Developments in eco-concrete look to make the world’s widely most used material more environmentally sound.
They’re the scourge of sewerage systems around the world, but time is up for the fatbergs and concrete corrosion that costs billions in repairs of sewers and pipelines each year.
Engineers from RMIT University have developed an eco-friendly, zero-cement concrete that all but eliminates corrosion.
The concrete can withstand the corrosive acidic environment found in sewage pipes, while greatly reducing residual lime that leaches out, contributing to fatbergs — congealed masses of grease and non-biodegradable products such as wet wipes, which can grow up to 200 metres long and weigh tonnes.
Project lead Dr Rajeev Roychand said the researchers created a concrete that eliminates free lime, a chemical compound that promotes both corrosion and fatbergs.
“The world’s concrete sewage pipes have suffered durability issues for too long,” he said.
“Until now, there was a large research gap in developing eco-friendly material to protect sewers from corrosion and fatbergs. But we’ve created concrete that’s protective, strong and environmental — the perfect trio.”
The RMIT concrete is more durable than Portland cement, making it perfect for use in major infrastructure projects.
“Though ordinary Portland cement is widely used in the fast-paced construction industry, it poses long term durability issues in some of its applications,” Roychand said.
The cement-free concrete solution uses the by-products of the manufacturing industry to create a composite of nano-silica, fly ash, slag and hydrated lime.
“We found making concrete out of this composite blend — rather than cement — significantly improved longevity,” he added.
A report in the Guardian last year found that after water, concrete was the most widely used substance on the planet. The global building industry pours about 19,000 bathtubs of concrete per second.
The RMIT engineers say that their concrete mix could replace cement and be able to withstand the high acidity of sewage pipes.
“With further development, our zero-cement concrete could be made totally resistant to acid corrosion,” Roychand said.
“Our zero-cement concrete achieves multiple benefits: it’s environmentally friendly, reduces concrete corrosion by 96 per cent and totally eliminates residual lime that is instrumental in the formation of fatbergs.”
Coffee flavoured concrete?
Roychand and his team’s innovation follows other RMIT developments in more sustainable concrete.
Last year, students set out to turn the 156,000 kg of coffee-ground waste produced in Melbourne cafes each month before lockdown into concrete.
Ordinary concrete contains up to 80 per cent sand, the third most used resource on the planet. The group found they could replace up to 10 per cent of this sand with coffee grounds and produced sample coffee bricks.
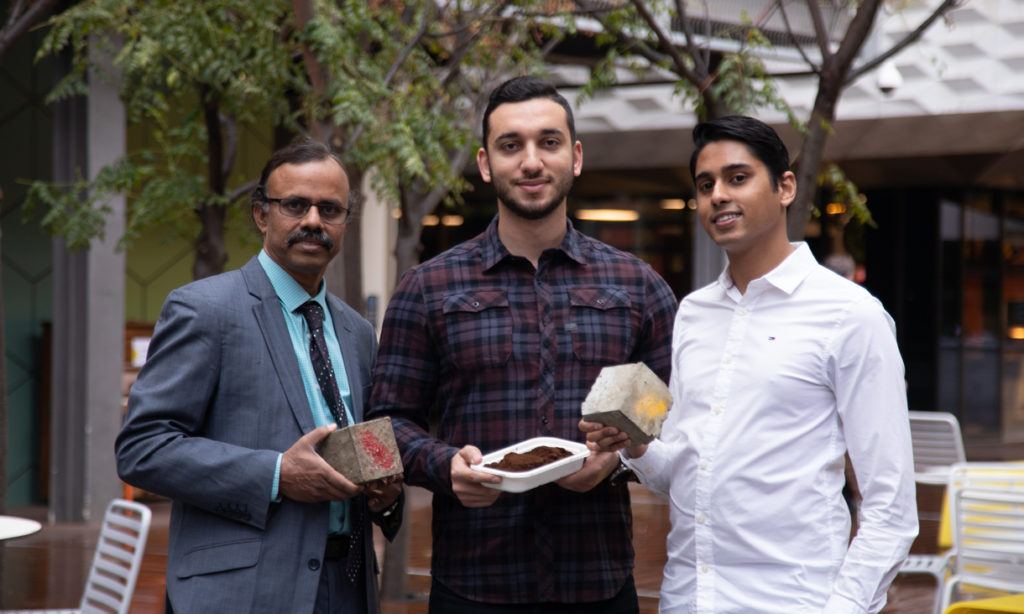
RMIT School of Engineering Senior Lecturer Dr Srikanth Venkatesan said more work was needed before the coffee bricks could become reality.
“The biggest challenge is ensuring the addition of spent coffee grinds does not lead to a reduction in strength of concrete, and this is the focus of further testing and development to make this product viable for use in real-world applications,” he said.
Earlier this year, another research group at the university found that a by-product of steel making could be used to both treat wastewater and make stronger concrete.
Steel slag, which is produced during the separation of molten steel from impurities, is often used as a substitute aggregate material for making concrete. It can also be used to absorb contaminants like phosphate, magnesium, iron, calcium, silica and aluminium in the wastewater treatment process.
The RMIT engineers found that slag that had been used to treat wastewater could then be recycled as an aggregate material for concrete, making it about 17 per cent stronger than concrete made with conventional aggregates, and 8 per cent stronger than raw steel slag.
While there are still technical issues to be overcome, water engineer Dr Biplob Pramanik who oversaw the project said the findings were promising.
“The global steel making industry produces over 130 million tons of steel slag every year. A lot of this by-product already goes into concrete, but we’re missing the opportunity to wring out the full benefits of this material,” he said.
“Making stronger concrete could be as simple as enhancing the steel slag by first using it to treat our wastewater.”
Just add CO2
Other Australian universities are also working on pioneering forms of “green” concrete.
University of Sydney researchers have successfully poured their own blend of eco-concrete, made from a unique mix of fly ash and waste materials including ground glass and gaseous carbon dioxide.
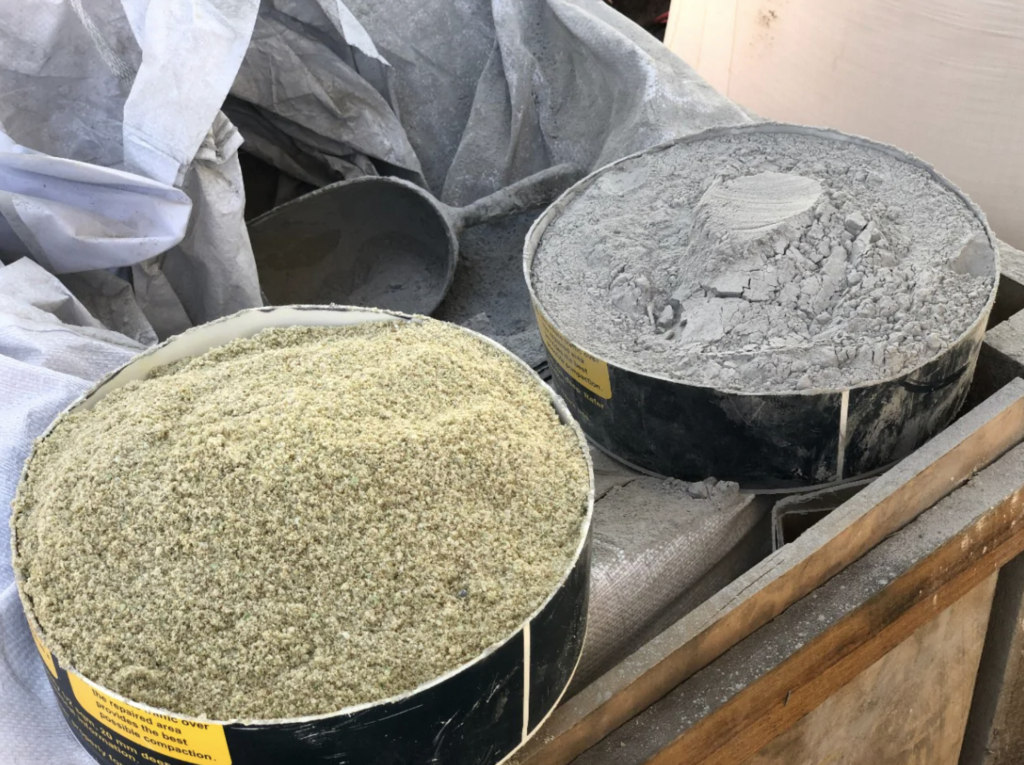
“Traditional concrete production is energy and resource intensive, yet is one of the most common materials used by the construction industry,” said Professor Ali Abbas of Sydney University’s School of Chemical and Biomolecular Engineering.
“We sought to create a less energy intensive solution that would have less impact on the environment using carbon-capture and beneficially reusing materials that would otherwise end up in landfill.”
Australia produces about 12 million tonnes of fly ash per year as a by-product of coal combustion.
The researchers said their ‘eco-pavement’ had saved 752 kg of sand from being dredged and 327 kg of carbon dioxide being emitted into the atmosphere, while its production had saved the equivalent energy of driving a car over 1,800 km.
Their next challenge? Testing an algorithmic intelligence technique that adapts the concrete blend to specific applications before attempting to make their innovation commercial.
This article is very much hype. For one ground blast furnace slag is a cement which has been recognised in German standards dating back to around 1890 and is recognised in European and Australian standards. It is a calcium silicate which hydrates and gets strength on its own. For good early strength it needs activation which comes from the addition of lime or CaO release in Portland cement. One could use NaOH but that has problems with some aggregates plus high cost. Slag (GBFS) has been used in Australia cements since 1975 (I think Swan Cement was the first to introduce it in Australia). By around 1995 GBFS already made up something like 30% of all sold cement in Australia. The special cements Suphate Resistant SR and Low Heat LH have in excess of 55% GBFS. There is no need to replace a properly specified SR cement in sewers. Fly ash has been added in concrete as a cement extender since about 1965. It may assist in improving sulphate resistance of blended cements in some applications.
I personally have specified using a cement made up of 90% GBFS and 10% hydrated lime for cemented mine backfill.
Finally, lime is a cement on its own and was used to make polished concrete floors at Catal Huyuk in Turkey around 7000BC. The first hydraulic cement that gain strength under water was made by Greeks around 600BC using a cement of volcanic ash (rich in fine silica) activated by lime.
It would be great to see a follow up article that responds to the comments made here.
The production of cement involves burning limestone to produce lime and carbon dioxide.
(I.e. Ca CO3 -> Ca0 + CO2). Put simply, the lime is then burnt with fly ash, gypsum and clay to produce cement, which, when added to a water, sand and aggregate mix hardens to form concrete. Different proportions of the mix and additives to the mix change the nature of the final product.
Concrete is absolutely essential and it follows that we can’t do without cement. The problem is the liberation of carbon dioxide.
The developments described in the article are fantastic and commendable, but the carbon dioxide problem looms large.
There are quite a lot of misconceptions in this article as Peter mentioned previously, leading me to feel that this is very much just hype with no scientific backing.
For starters Portland Cement doesn’t have “durability”, because cement is not used in structural applications – concrete is. Cement is only one component of the mix.
Steel slag has also been used in cements but it is not as good as GGBFS, which is iron slag. And claiming that you can achieve a zero-cement concrete by using steel slag is a massive stretch. Even GGBFS is limited to about 70% of total binder content, which is still quite high and seldom used. If you want to claim that a concrete has zero net cement content, please provide the mix designs used.
Finally, I have personally never seen a mix design where sand was used for 80% of the concrete. Generally sand (fine aggregates) and stones (coarse aggregates) are used in a pretty similar proportion, so 80% sand raises an eyebrow. We also need to really see what the environmental impact of using coffee bean waste on the embodied energy of concrete is, since fine aggregate has a very low embodied energy to begin with (~0.006 kgCO2e/kg).
Portland cement was an attempt in the 1800s to try and imitate miracle Roman concrete by adding gypsum to “natural” cement that accelerated setting.
In 1917 the secret for maximum strength Roman cement was found to be activated silicates in volcanic fly ash.
Waste product fly ash from burning coal to produce electricity was used to replace Portland cement in the Hoover Dam spillway as proof cheap waste fly ash (now sold by Boral) made the stronger Roman concrete.