Bunbury, about two hours’ drive south of Perth in Western Australia, is about to get a long-awaited bypass that will transform its congested main road network and reduce commuting times by up to 18 minutes.
The four lanes of the $1.25 billion Bunbury Outer Ring Road are due to open in late 2024 and will stretch 27 km between Forrest Highway in the north and Bussell Highway to the south of the city. Fifteen new bridges and nine junctions will connect them to local roads.
One notable aspect of the scheme is that its architects and planners opted to use customer-engineered new generation, high-performance pot bearings, 100 per cent fatigue-proof steel finger joints and steel strip seal joints and other pieces of construction hardware, rather than relying on off-the-shelf low technology alternatives.
The decision is unusual in Australian infrastructure, as precision-engineered components that are made to measure add to the short-term costs, a fact that often puts off contractors working to strict budgets.
But focusing on upfront expenditure can be a false economy.
“It’s very common to see items like pot bearings wearing out quickly and having to be replaced every five or 10 years,” said Virendra Ghodke, General Manager at mageba Australia.
“Design engineers should specify better quality ones that would last for 50 or more years, even though they are more expensive.”
“Just imagine the cost and inconvenience of employing construction crews to replace malfunctioning bearings over and over again during the lifespan of a bridge. Each time, you would need to purchase brand new bearings, close the surrounding roads, and divert traffic, causing significant disruption.”
High-quality, lower costs
Even if a custom-made product costs more, there would still be considerable savings over the long term.
The stakeholders behind the Bunbury project saw the sense in involving mageba, one of the world’s leading engineering organisations, from the design stage all the way through to completion and incorporating a range of its high-quality products into the project. mageba’s Head of Sales and Project Management, Sabia Kazi and project manager Utkarsh Sharma have jointly and closely managed the entire process.
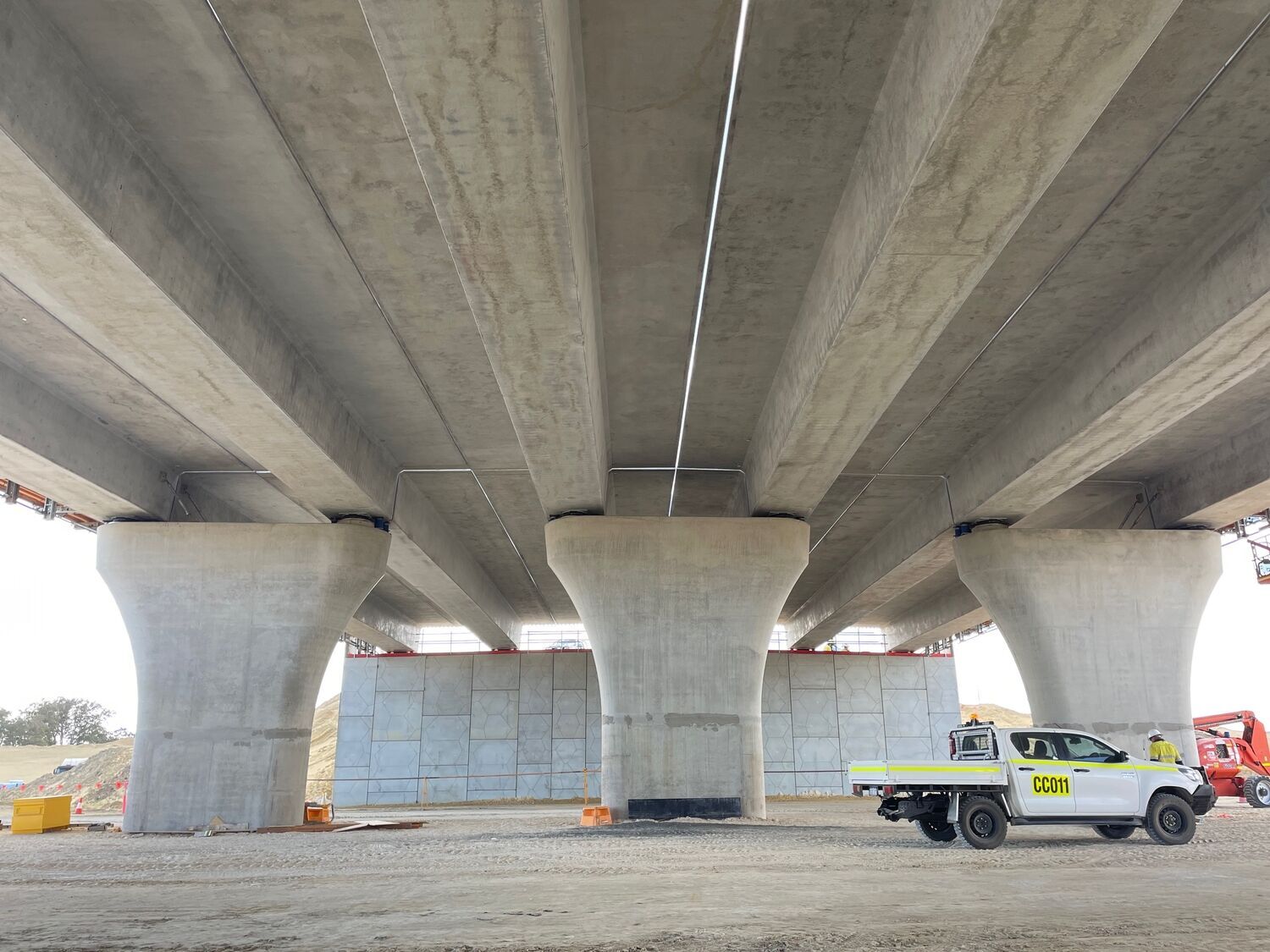
“We design everything to have the lowest possible life cycle costs,” Sharma said. “That means maintenance is minimised, so engineers can set and forget, rather than worrying, about how quickly they’ll have to replace a particular part.
“For example, many firms use aluminium for the expansion joints bolted into concrete. But they aren’t as robust as those fabricated from steel that we manufacture.”
As the concrete ages, the bolt loses its pre-stress and could work its way loose, which could be a big problem if it falls onto the road and causing a serious hazard.
“mageba’s unique TENSA-GRIP expansion joints have been successfully tested for over 10 million load cycles, many more than any competitors can achieve,” said Kazi. “So they are robust enough for heavy traffic flow and are galvanised to protect them from corrosion”, added Sabia Kazi.
Long-lasting bearings and joints are also a more sustainable option, a critical factor in every aspect of construction.
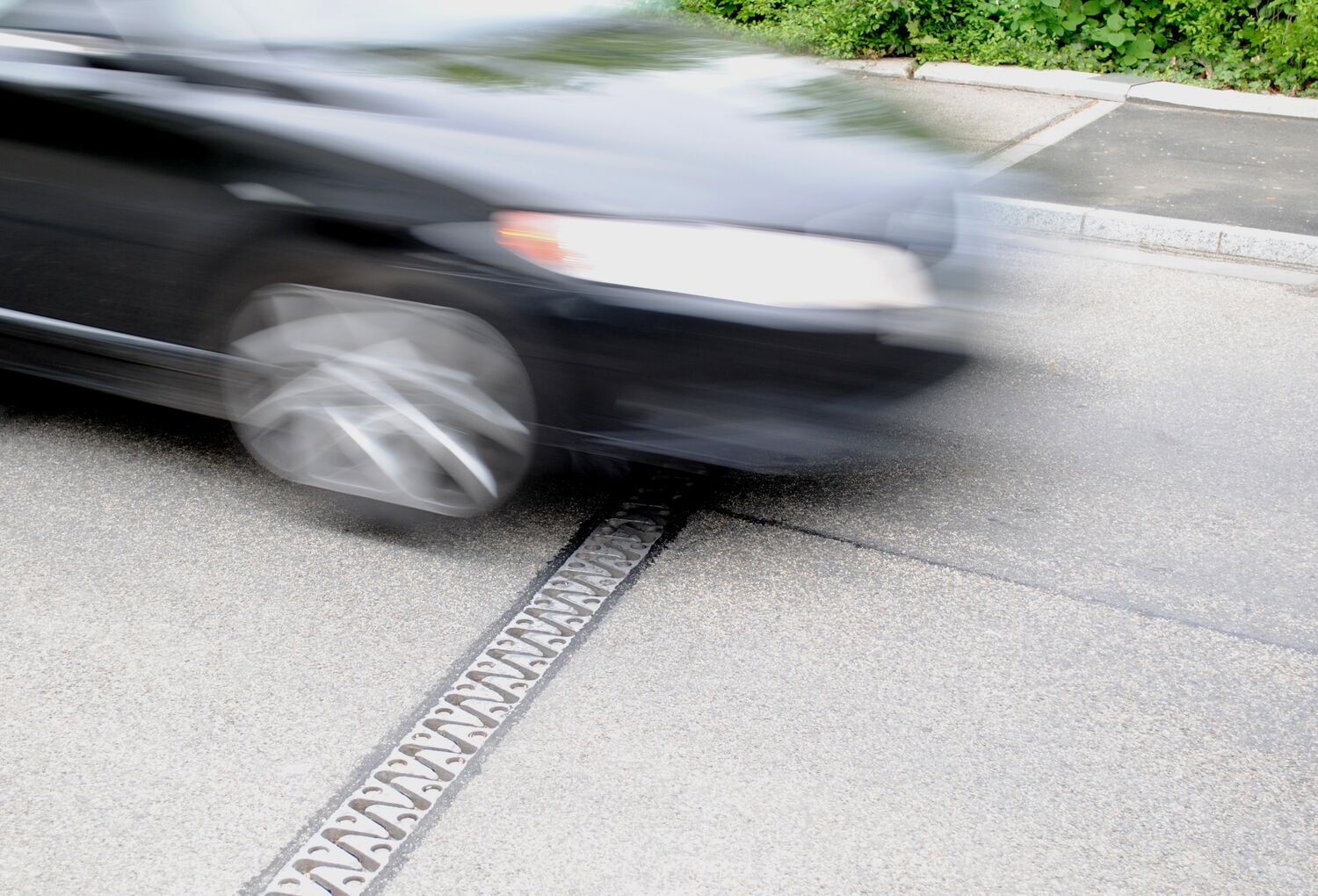
Made to measure
The company’s approach to manufacturing has become popular with engineers and developers.
“All our competitors have catalogues containing lists of their products. So whatever piece of infrastructure is being planned has to accommodate those dimensions,” Kazi said. “But often, that’s simply not possible, or it’d mean that something doesn’t fit properly. When that happens, it can cause delays and disputes with contractors.”
“All of our solutions are custom-made for each project so they comply with specific requirements, and contain significantly more versatility of design. For Bunbury, our design team in Sydney was responsible for every solution we delivered, and over a quarter of them were manufactured in Australia.”
Another groundbreaking product that mageba will apply to an upcoming highway upgrade project is the high-performance sliding material ROBO-SLIDE 75, which has been tested for 75,000 m accumulated sliding path.
This is several times the life expectancy of a standard sliding material such as PTFE. PTFE, being a PFAS material, is set to be prohibited for any use by the Australian Government as early as 1 July 2025, citing environmental concerns around the product. mageba has moved away from using the material well ahead of time as part of its drive towards more sustainable engineering.
Compromising quality
For Kazi, the widespread use of lower quality products in bridges and highways results from insufficient design policies and specifications.
“The lists of approved products often leave the maintenance and construction teams frustrated, because low-quality products are still being used to save money,” he said.
“They’re the ones actually out in the field who can see what needs to be done but can’t do anything about it. That’s why we’re seeing bearings and expansion joints failing way earlier than expected.”
Ghodke has twice successfully convinced the Australian Bridge Design Code committee to improve its standards and raise the bar for the entire industry, but argues that more needs to be done to raise awareness of the benefits of high-quality products.
“There are other standards that also need to be updated to make our infrastructure safer, more reliable and long-lasting,” he said.
The estimated 18,000 drivers a day who will get to their destination sooner thanks to the Bunbury Outer Ring Road won’t know or care what type of structural bearings or expansion joints are installed in the bridges they’ll pass through. But they will be thankful that the new road won’t have to be closed every few years because some need replacing.
Click here, email info.au@mageba-group.com, or call 8158 5850 or 1300 62432 to find out more about mageba’s industry-leading range of infrastructure solutions.
Congratulations for your untiring efforts and achievements over the years with regards to customized bridge bearings and expansion joints for various projects in Australia. Keep up the good work.