Architectural engineer Daniel Prohasky MIEAust is using advanced manufacturing techniques to create curved concrete panels that reduce waste and carbon emissions.
Prohasky, a lecturer for Swinburne University’s Architectural Engineering degree and member of Engineers Australia, told create he helped develop the core technology for Curvecrete while working as a research assistant at the University of Melbourne.
The Curvecrete concept earned Prohasky the 2019 Veski Fast Smarts Innovator of the Year Award when he first presented it during Melbourne Knowledge Week. For this year’s Knowledge Week next month, his team will display their 12-panel curved concrete showcase. This is a demonstration of how future building facades could be made from low-carbon, robotically manufactured materials.
“I’ve always been building things and passionate about finding better ways to build things. Now it’s more about how you could build something that’s magical and unexpected,” Prohasky said, adding that this can be achieved by engineering new robotic construction methods.
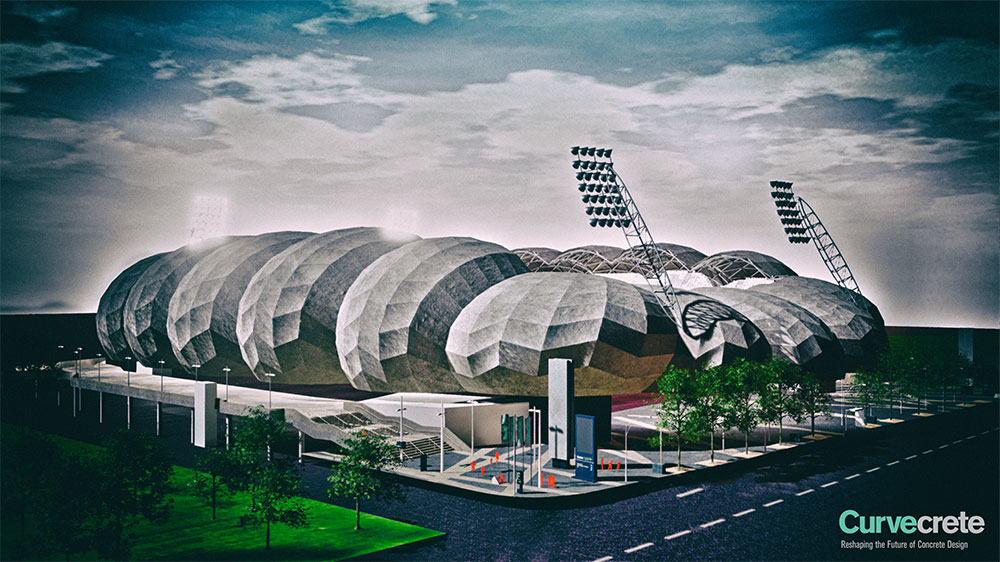
Form and function
As well as civil engineering qualifications, Prohasky has a background in aerospace engineering and architecture, and is a self-taught roboticist. He describes himself as a multidisciplinary integrator between architectural design and engineering.
“You can’t just start with a form, you have to think about what problem it is solving,” he said.
With Curvecrete, Prohasky and co-inventors Paul Loh and David Leggett set out to solve the problem of the waste generated by concrete. Of the 24 million cubic metres of pre-cast concrete produced in Australia each year, the formwork, or mould, makes up about 15 per cent of concrete waste by weight.
Curvecrete uses a parametric adjustable mould (PAM) CNC machine to manufacture double-curved concrete for non-structural building elements, such as facades and internal features. This has the potential to reduce the demand for pre-cast concrete.
Prohasky said Curvecrete also reduces the carbon emissions involved in producing concrete by about 80 per cent by using a 50:50 ratio of waste fly-ash (from coal-fired power stations) and blast furnace slag (from steel manufacturing) to replace conventional cement mix.
As well as creating an impressive visual effect, Prohasky explained that the curved panels are much stiffer relative to their mass than flat panels, and do not require steel reinforcement. They can also be thinner and lighter than flat panels, as the arching action reduces stress on the panel.
This property has been used for centuries in the inverted catenary curve found in ancient cathedrals and domes, and in more modern bridges and other structures.
Loh and Leggett are continuing their research at University of Melbourne and getting students involved in experiments to find new ways to use robotically-manufactured curved concrete. While they’re not involved with Curvecrete commercially, the team is looking at ways to work together on future demonstrations of the technology.
Chicken and egg
Curvecrete is creating not just a product, but an advanced manufacturing process, Prohasky said. His company’s greatest engineering challenge has been to set up the robotic production line while delivering on projects that require curved concrete panels.
In future, Prohasky plans to apply the process developed for Curvecrete to make manufacturing of other construction materials more environmentally and economically sustainable.
“We need to prove the robotic technology is practical for commercial products,” he said.
And this is underway, as Curvecrete embarks on its first commercial projects, which will create a new communal area for residents. Prohasky expects construction to start later this year, and has discussed other commercial opportunities with Invest Victoria.
The company has also worked with architects to study how Curvecrete could be used in the facades of buildings, such as Melbourne’s AAMI Park, if they needed to be replaced.
Big things on the horizon
Last year, Skalata Ventures invested $100,000 in Curvecrete, and the company recently completed a six month program to scale up its production facilities and commercial governance. As it grows, the business is looking to add to its team of engineers, particularly in the mechatronic, mechanical and electrical disciplines.
Prohasky is also working with the Materials and Embodied Carbon Leaders’ Alliance (MECLA) to help the New South Wales government drive down the construction industry’s greenhouse gas emissions.
In the longer term, Prohasky has his sights set on taking Curvecrete’s innovative process and product much further —to construction projects not just on Earth, but the Moon, Mars and beyond.
“It’s early days, but we’re starting to have conversations about how this might be possible,” he said.