Australian engineers have developed a circular economy solution for disposable face masks in a bid to tackle pandemic-generated waste.
A world-first study by RMIT University researchers has shown that using recycled face mask material to make just one kilometre of a two-lane road would use up about three million masks, preventing 93 t of waste from going to landfill.
The mix of shredded single-use face masks and processed building rubble meets civil engineering safety standards for road materials. Analysis shows the face masks help to add stiffness and strength to the final product, which is designed to be used for base layers of roads and pavements.
Dr Mohammad Saberian, a research assistant at RMIT’s School of Engineering, said that multidisciplinary and collaborative approaches are needed to tackle the environmental impact of COVID-19 — particularly the risks associated with the disposal of used personal protective equipment (PPE).
“This initial study looked at the feasibility of recycling single-use face masks into roads, and we were thrilled to find it not only works, but also delivers real engineering benefits,” he said.
“We hope this opens the door for further research, to work through ways of managing health and safety risks at scale and investigate whether other types of PPE would also be suitable for recycling.”
The use of PPE has increased dramatically during the COVID-19 pandemic, with an estimated 6.8 billion disposable face masks being used across the globe each day.
How it works
Processed building rubble — known as recycled concrete aggregate (RCA) — can potentially be used on its own for the three base layers of a road, maintaining the necessary strength and flexibility to withstand the pressures of heavy vehicles and prevent cracking.
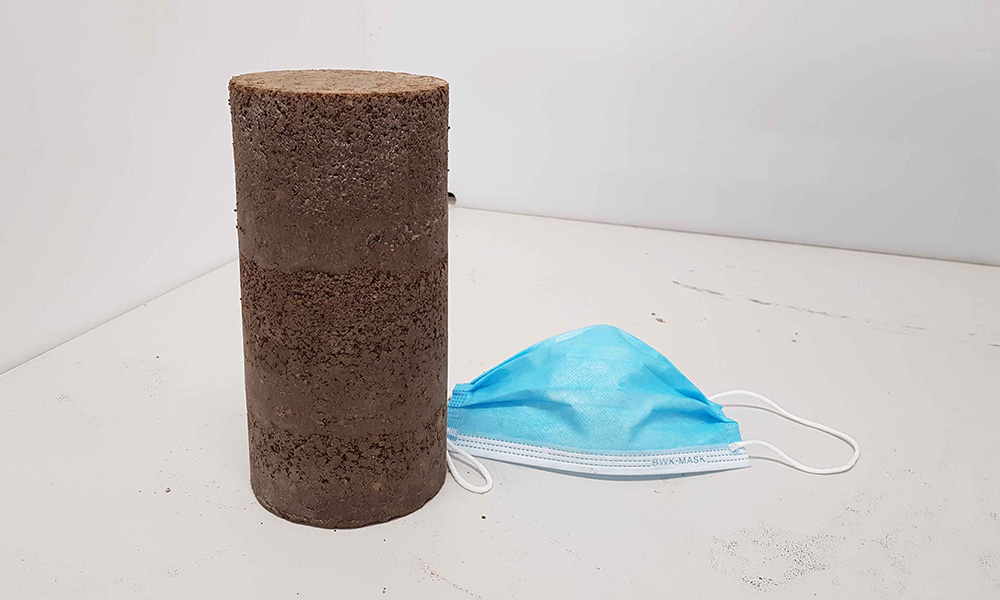
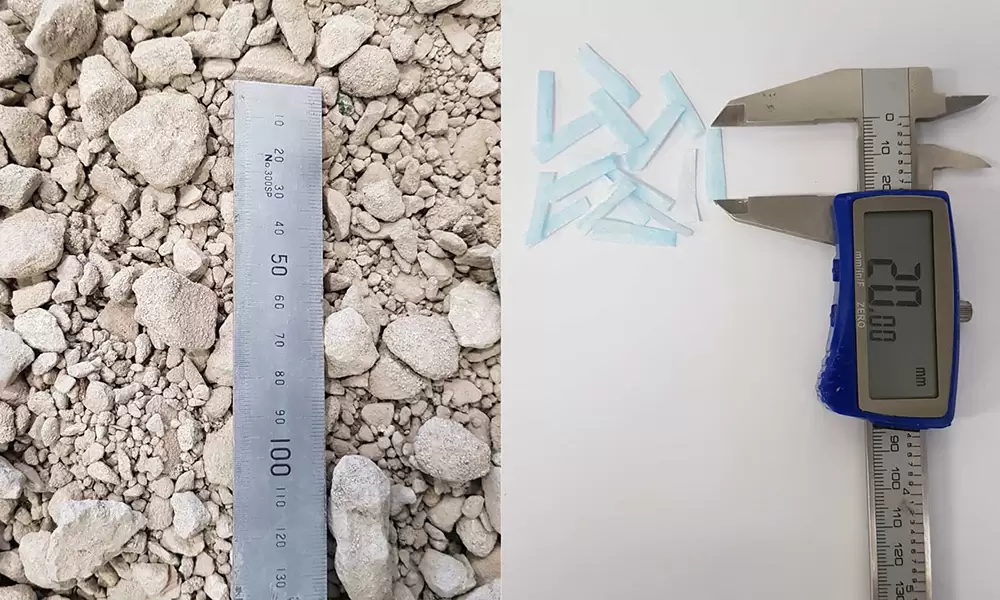
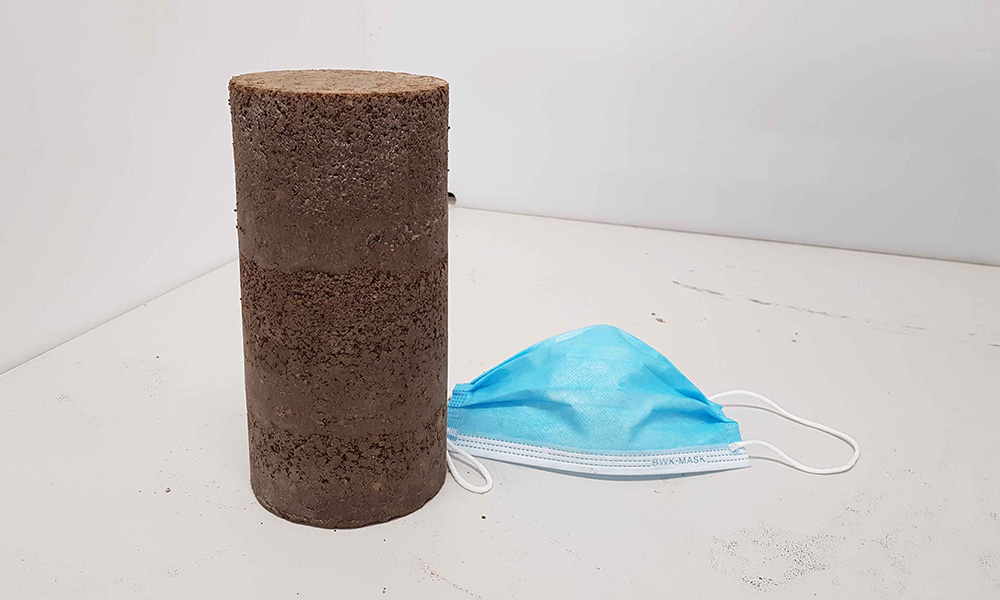
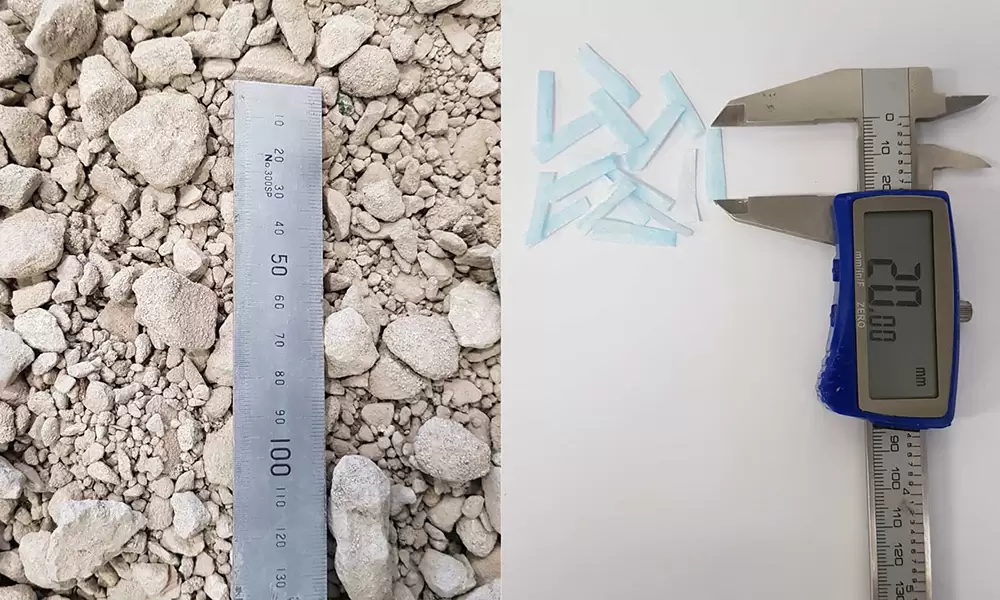
However, the researchers found that adding shredded face masks to RCA enhances the material while simultaneously addressing environmental challenges on two fronts: PPE disposal and construction waste.
The optimal mixture — 1 per cent shredded face masks to 99 per cent RCA — delivers on strength while maintaining good cohesion between the two materials.
Construction, renovation and demolition account for about half the waste produced annually worldwide, and in Australia, about 3.15 million t of RCA is added to stockpiles each year, rather than being reused.
The mixture performs well when tested for stress, acid and water resistance, as well as strength, deformation and dynamic properties, meeting all the relevant civil engineering specifications.
Other concrete proposals
In related research, the RMIT engineers also investigated the use of shredded disposable face masks as an aggregate material for making concrete, with promising preliminary findings.
Professor Jie Li said his team was inspired to look at the feasibility of blending face masks into construction materials after seeing so many discarded masks littering their neighbourhoods.
“We know that even if these masks are disposed of properly, they will go to landfill or they’ll be incinerated,” he said.
“The COVID-19 pandemic has not only created a global health and economic crisis, but it has also had dramatic effects on the environment.
“If we can bring circular economy thinking to this massive waste problem, we can develop the smart and sustainable solutions we need.”
Researchers at Swansea University in the United Kingdom are also looking for solutions to disposable PPE.
They have developed a new technique that would turn single-use COVID-19 face masks, plastic aprons and visors into green fuel. The research builds on the team’s previous work on generating hydrogen from waste plastics, called photoreforming.
This involves using a photocatalyst — a material that absorbs light and can convert it into energy to promote chemical reactions — such as breaking down plastic PPE and water into hydrogen.
Although the research is at an early stage, the researchers hope they can eventually develop a low-cost device similar to a washing machine that people could use to convert their waste into value.
Converting used PPE to building materials isn’t circular because it isn’t being converted back to its base/constituent materials and it can’t be repurposed again once it’s used as a building material. Also, how will the micro-plastics from the PPE be stopped from getting into the environment? This is really just moving the problem to somewhere else.