This Australian company has developed a stationary battery that is greener, safer, and potentially even cheaper than its competitors.
Six years after it was spun out from research developed at the University of Sydney, Australian battery company Gelion has listed on the London Stock Exchange.
The move presages big things for the start-up, which is developing for commercial use a zinc-bromide battery that is safer and has a higher energy density than its lead-acid counterparts.
Structured like a lead-acid battery — the kind used in cars and which have a comparatively low energy density — Gelion’s battery is used for stationary energy storage.
“That market is dominated by lithium-ion batteries and, to a lesser extent, lead-acid batteries,” Gelion CEO Andrew Grimes, a chemical engineer, told create.
“The zinc-bromide chemistry brings some really unique advantages that address a lot of the traditional problems around those two techs.”
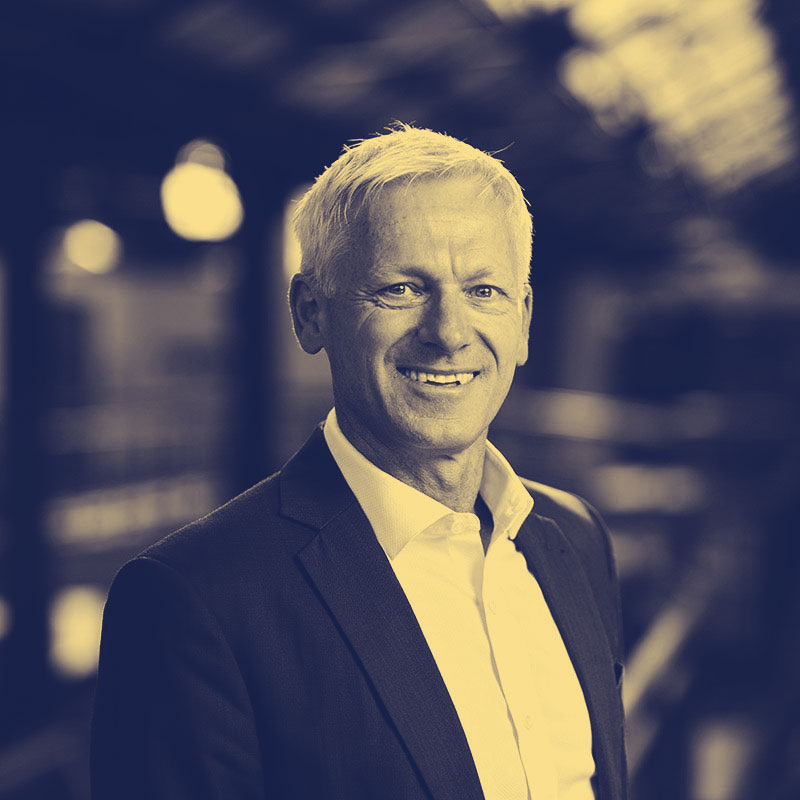
These advantages include durability and safety — the Gelion battery cannot catch fire — as well as environmental friendliness and, when produced at sufficient scale, lower cost.
“It’s very hard to damage the batteries,” Grimes said.
“They can be operated across a very wide temperature range, number one. They can be discharged down to zero, number two.”
That distinguishes the technology from both lithium-ion and lead-acid batteries, which cannot be discharged below a certain point.
But the technology’s biggest selling point is its safety. Fire is a significant risk for current stationary battery technology, as illustrated by a blaze at Moorabool’s Victorian Big Battery site this past September, which saw two Tesla Megapacks ignite.
“Our batteries won’t catch fire,” Grimes said confidently.
“They can be operated across a wide temperature range, which means that you don’t have to spend all that money that you have with lithium- ion batteries on air-conditioning systems to keep them inside a very tight range.”
One test the company conducted involved heating its battery on a hotplate to 700°C.
“Even as the battery starts smoking and charring, it’s still continuing to operate,” Grimes said. “It’s really incredible to see.”
The safety offered by the zinc-bromide technology has immediate benefits, but it could also help increase the take-up of other technologies, such as charging stations for electric cars.
Batteries with a high fire risk cannot be placed in places with strict building codes, for instance, which could prevent charging stations from being installed where people need them.
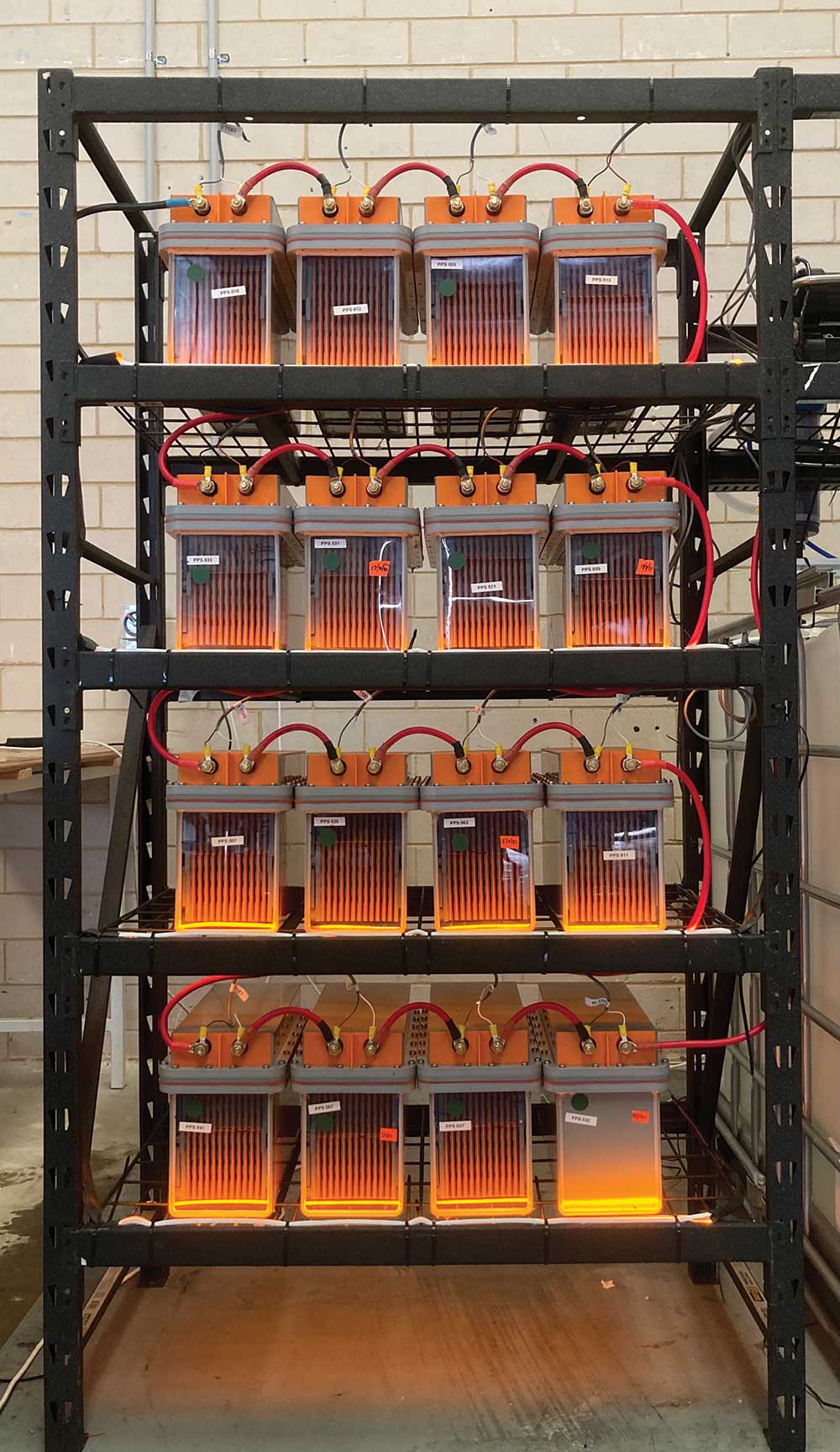
“That’s one of the applications that we’ve already been having some discussions [about] with some of the large commercial building developers, and they’re really interested because I think you would struggle to get approval to put a lithium-ion battery in the basement of a big building,” Grimes said.
“The advice, if you have a lithium-ion fire, is just stand back and let it burn because you can’t put it out — that’s actually the official advice from the fire agencies. So I don’t think that they will ever be in a position to get lithium-ion batteries into buildings in that sort of way.”
The particular properties of Gelion’s zinc-bromide battery are the result of technology devised by the company’s founder, University of Sydney chemist Dr Thomas Maschmeyer.
Maschmeyer first became interested in the possibilities of zinc-bromide batteries when he was asked to work on a bromine flow battery. The flow approach — which used electrolytes — did not work out, but Maschmeyer decided to explore an alternative.
“I came up with a gel approach — a nano-structured electrode approach — that took care of keeping everything very well and equally distributed in the battery during the various charging operations and that would be a simpler format to manufacture and to operate,” he told create.
The gel started as the product of an in inconclusive experiment Maschmeyer had worked on with a student.
“We tried to separate chemicals with what’s called a self-supporting anionic membrane,” he said.
“It was a liquid salt in a gel that was designed to separate chemicals as a membrane from one side to the other — and was a complete failure.”
The experiment used red and blue dye, and during its course, Maschmeyer found the different colours had different charges.
“I thought, right, this is completely useless from any kind of application point of view right now,” he said.
“I had that in my mind for a few years, and then came this flow battery situation and I thought, well, all I need to do is control charged species in a certain manner, and this thing would actually do it.”
Maschmeyer emphasises the important role engineers have played in translating the technology, and he appreciates having a chemical engineer in the company’s CEO position.
“He can … speak to me and I can speak to him, we understand what we’re saying,” he said of Grimes.
“The more mature the company becomes, the more important the engineering side gets.”
“The chemists generally handle the project first, and then once they get it to a certain level … it gets passed over to the engineers,” Grimes said.
“It never leaves the chemists — you’ve always got this interaction between the two groups — but as soon as you’re talking about processing, as soon as you’re talking about scale-up, that’s when you’ve got the domain that more traditionally sits with the engineers.”
The next few years for the company will involve scaling up and commercialising, Grimes said, a process that will be helped by the injection of funds from the company’s stock exchange listing.
“We are in the process of building a factory to manufacture zinc-bromide batteries,” he said.
“Getting those out and getting full-size battery systems into the hands of our customers, and then getting approvals for that.”
Grimes sees the batteries as having a use anywhere that stationary energy storage is required.
“Anything from something that might go into a house up to the large multi-shipping container size batteries that support solar and wind farms,” he explained.
“Because of the robust nature, we’re particularly suited to some of the Australian applications like off-grid outback. There’s a lot of work being done at the moment on replacing poles and wires with standalone power systems.”
“Diesel [generator] sets are a sweet spot for us because that’s expensive energy, expensive electricity, especially in off-grid situations,” Maschmeyer added.
“But increasingly, as our volume goes up, we will be targeting larger installations — so where initial installations might be between the 20 to 200 kWh, once we get the manufacturing volume up, we can go to the megawatt hours.”
He also points to energy-shifting applications — deploying power collected from solar farms at night, for instance — and green hydrogen as other possibilities for the technology, while Grimes said it could be applied to desalination and other agricultural activities.
“Australia, although it’s not our only market, as a first place for us to start commercialising, it’s a really, really great market for us,” Grimes said.