In recent years 3D printing has delivered several exciting developments, from organs to race cars. Now, it’s adding houses to its repertoire.
Dutch construction company Van Wijnen has partnered with the Eindhoven University of Technology to deliver five fully habitable, 3D-printed houses by 2019.
According Van Wijnen Manager Rudy van Gurp, Project Milestone (as it’s called) was in part a response to the shortage of people willing to take part in the laborious construction process.
“We need a technical revolution in the constructing area to respond to the shortage of skilled bricklayers in the Netherlands and all over the world,” he said.
Instead of the traditional road closures and heavy human labour associated with building developments, the elements of the houses will be created using the Eindhoven University of Technology’s 3D concrete printer (3DCP). The university’s 3DCP research program is a world leader in concrete 3D printing and has developed a printer big enough to create houses.
The printer is 9 m x 4.5 m x 3 m, and features a four-axis gantry robot connected to a concrete mixing pump.
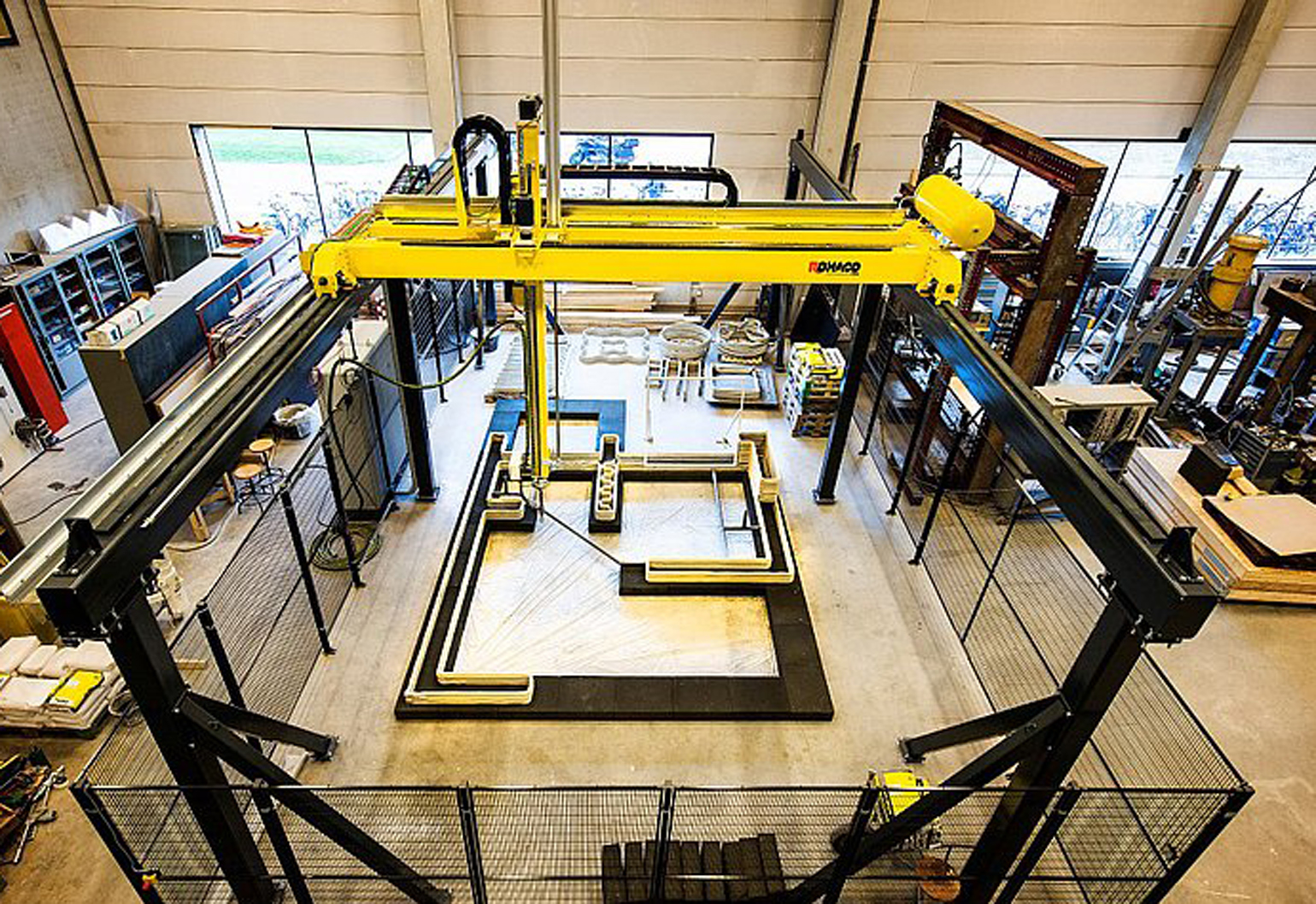
The first batch of homes will be one storey with three rooms, and only the exterior and interior walls will be built using the 3D printer. However, the developers plan to steadily increase the percentage of features created using 3D printing, until eventually everything, including drainage pipes and other installations, are built using this method. They also hope the final home can be printed on-site, rather than at the university.
Sustainable practices
In addition to satisfying the need for construction labour, using 3D printers as opposed to traditional building techniques could have significant environmental benefits. Using a 3D printer allows concrete to be placed where it’s needed, avoiding any unnecessary use or accidental wastage.
The 3D-printing process also allows concrete to be created with a wider range of functionality than traditional building products. Usually, walls need to accommodate for insulation and require an extra internal layer for acoustics. By incorporating these properties into one product, fewer materials are required and the building process is faster.
Rising demand for smart-home features can also be incorporated more easily into this design, such as embedded wireless sensors for controlling temperature, lighting and home security.
Design innovations
Beyond the logistics of producing the physical structure, 3D printing also frees designers from some constraints.
In the traditional pouring of concrete, the formwork determines the shape of concrete. With concrete prints, builders will soon be able to make concrete details as small as a pea, and round, hollow or convex shapes. This makes concrete buildings and constructions with completely new forms possible,” said the project’s developers.
Designers have taken full advantage of the creative opportunities that 3D printing affords, creating visually striking homes. Moving forward, van Gurp said 3D printing will offer greater flexibility in the construction process.
“We are already looking to a take a step further and people will be able to design their own homes and then print them out. People will be able to make their homes suit them, personalise them and make them more aesthetically pleasing,” he said.
The future
Eindhoven University of Technology has developed a research program aimed at establishing concrete printing as a “viable new method to manufacture concrete elements”. In addition to Project Milestone, they have also constructed a bicycle bridge using 3D printing.
While this one of the first examples of ‘printing’ habitable houses, a similar project is underway in the US. Earlier this year, Silicon Valley-based startup New Story announced a collaboration with construction tech company ICON to produce 3D printed houses. They have produced a bespoke 3D printer that can be transported on the back of a truck, meaning it can construct a house onsite in one day for approximately US$4000.
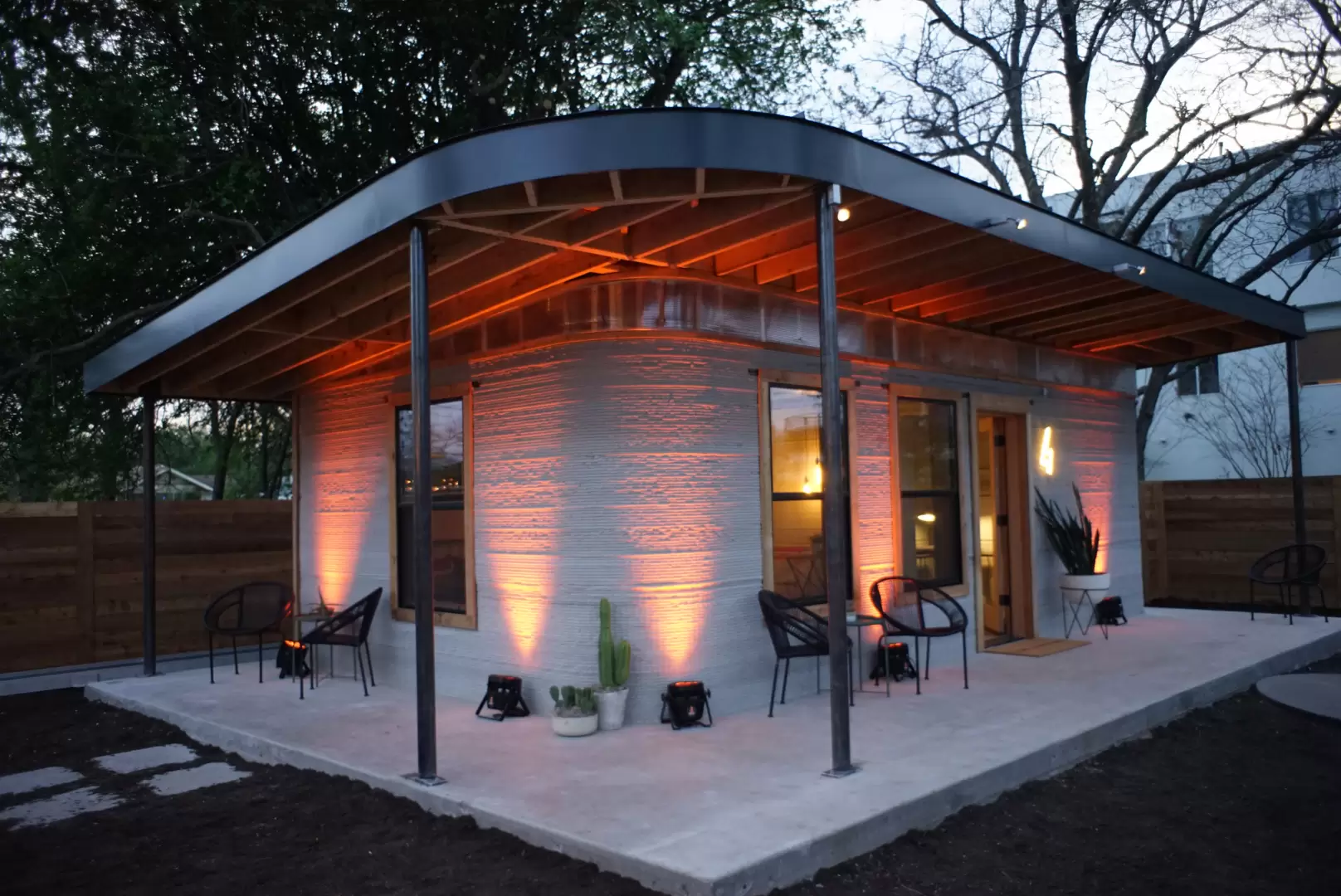
However unlike the Netherlands, where the number of construction workers is dwindling, construction can be a valuable source of employment in developing countries. This is an issue that New Story CEO Brett Hagler said the company “had to wrestle with a little bit”.
Ultimately, they concluded the benefits of accessible housing outweighed the decrease in the demand for labour, and noted the work that is required could provide long-term employment opportunities.
“You’re also supplying an advanced kind of technical job, which right now we don’t really do,” Hagler said.
“We think that will better position [workers] for what’s going to come in the next 10-20 years with AI and robotics. It would be amazing if the people in our communities already knew how to work with all that stuff.”
Those involved with the Project Milestone have similarly grand expectations, and believe this method of construction might soon become more widespread.
“At the moment, research costs and regulation restraints outweigh the benefits of 3D houses, but we may see mass production of these in the next few years,” van Gurp told CNN.
Interest in Project Milestone has already outstripped expectations. The homes will not be ready for occupation until 2019, but 20 potential tenants registered their interest within a week of prototype images being released.