The team behind RASTRUM, a bright pink bioprinter that is revolutionising cancer research, took home the 2021 ANSTO Eureka Prize for Innovative Use of Technology last week.
RASTRUM is the combined effort of teams from the University of New South Wales (UNSW) School of Chemistry, the Australian Centre for NanoMedicine, the Children’s Cancer Institute and Inventia Life Science.
The small but powerful machine enables scientists to create 3D cell cultures for biology research and drug discovery. In particular, it has been used to print models of tumours for cancer research.
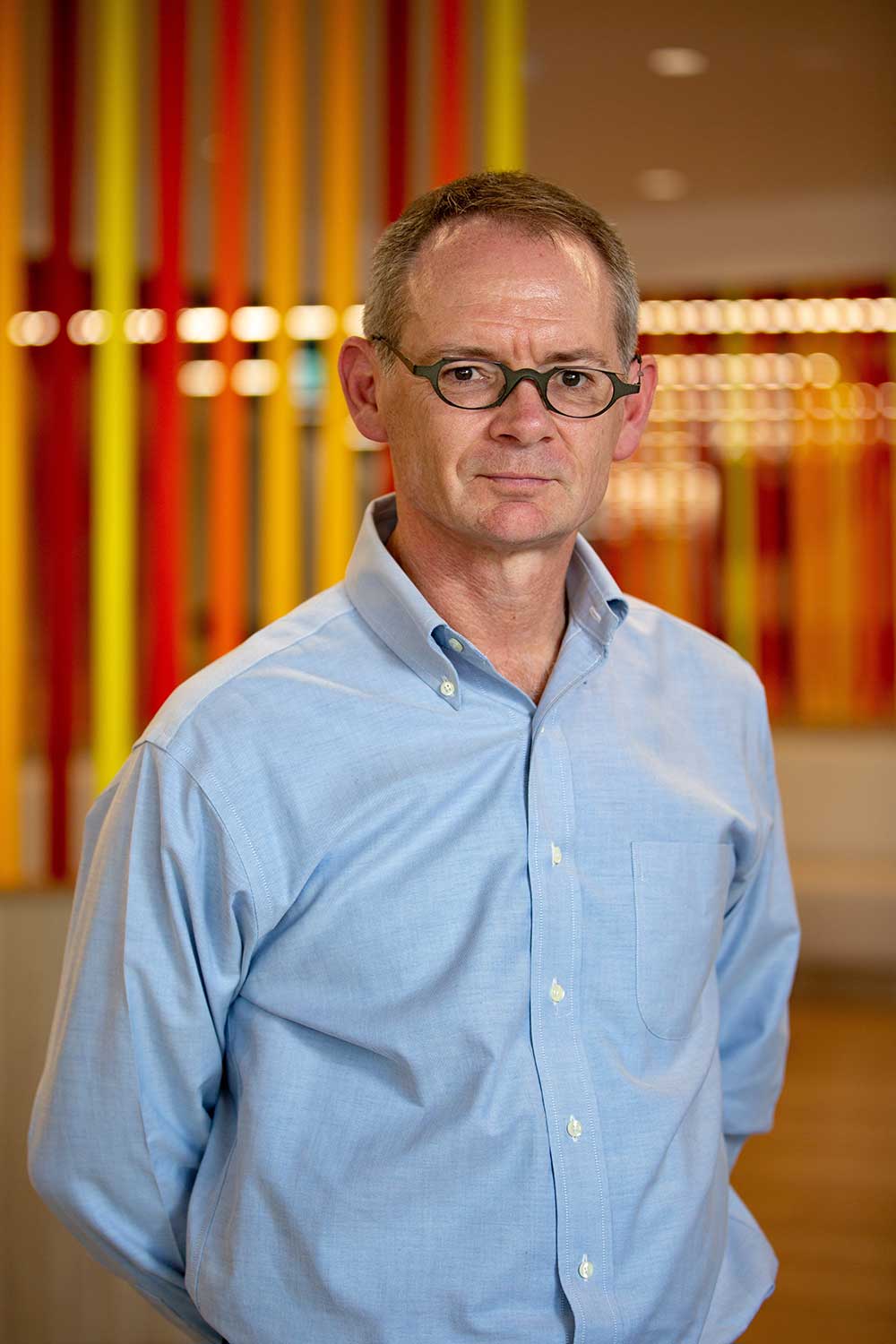
UNSW Scientia Professor Justin Gooding told create the project’s win was validation of the hard work the team has put in.
“I was so pleased that the team was recognised for what I think is really important work,” Gooding said.
“Commercialising research is a long and hard road, but commercialising research that can make people’s lives better is incredibly fulfilling.”
Understanding each other’s language
Building a device like RASTRUM involves a team of researchers from disciplines including health, biology and engineering.
“The big challenge in the beginning was to understand each other’s language and for the different disciplines to respect the challenges the others face,” Gooding said.
“This also crosses into the collaboration between industry and universities, where the academic researchers need to understand the commercial goals but the industrial team needs to understand the drivers that further an academic career.”
Dr Aidan O’Mahony, mechanical engineer and co-founder of Inventia Life Science, has been heavily involved in RASTRUM’s development. He told create he was impressed by the cohesion between the various teams.
“This is only made possible by our collaboration with Justin [Gooding] and [UNSW Professor Maria Kavallaris] and the team at UNSW,” he said.
“We’ve got a bunch of really highly skilled people working on this. It wouldn’t have been possible without everyone’s efforts on developing the technology and the product.”
Printing tissue
So how does one go about printing a tumour? It’s not too dissimilar to an inkjet printer.
“Essentially, we print very, very small droplets, about 25 nanolitres or 360 micron diameter, onto a culture plate,” O’Mahony said.
“When two droplets come together there’s a very fast chemical reaction that happens in the bio materials that forms a solid hydro gel.”
This creates a cellular matrix environment, which mimics an environment in the human body. From here, scientists can study how certain cells behave in the body or react to different stimuli, such as pharmaceuticals.
RASTRUM uses a bioink that was developed by Gooding and his team. But unlike an office printer, the final ‘print out’ can take a few days to develop, as the bioink bonds to form the matrix environment.
“For example, tumoroid models might take three or four days. The cells kind of communicate with each other as they come together,” O’Mahony said.
“It is a very weird and fascinating thing.”
Building a body
The Eureka Prize isn’t RASTRUM’s first award. In 2019, the team scooped up The Good Design Award of the Year.
And the little printer has come a long way in the three years since.
“In terms of design look and feel it hasn’t changed much, but we do have a much wider range of tissues that we can support now,” O’Mahony said.
“Back then, we had maybe two or three tissue types, now we have over 13 types.”
These include skin, brain, liver and breast tissue.
This library of tissue is likely to expand as researchers continue working on the project. Gooding believes the future potential of RASTRUM is enormous.
“Of the many potential applications, the one we are particularly interested in is personalising a person’s cancer treatment by being able to not only print model cancers but even perhaps use a patient’s own cells to print models of their cancer,” he said.
“This is important as then clinicians can trial different treatment regimes in a dish and perhaps facilitate better treatments and outcomes for the patient.”
RASTRUM’s commercial potential is also bright.
“We are currently expanding our global presence in the business, so we’ve just placed our first instruments in the US and Europe, which is really exciting,” O’Mahony said.
“We’re trying to ramp-up the technology that’s been developed in Australia. We still do all the assembly, testing and manufacturing of the instrument right here, which we’re really proud of.”