At this week’s ACAM 2024, Professor Stefanie Feih will explain the essential role biomechanical engineers play in working for the ultimate human outcome.
Often engineers are one step removed from having a direct impact on humans, according to Professor Stefanie Feih FIEAust, Professor of Mechanical Engineering and Director of the Advanced Design and Prototyping Technologies Institute (ADaPT) at Griffith University.
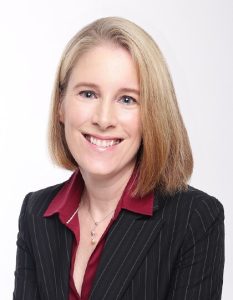
“I’ve worked in a lot of different sectors, including aerospace, naval structures and offshore oil and gas, and of course we consider the safety of the structure and the people interacting with it,” Feih, a thought leader in the optimisation of lightweight structures, told create. “But you’re always one step away from humans.”
However, in the field of biomechanics, which is the focus of Feih’s work at Griffith University, everything is patient-specific.
“You’re actually designing with the human in mind,” she said. “That is very different, and it creates an emotional connection and a deeper level of engagement and satisfaction.
“At the same time, it’s also very much about hard engineering. We can’t look at materials, structure and manufacturing in isolation. We need to consider them holistically and make sure we have a good numerical analysis approach that’s validated.”
The right material
At ACAM 2024, Feih will offer listeners an illustration of how the development of biomechanical structures — items to be implanted into human bodies to bring outcomes around health and quality of life — is not far removed from the work she did on major structures.
“My focus was always on what is the right material, what is the right structure for that target application and what is the right process to actually manufacture this component,” she explained.
“In biomechanical structures, the skills are similar even though the constraints are different. Materials need to be biocompatible. It might be an implant or a bone plate, in which case we’re talking about osseointegration. A living material must be allowed to grow into that structure, which is [about] enhancing osseointegration.”
The skills, knowledge and insight Feih gained in the broader mechanical engineering sector have been instrumental in her current work in biomechanics.
This is particularly true in the area of testing and proving of materials, designs and manufacturing processes — particularly the 3D printing of biomechanical structures.
Mechanical engineers are essential
“We talk about the reliability of the manufacturing process a lot,” Feih said.
“In an aerospace structure, you have an inspection interval and the maintenance process is well defined. But in a human body, you definitely don’t want anything to break and, in many cases, you don’t want the implant to be too stiff. We want to match the stiffness of the bone, for instance. So biomechanical structures have strict manufacturing constraints.”
Mechanical engineers are in a powerful position to have a positive influence on the future directions of biomechanical structures, she believes.
“This is true for mechanical engineers, electrical engineers and mechatronics engineers,” Feih said. “I’d say it’s easier to explain biomedical concepts to people with an engineering background than vice versa.”
Testing is the holy grail
A clear understanding of the value of numerical simulation linked to experimental characterisation, and the processes required to conduct such validation studies thoroughly, is vital in biomechanical engineering, Feih said.
“I’m very scared when people present simplified simulations without sufficient experimental validation,” she said.
Each time a design is optimised, it must be revalidated because an engineer can never be sure if they have moved outside the realm of the prior numerical simulation validation.
“In biomechanical device manufacturing, advanced manufacturing processes such as additive manufacturing are typically not yet approved and applied,” Feih explained. “So we mill, we drill, we do the typical things.
“The problem is that these engineered structures, like many other engineered structures, are over-designed in terms of stiffness.
“A bone does not have a Young’s modulus of 110 GPa, which is titanium, or 210 GPa, which is stainless steel. Bone is closer to something like 20 GPa, and when we are looking at paediatrics it can be as low as four or five GPa. How do we match this with metallic implants?”
In the biomechanical engineering space, there are numerous problems yet to be solved, and mechanical engineers will be vital in the development of those solutions.
“Because it’s so personal and has such a direct impact on humans, if we can open up the biomechanical engineering space I think it will attract the younger generation, and especially women, to study engineering,” Feih said.
Feih will be communicating the connection between great engineering design and positive human outcomes at ACAM 2024.
Register for ACAM 2024 here. Full conference and single-day registrations are available. The conference runs from 7-9 February.