A new method that allows robots to work concurrently on 3D printing concrete structures could bring on-demand design to construction sites.
The method known as ‘swarm printing’ enables robots to simultaneously 3D print concrete designs not attainable through traditional methods.
The process begins the usual way with a computer mapping out the design. It then assigns each robot arm specific tasks in the printing process to keep the arms from colliding or interfering with each other’s work.
Robots move into place and print their assigned parts, ensuring the joints between the separate pieces overlap. According to the developers, this is the first time multiple robots have printed simultaneously on a single concrete structure.
Leading the project is Pham Quang Cuong, an assistant professor at Nanyang Technological University’s (NTU) School of Mechanical and Aerospace Engineering. The team’s method was a success, enabling robots to 3D print a concrete structure measuring 1.86 m x 0.46 m x 0.13 m in just eight minutes.
After allocating two days to harden and another week to achieve its full strength, the concrete structure was ready for installation.
Robots, assemble!
This development builds on Pham’s earlier work creating a robot that autonomously assembled an Ikea chair. But according to him, this latest project was more complex in terms of planning and execution.
Refining learnings from the Ikea project, the NTU team increased the precision of the robot’s autonomous systems by incorporating localisation, collision avoidance and optimal robot placement – all working in tandem.
Developers hope this swarm printing technique addresses a common problem for existing 3D printing processes: scalability. For the most part, the size of a design is constrained to the chamber volume of the 3D printer.
“This issue is more pronounced in the building and construction industry, where it is impractical to have printers that are larger than actual buildings,” stated the research paper, which was published in Automation in Construction.
Other methods for 3D printing sizeable concrete structures are reliant on much larger printers, which would create space issues on cramped construction sites. Having multiple smaller robots enables 3D printing to be completed virtually anywhere, so long as there is adequate room for the robots to navigate around the work site.
Developers said this technique would be particularly useful for creating large structures like architectural features and specially designed facades on site.
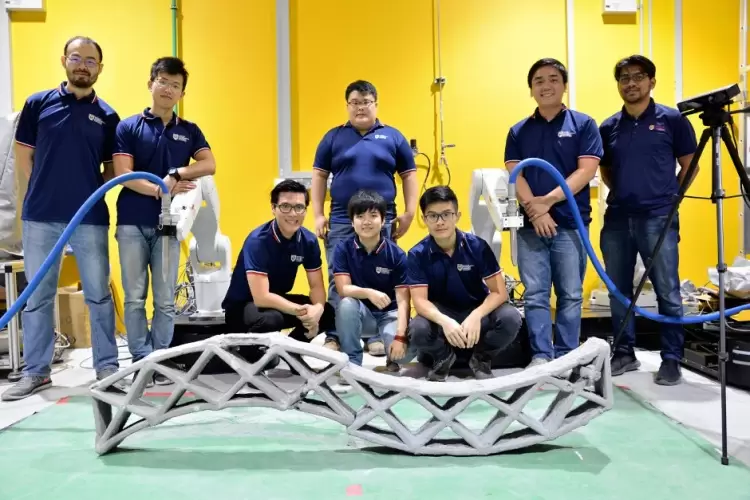
“We envisioned a team of robots that can be transported to a work site, print large pieces of concrete structures and then move on to the next project once the parts have been printed,” Pham said.
The path to commercialisation for NTU requires integration of more robots to print large-scale structures. Once this has been achieved, developers said they will focus on optimising the printing algorithms and refining the cement paste recipe to minimise errors and curing time.