Australia’s states and territories have agreed to ban the export of waste by 2024, meaning the country must find ways to deal with the plastic, paper, glass and tyres it would usually ship overseas. With just four years until the deadline, engineers will be instrumental in finding solutions to turn this trash into treasure.
Unprocessed glass will be banned from export from 1 January 2021, followed by mixed plastics, whole used tyres, single resin/polymer plastics, and mixed and unsorted paper and cardboard.
So, how can engineers address this issue and stop Australia from drowning in recyclable waste?
The construction industry provides one avenue for innovative waste solutions. Geofabrics Australasia, an Australian manufacturer and distributor of geosynthetics for the building and infrastructure sectors, incorporates recycled polymers in a number of its products.
This includes in its geotextiles, which are permeable materials typically used for filtration and separation, for example to prevent soil erosion or moisture loss.
“Early in 2020, we brought to market a geotextile, for the first time in Australia, that includes Australian recycled plastics,” said Dennis Grech, CEO and Managing Director of Geofabrics.
“We feel a real obligation as a business to innovate at reducing waste to landfill and eliminating plastic waste going into our waterways.”
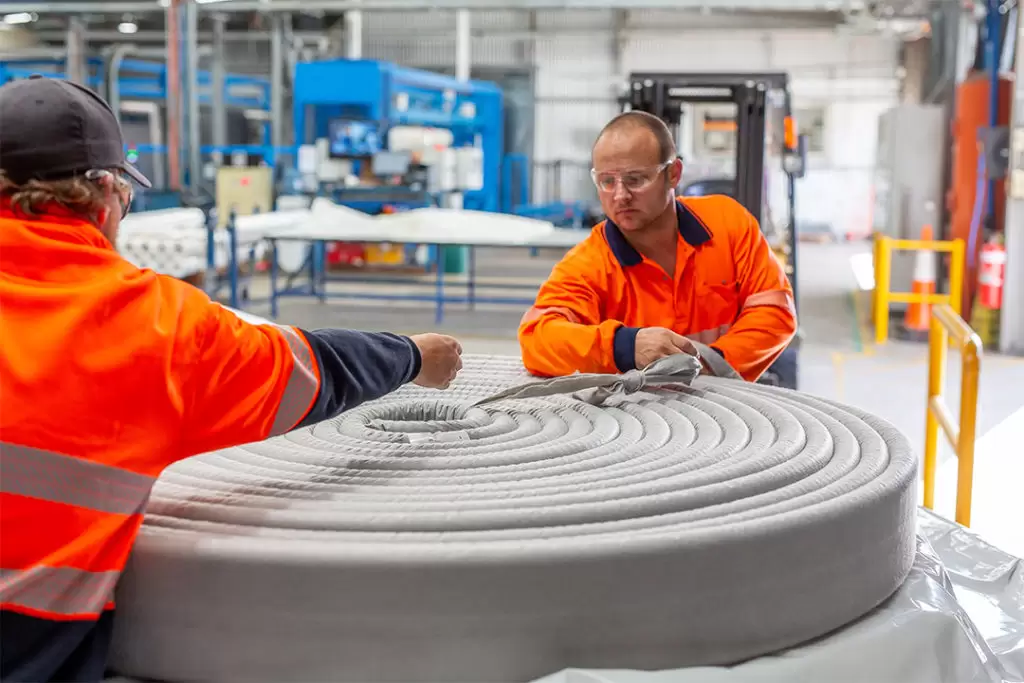
The company also recently signed a long-term supply agreement with packaging company Visy.
“Visy uses food-grade recycled PET in the manufacture of its plastic bottles,” Grech explained.
“The partnership between us and Visy is such that where the recycled PET is not fit for bottles, Geofabrics purchases that recycled PET to use in manufacturing our geotextile.”
Geofabrics also produces paving fabric and pipe products made from recycled materials.
“A number of customers, including government infrastructure projects and large contractors, are opting for the green product range, which is really pleasing,” Grech said.
“We are seeing an increasing momentum in Australia for infrastructure projects to incorporate sustainable materials … I also think there is a need for industry and government to come together to create an environment that promotes the use of recycled content.
“Government has a role to play, to encourage and indeed support Australian companies that innovate in the use of Australian recycled material.”
Waste as a resource
For Professor Veena Sahajwalla HonFIEAust CPEng, tackling the growing waste problem means changing the way we view waste, and aligning the worlds of manufacturing and recycling.
“It’s an innovative way of thinking — how our waste materials can be really useful and really valuable in many instances,” said Sahajwalla, Director of the Sustainable Materials Research and Technology (SMaRT) Centre at the University of New South Wales.
“We need to retain waste material in our economy and not see it as a bad thing … For example, electronic waste (e-waste) contains so many important metals and precious materials. When you dispose of e-waste with plastics and metals, you end up in a smelting situation where the plastics burn, and a lot of the materials aren’t harnessed.”
Sahajwalla, who will present at the World Engineers Symposium next week, is currently focusing on harvesting such materials through micro-recycling.
“Say you want to harness a particular alloy that is rich in tin. If you take an entire circuit board and heat it up, you’ll have an alloy with copper and tin in it,” she said.
“But if you want to harness the tin separately, you can control it at much lower temperatures and produce that metal… Through microfactories, you can then tailor the exact chemistry of the alloy, because you’re operating in that controlled setting. These microfactories give you a lot of flexibility to deliver the right kind of alloy.”
This process, known as selective synthesis, also has the benefit of being a localised recycling solution.
Sahajwalla officially launched the world’s first microfactory in 2018, unveiling a modular system to convert old phones and computers into materials for reuse that could be installed in an area as small as 50 square metres. This meant e-waste recycling facilities could be conveniently transported to the waste site, cutting down on transport and logistical costs.
“If you can set up microfactories locally, you can create local jobs and support local economies,” Sahajwalla said.
“I like to think of microfactories as upcycling and creating value for local economies… Our solutions need to be accessible and affordable to everyone in the world.”
As well as e-waste, the SMaRT Centre’s research focuses on developing solutions for waste tyres, mattresses, fabrics and glass. The Centre also recently collaborated on a project with Hunter’s Hill Council in Sydney’s Lower North Shore, converting old uniforms into tiles fitted to an island bench. Additional collaborations are likely to be on the cards in the future.
“A whole range of businesses and councils are keen to take our collaboration and partnership further,” Sahajwalla said.
“We’re also about to embark on a new Australian Research Council research hub, covering batteries and other consumer waste.”
New government programs
Some state governments are also playing their part. Western Australia, for example, recently launched the WasteSorted e-waste grants program, providing funding of up to $200,000 for businesses to invest in research into and development of innovative processes to recycle and reuse e-waste. Grants of up to $80,000 are also available for organisations looking to increase the volume of e-waste collected for recycling.
Meanwhile in New South Wales, the state government-funded body, NSW Circular, aims to work towards a zero-carbon circular economy by designing out waste and pollution, keeping products and materials in use, and regenerating natural systems.
It’s this shift in our thinking that could pave the way towards a waste free future, with engineers being central to the solution, Sahajwalla said.
“Even if our phones and computers become obsolete in the future, those materials never die, the materials never become obsolete,” she said.
“The fact we can go in and harness different types of metals becomes important. We need to think about how we as engineers bring a circular economy to life.”