Engineers have developed a soft robot that can burrow through sand and other difficult terrain.
Thanks to advancements in robotics we already have machines travelling on land, air and sea, but a team of engineers at the University of California, Santa Barbara (UCSB) and the Georgia Institute of Technology have cut through one of the final frontiers: granular, subterranean spaces.
Nicholas Naclerio, a graduate student focused on the mechanical design of soft robots at UCSB, said his team had developed a burrowing robot inspired by the natural world that overcomes the limitations of conventional robotics.
“The forces resisting subterranean movement are orders of magnitude higher than in air or water. For example, a human cannot dig a hole nearly as fast as he or she can run, or even swim,” he said.
“As a result, most methods of digging require heavy, powerful machinery like drills. While these tools are effective, they are limited in their ability to change direction underground and may not be the most practical for a small, exploratory robot.”
Another challenge of horizontal burrowing is that a symmetrical object moving horizontally through a granular media experiences a lift force.
“Unlike a gas or liquid, which can easily flow around an object, it is easier to push sand up and out of the way than it is to compact it down. As a result, an object travelling horizontally through sand tends to surface,” he said.
How it works
Just like a plant’s root, the robot extends from its tip.
“It does this by everting itself, passing new material out the tip,” Naclerio said. “This means that the sides of the robot remain stationary relative to its surroundings.”
No matter how long the robot is or the path it takes, it only needs to overcome the resistive forces at its tip, not the drag along its sides.
Another challenge the researchers had to solve was the resistive force encountered at the robot’s tip. They tackled this with granular fluidisation — something used in both the construction industry and by a type of burrowing octopus.
“The robot blows a jet of air out its tip that both excavates and fluidises the surrounding sand,” Naclerio said.
“The pressure from the air passing through the sand particles suspends them, like pucks on an air hockey table, allowing them to flow past each other like a fluid.”
Finally, Naclerio explained the engineers overcame lift forces created in horizontal burrowing through a clever use of air flow.
“By blowing air straight down, perpendicular to the direction of the robot, we can loosen up the sand beneath the tip of the robot, reducing the lift force that it creates,” he said.
“This enables controllable horizontal burrowing and turning. The asymmetry principle is also used by the sandfish lizard, a type of reptile that uses its wedge-shaped nose to help it burrow into sand.”
Shifting sands
The project came about because the engineers were interested in creating a model of plant root growth.
“We used the tip-extending principle of our device in another work to study how plant roots can passively grow around obstacles,” Naclerio said.
But horizontal burrowing proved much more difficult than expected, because the robot continued to surface.
“While prototyping with the robot we also did a series of controlled physics experiments. These experiments taught us about how fluid flow affects lift and drag on a rigid object moving through sand,” he said.
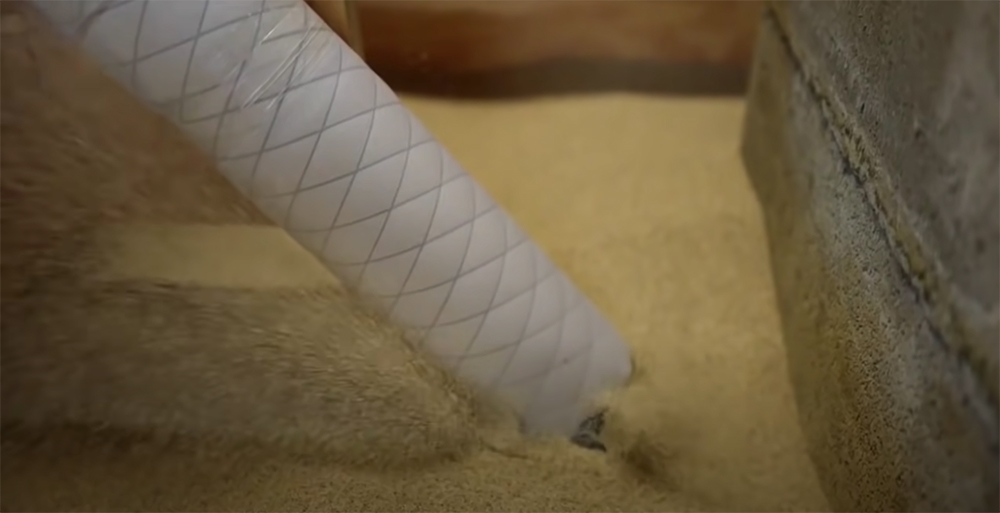
Tip extension and granular fluidisation offer several advantages over other methods. For example, by extending from the tip, the robot experiences no friction along its sides, meaning friction does not increase with length or path curvature.
And tip extension means the robot can turn in any direction, regardless of the path it has taken so far. Current methods such as directional drilling are limited to more gradual curvature.
“Our work presents a physics understanding of burrowing in granular media and applies the key results to design a soft robot that controls subterranean interaction forces to achieve fast, steerable burrowing in three dimensions,” Naclerio added.
Beyond our planet
Though the burrowing breakthrough may not be ideal for soil penetration beyond a few metres, Naclerio believes it offers improved performance in long, shallow, directional burrowing — and has plenty of potential applications in future.
“On Earth, these include soil sampling, minimally invasive irrigation, wire, or geothermal loop installation without trenches, erosion control, search and rescue, and granary inspection,” he said.
The method is also well suited for dry, low gravity, extraterrestrial environments, where reactive forces may be difficult to produce. In future, he hopes to examine integrating tip extension with conventional drilling and exploration technologies.
“Applications could include thermal sensor placement on Mars, volcanic tunnel exploration on the moon, asteroid sampling or anchoring, and granular ice exploration on Enceladus, a moon of Saturn,” he said.
Naclerio believes the research will open up a whole new field of inquiry into the systematic study of physical phenomena that can improve the performance of robotics, and how robotics can be used to study natural systems.
“We are excited to explore other mediums, fabrication methods and force-reduction techniques, as well as a more in-depth study of the physics of local fluidisation in granular media,” he said.
“We also plan to study the performance of this device in lunar soil simulants and low gravity.”