Australia would approach the task of building The Ghan, an almost 3000 km rail line stretching through the nation’s centre, very differently if construction began today.
Few engineers argue that the Ghan was a case of perfect project management.
After all, in the first 12 months of actual construction, less than two kilometres of track was laid.
But in its defence, the massive undertaking was actually a combination of a number of smaller projects, the first of which began in the mid-1880s.
The Ghan as we know it today — a 2979 km freight and passenger line stretching from Darwin to Adelaide — was not completed until 2004, almost 120 years after it began.
It’s a far cry from the rampant pace of today’s rail industry — in China, around 19,000 km of high-speed line have been laid in just nine years — and the processes and technologies were worlds away from those that would be applied today.
For a form of transport that is often considered to be traditional, rail has come a very long way.
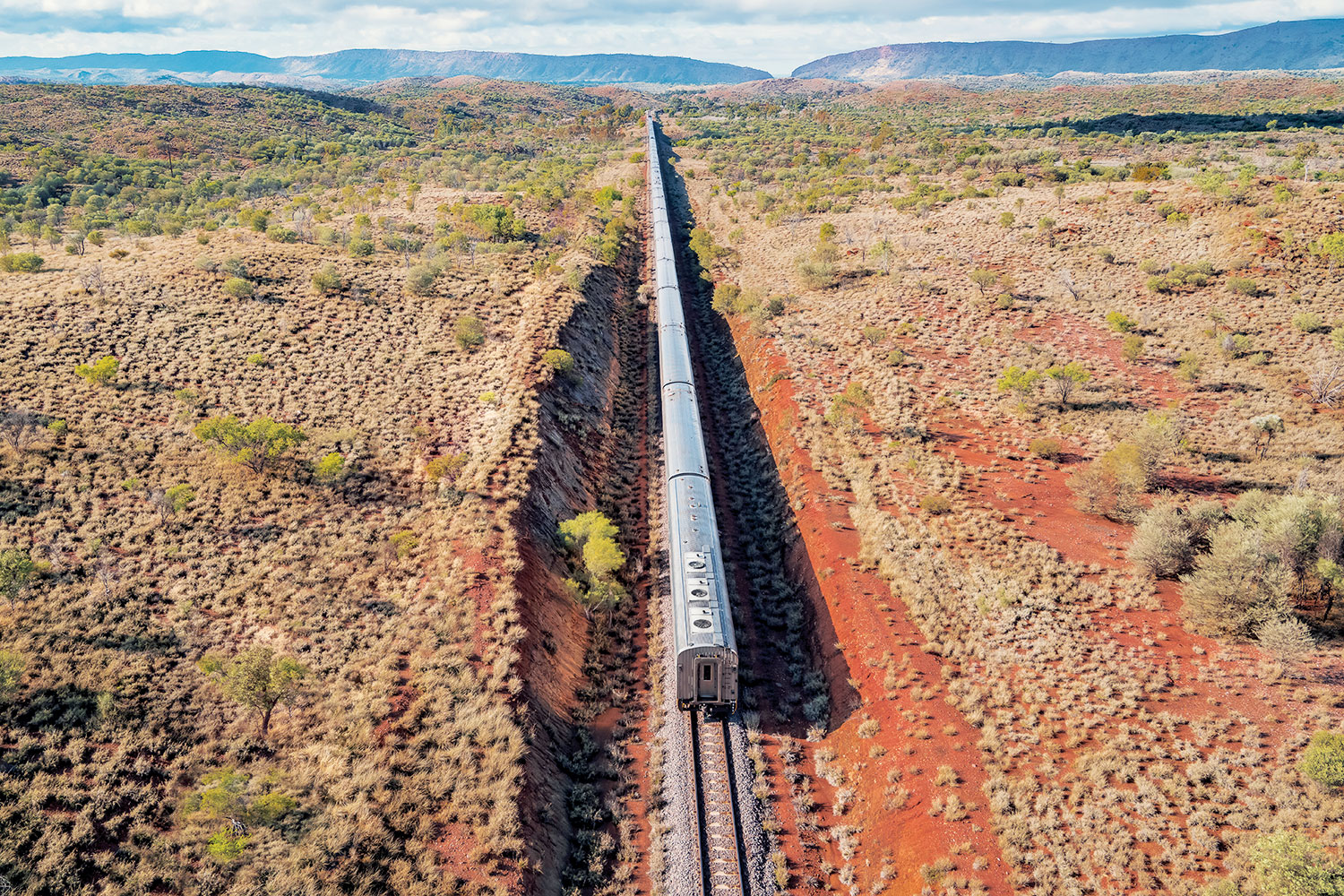
The most surprising Ghan fact for rail engineers in today’s environment is that very little was done in the way of surveying and gathering geological and hydrological data prior to tracks being put down.
“There are a few essential steps that we’d take prior to a rail project,” said Nicole Waterman, Design and Engineering Manager at Laing O’Rourke.
“We’d begin with an aerial LIDAR survey using a rotary drone. That would enable us to choose the alignment, and then we would do a feasibility study on the alignment. After that, the geotechnical investigation begins.”
The geotechnical survey, Waterman said, would likely begin with boreholes at 50 m intervals.
“If we were designing a road or even rail through a metropolitan area, we would bring the boreholes much closer together,” she said.
“Because Australian geology is now much better known and that stretch between Adelaide and Darwin is quite inert, the centres of those boreholes could move a little further apart as you begin to get predictability. But you would certainly start with a steady rhythm of borehole logging.”
Riding the rails
The lack of survey data was acceptable at the time for another important reason, said Buddhima Indraratna, Distinguished Professor of Civil Engineering at the University of Wollongong.
The trains were much smaller, lighter and slower — as are the trains that still use the Ghan line.
That means they had a reduced impact on the rails, the ballast — the track-bed upon which rail ties are laid — and the ground below, known in rail-speak as the ‘subgrade’.
“The average length of Ghan trains is probably 750 to 800 m,” said Indraratna, who is also the Founding Director of the Centre for Geomechanics and Railway Engineering.
“But modern trains are up to two-and-a-half times heavier and the length of some trains, particularly coal trains, can be up to 4 km. They might be carrying 70,000 t of weight and moving at an average speed exceeding 60 to 70 km per hour on some resilient routes. Some rail authorities in New South Wales, Queensland and Western Australia have been talking about elevated speeds up to 80 to 100 km/h.”
This length, weight and speed differential introduces a number of new challenges for the rail engineer. Instead of 40 light carriages moving at a gentle pace, there may be 350 extremely heavy carriages moving fast.
Instead of an axle load of 15 t, modern heavy haul trains can have axle loads bearing 35 to 40 t. As a result, everything below the train itself is put through far greater stress.
Not too hard, not too soft
Consider, Indraratna said, that a 4 km train might have its engine in one town, its rear carriage in another town and its middle on a bridge as the train moves at 100 km per hour.
Along the entire length of the train, enormous forces are being concentrated on the ballast and the subgrade.
If the subgrade is not of a high quality — that is, if it is soft, wet and weak — this dynamic load can cause a phenomenon known as ‘mud pumping’.
This means a hydraulic gradient is created within the soft soil, forcing the soil to flow or slurry, and then pump upwards into the ballast and to the top of track.
The track will be unusable until the polluted ballast is completely replaced and the mud holes are removed.
“This didn’t happen in the past because the trains were not heavy and fast enough,” Indraratna said.
“Now it’s a problem. Some train drivers may practically refuse to drive over certain types of boggy soils because, they say, it feels as if the train is travelling over a wet sponge. The driver can actually feel as if the wheels are losing proper contact.”
In any areas of poor-quality soft subgrade, the ballast layer has to be built much higher than usual — sometimes up to 2 to 3 m high as embankments — to prevent load transferring to the soft soil, thus reducing the risk of this phenomenon.
And the problem of laying rail over a surface of hard rock is just as challenging for these very heavy and long trains, but for a different reason.
“If you are laying railway on rock, your ballast will break very quickly,” Indraratna said.
“Because rock is a very hard subgrade, the reaction to the axle load is very high, so the rock particles or ballast can be destroyed, at times pulverised.”
Indraratna and his team at the Centre for Geotechnical and Railway Engineering have developed a solution for this, which also happens to help solve an environmental problem.
A modern approach
If the Ghan were being commenced today, Waterman said, once the aerial and ground surveys were complete, 3D models would be developed to assist the design and construction process. Then time would be added in, to create 4D sequences.
Virtual time in 4D modelling allows project managers to test the sequencing of the construction, which would be particularly important on a railway project that is not only evolving over a period of time, but which also covers a large area geographically.
“The complexity is managed by breaking up the build into packages, and how you supply and contract out each of those packages,” Waterman said.
“You might separate such a project into 100 km sections and manage logistics by strategically placing your camp between two sections, then leapfrog as each is completed.”
Finally, Waterman said, the other major difference in modern construction is the likely inclusion of technology for driverless trains.
Unlike autonomous cars, which are still a largely futuristic idea, driverless trains are a reality around the globe.
Rio Tinto runs an autonomous train to haul iron ore, remotely controlled from 1500 km away. And trams and metro trains have been running driverless for many years in China, Singapore, Hong Kong, the US, the UK and Europe.
Sydney commuters got to ride the city’s first driverless train when the Northwest Metro line opened to the public on 26 May this year.
Construction additions to allow for driverless technology would include screens on platforms to ensure passengers cannot fall on to the tracks, an energy system that involves power to drive the train being delivered through the rails, and various other safety and security measures, including the ability to monitor and control the entire system remotely.
“There is some fantastic technology involved in rail today,” Waterman said.
“It’s what continues to bring young engineers into this field. For a traditional mode of transport, it’s a very fast-paced and high-tech arena.”
Tyre tracks
According to Waste Management Review, more than 50 million used tyres are generated in Australia every year, of which fewer than five per cent are recycled locally.
Around 32 per cent are shipped to Asia for recycling, using more fuel and producing more carbon. The rest, the magazine said, are “either landfilled, stockpiled, illegally dumped or ‘lost’”.
Distinguished Professor Buddhima Indraratna and his team of researchers at the Centre for Geomechanics and Railway Engineering at the University of Wollongong have found a railway solution that may just kill two birds with one stone.
They have developed a way to recycle tyres into rubber mats that can be laid, like carpet, between hard surfaces such as rock and railway ballast.
“Some companies make these brand new and they are very expensive, but we can make them from discarded rubber tyres,” Indraratna explains.
“We call it 2-REAL, which stands for Recycled Rubber Energy Absorbing Layer.
“The problem of instability for long, heavy trains is a serious one, particularly when various parts of the train are experiencing different ground conditions. Using materials made from recycled rubber, we can create an energy-absorbing reservoir to create consistent track conditions and also to prevent track damage.”
Indraratna, with EcoFlex International, also has a pending patent for a method of laying whole tyres down, beneath the ballast, in a honeycomb pattern.
“So, you have several rings of old rubber tyres placed together, like a beehive when you look from the top,” he said.
“Then you fill the cavities with recycled rubber crumbs and other waste materials like discarded ballast and coal wash. The tyres are heavy and highly frictional, so they don’t move. Then you run the normal ballast and track over this tyre assembly, and it absorbs the energy from the fast-moving, heavy trains.”
These new methods, which solve problems in railway engineering as well as recycling, are already finding their way into modern railway construction.
This article originally appeared as “Going the distance” in the September 2019 issue of create magazine.