A dynamic manufacturing sector can bring a pandemic-weakened Australian economy back to full strength. The support of business and government will ensure the nation can make the most of the opportunities on offer.
The year 2020 might be remembered as the one when Australia remembered the importance of manufacturing — a part of its economy it had allowed to wither.
In October of that year, the Australian Government announced a strategy to focus on six sectors in manufacturing, described as areas of “comparative advantage and strategic importance”.
These areas are: resources technology and critical minerals processing; food and beverages; medical products; recycling and clean energy; defence; and space.
“We make things in Australia. We do it well,’’ said Prime Minister Scott Morrison at the launch of his government’s Modern Manufacturing Strategy.
“We need to keep making things in Australia. And under our plan we will.”
Since then, the Australian Government has opened applications for grants under its $1.3 billion Modern Manufacturing Initiative to its chosen sectors, as well as releasing 10-year road maps for each.
There are many ways to look at the current moment for Australian manufacturing, which the Department of Industry says is worth six per cent of national gross domestic product and employs 862,200 Australians.
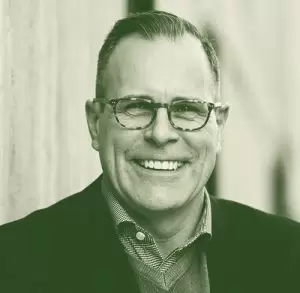
Dr Matthew Young, Manufacturing Innovation Manager at the Innovative Manufacturing Cooperative Research Centre (IMCRC) and a former Materials and Process Engineering Lead at Boeing, believes that the COVID-19 pandemic has opened a unique window of opportunity for the industry.
It is, he told create, “a chance for companies to rethink their approach to manufacturing — how and where they make their goods — to future-proof their business strategy, and for government to provide the focus, support and environment to grow Australia’s manufacturing sector, and thus drive economic and social recovery”.
The Government’s declaration of manufacturing as a sovereign capability and its outline of its Modern Manufacturing Strategy was a first step, he said.
“Yet more needs to be done — on all sides — to build a strong, resilient and globally competitive Australian manufacturing industry.”
John Sordo, Manager, Marketing and Product Management, at manufacturing company ACO Australia, said there’s a lot of goodwill but also a lack of coordination between different levels of government, with prevailing disadvantages for local companies wanting to supply major projects. He agrees that more needs to be done.
Among this is spreading a greater appreciation for the economic multiplier effects of keeping manufacturing in Australia to support construction, which has substantial links with many other sectors throughout the economy.
Its output stimulates more economic activity across society than any other sector, Sordo said.
“Construction is an area where the government invests a lot. We’re always building roads, we’re always building infrastructure, and there’s local manufacturers that can supply that,” he told create.
“I just think we’re all missing something here, because this is the sort of stuff that gives an economy resilience. You take manufacturing out of an economy, then we become a very simple economy and vulnerable to what happens in the world.”
The skills speed bump
A focus on research and development (R&D) is vital for a manufacturer, said Trent Alexander TMIEAust, Group Improvement Manager, Concrete Products, at construction material manufacturer Brickworks, adding proudly that his company released 100 new products during a difficult 2020.
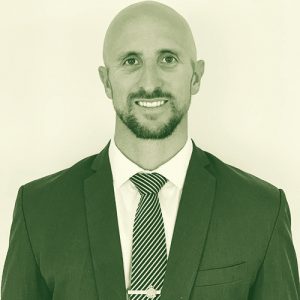
Investment in R&D on recycled materials is “massive at the moment — absolutely massive”, he told create, adding that this investment is driven by customer demand.
“We’ve been quite active on that, actually, even before [the pandemic],” he said. “For example, on a lot of our concrete masonry products, we will utilise power station waste in the form of ash. We’ve recently been utilising recycled glass from bottles.”
Geosynthetics manufacturer Geofabrics is in the middle of an AMGC-backed project to develop an automated robotic cell that can produce laminated, thermally bonded geocomposites, which are increasingly specified by civil engineers but are currently imported.
Executive Director, Sales and Business Development, Peter Tzelepis described adopting robotics as part of a sustainability push: delivering better-quality products more efficiently and making employment at his company and its suppliers more sustainable.
“[Local] procurement means local employment and improving local skill sets in regional areas. So, for machine operators, it gives them an opportunity to be retrained, to undertake courses and to modernise their skill sets as we modernise our workplace,” he said.
“How we made products 10 years ago will be different to how we’re making them in the next 10 years, with investments not only in the equipment but [also] our people, by improving their skill set.”
After the worst of the pandemic, manufacturing is currently in a rebound.
The March Performance of Manufacturing Index from the Australian Industry (Ai) Group showed a sixth straight month of growth, and the sharpest rate of expansion since March 2018.
The Ai Group cautioned with its March 2021 results that growing pains were becoming apparent among survey respondents, “with reports of skill shortages becoming more widespread”.
Finding and retaining engineering talent, especially with manufacturing experience, is a challenge, according to Brickworks’ Alexander. The issue goes downstream too, with shortages at installers such as bricklayers.
He added that it’s become harder over the years to find certain plant and equipment items in Australia.

ACO Australia.
Sordo, from ACO, which makes products for drainage and utility enclosures, said one difficulty continues to be competition with cheap imported products.
“We’re very strong in the specification area. So, engineers who are members of [Engineers Australia], for instance, are very happy to specify us, because we offer services to help integrate our product into their designs,” he said.
“The disconnect comes when the project goes out to tender, and the contractor will shop the product around without understanding why the ACO product was specified in the first place. The contractor then, in essence, moves away from the engineer’s original design brief and compromises the project just to make some additional profit. Sadly, the contractor rarely is held accountable.”
He shares a story about an 8 km drainage project along a prominent Western Sydney arterial road. His company lost out by three per cent to an international product, which then saw supply delays and a budget blowout for the contractor.
“Not only did the contractor end up paying more due to the blowout but we missed out on the job. Our entire Australian-based supply chain did as well,” he said.
“The road owner was a government authority which had the ACO product on a pre-approval list. So, there was no political support in a way that would possibly mandate the construction industry to buy Australian. And there was no incentive for the contractor.”
Encouraging the purchase of locally made goods is obviously popular with local companies. Advantages given include the products’ fit with Australian Standards and local installation methodologies, the manufacturer’s closeness to the customer — geographically and linguistically — and the boost given to the local economy.
“As a business, we certainly actively support Australian-made … where we can,” Alexander said. “We’d like to see more government support pushing Australian-made. That was a really big theme in the ’90s. We certainly have a plethora of products that are manufactured in Australia, and we want to keep doing that for the next few decades or longer.”
Testing times
Challenges also remain for manufacturers in other sectors. One problem is that infrastructure limits can have far-reaching implications, as seen by the potential closure of a testing facility in Sydney’s Lane Cove.
Plans to close the High Power Testing Station, which provides certification testing to Australian and international standards for electricity transmission and distribution network equipment, have attracted concern from industry and other stakeholders, including Engineers Australia.
“This capability is a critical function for the testing of new electrical equipment, which is often mandated by Australian and New Zealand design standards, and in some instances by government regulation,” said Engineers Australia’s Chief Engineer Jane MacMaster.
“There are many Australian manufacturers who support the transport, energy, infrastructure, defence, mining and heavy industries sectors who require this unique facility for equipment testing.”
Engineers Australia has been approached by a large number of its members and partner organisations who have concerns about the implications of the closure. These include a significant increase in the cost and time needed to certify new systems if companies are forced to use overseas facilities for electrical testing.
This could lead to reduced testing regimes or companies withdrawing from domestic production altogether.
In response, Engineers Australia has sent letters to key government ministers at state and federal level, as well as other stakeholders, including chief scientists and business associations.
Ai Group and Engineers Australia have also formed a working group of industry experts to explore sustainable long-term business solutions to keeping the facility in operation.
Responding to the concerns, the Ausgrid-operated Plus ES, which owns the facility, will complete all existing work orders and delay closure until October 2021.
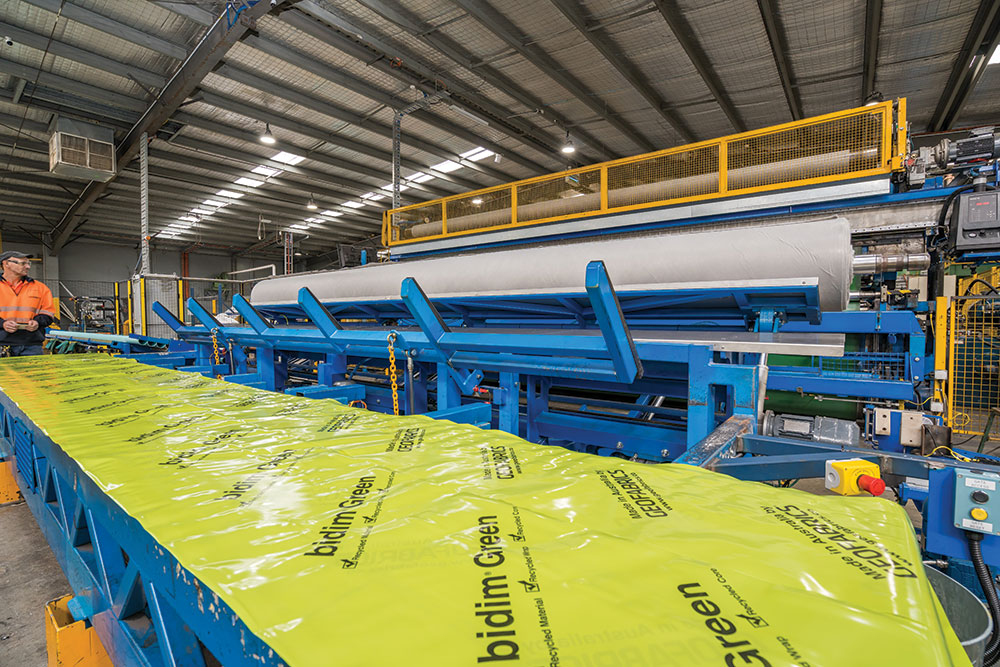
Recycling and development
Geosynthetics manufacturer Geofabrics has invested in R&D for new products using recycled materials.
Its “recycling journey,” as Executive Director Peter Tzelepis MIEAust calls it, began in 2019 with work on Bidim Green. This is a recycled polymer version of Bidim, the non-woven textile that is the company’s top-selling product and is used in a variety of civil engineering construction projects.
Tzelepis said there’s a “long series of products” based on recycled materials to be introduced into the market. Currently there are three: Bidim Green, a paving product called Sealmac and pipe product Megaflo. Another three will launch soon. Initially the company’s challenge was finding suppliers of good-quality recycled PET plastics. This is still a challenge, but the uptake of recycled plastic by companies has presented a new issue.
“We are competing with a lot of other companies. Not in our field specifically — whether it’s the food industry or other sectors — that want recycled plastic and we’re competing with them,” Tzelepis told create.
“But it’s great that we’re competing for something that would traditionally be sent to landfill.”