The engineers at the Australian Synchrotron are designing tools to study objects at nano-scale resolution in an impressive display of nanoengineering.
In his 20 years at the Australian Synchrotron, head of engineering Brad Mountford has seen some strange objects.
The instruments he has designed have been used to study an entire living tree, a rhinoceros skull and a fossilised dinosaur nest.
One day, an ancient Egyptian artefact might be in the building; the next, a Renaissance painting or a lunar meteorite.
“One of the beauties of this place is some of the strange things that come through the door,” Mountford said.
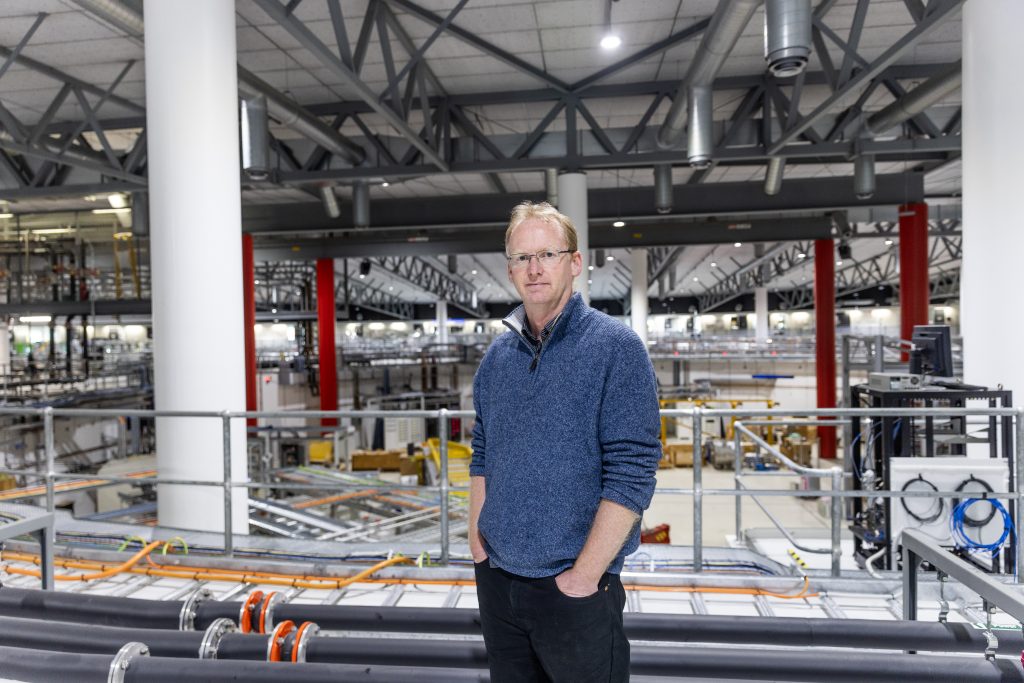
The Australian Synchrotron, in Melbourne’s south-east, is what’s known as a particle accelerator. It’s about the size of a football field and, from the outside, looks like a roofed sporting stadium.
The facility has been called a “super microscope” because of the extremely high-resolution imagery produced by its instruments.
But microscopy is only one aspect of the synchrotron, which is home to a host of tools for examining the molecular and atomic makeup of different materials.
Australian Synchrotron mechanical engineer Becky Lin said the synchrotron produces light, and then uses that light to do scientific research.
“We accelerate electrons really, really fast,” she said. “The light that comes off at a tangent … we use different parts of it to analyse different samples.”
The light is channelled down long pipelines, known as beamlines, into a suite of scientific instruments. It’s used by scientists from universities, other research institutes and industry.
Researchers typically apply for time on the synchrotron, with projects awarded access to the beamlines based on merit. There’s also a small proportion of users — such as for-profit drug companies — who pay to use the instruments.
The facility is one of only two synchrotrons in the Southern Hemisphere; the other is in Brazil.
In designing each beamline, Mountford said the engineering team concentrates on the area where samples go.
“We pay a lot of attention to what’s called the end station, which is where the experiment actually happens,” he said. “And we design them to have an incredible amount of flexibility — within reason — to accommodate all potential scenarios that might be requested of that beamline in the future.
“I would suggest we’ve been pretty successful at that to date. We’ve never had to tear a beamline apart to build it for a particular experiment, but we’ve had some very, very strange experiments happen.”
Breathtaking work
Associate Professor Martin Donnelley is a biomedical engineer researching X-ray imaging and cystic fibrosis at the University of Adelaide.
In August, his team won a Eureka Prize for work that put live rats in the synchrotron’s imaging and medical beamline.
The researchers had to overcome a host of challenges associated with imaging live animals outside of a biological lab. But their efforts paid off with a new technique for imaging the lungs of young children with cystic fibrosis.
Donnelley explained cystic fibrosis is a recessive genetic disease that causes dehydration of the airway surfaces.
“It means that anything that you breathe in sticks to this sticky mucus that’s there,” he said. “Bacteria can grow really well in it — you get these bacterial infections that, over time, destroy lung tissue.”
Donnelley, who works in Respiratory Medicine at Adelaide’s Women’s and Children’s Hospital, said the most common lung function test for kids with cystic fibrosis is called “spirometry”.
It’s a 100-year-old test that sees children blow into a spirometry device to measure “forced expiratory volume” — essentially the amount of air they can get out in one second.
“You have to breathe in as much as you can and then, as quickly as you can, get all the air out of your lungs,” Donnelley said.
“And so kids under five or six years of age can’t do that test.”
The alternative is a CT scan, but doctors don’t like to do too many CT scans on children because they come with a dose of ionising radiation.
Instead, Donnelley and his colleagues were able to use the synchrotron to track the motion of lung tissue throughout the breath cycle.
The new technique is called “X-ray velocimetry”, and it allows doctors to visualise where air is flowing in a lung and better calculate ventilation.
“You can actually generate a coloured map of airflow at different parts of the lung,” Donnelley explained.
Live broadcast
Donnelley and his team spent a long time developing tools and techniques to image live animals at the synchrotron.
“Early on, we faced a lot of challenges in figuring out how to make biological experiments work really well in a physics facility,” he said.
In the lab, for instance, scientists can easily administer a substance to a rat and observe what happens.
But at the synchrotron, where researchers are isolated from the experiment because of the radiation, they had to develop ways to do it remotely.
“Then we have to do a lot of things like physiological monitoring, to make sure that our animals are healthy and okay even though we can’t directly see them in front of us,” Donnelley said. “We need to make sure that they’re kept warm, [have] fluids, and we monitor their ECG and respiration and temperature.”
The team developed novel ways of detecting breathing, using sensors to pick the exact point in the breath they wanted to capture images.
They also became skilled at identifying landmarks within a rat to position the field-of-view — which could be just 1 mm2 — in just the right place.
Donnelley admits there were days the team reflected that they wished they’d taken up imaging geological samples instead.
“It just seemed so much easier sometimes,” he said.
But their work has paid off, and the technology is currently being commercialised through Melbourne company 4DMedical — with whom Donnelley is a shareholder.
On the clinical side, the researchers are now recruiting children with and without cystic fibrosis to gather baseline data on what their lungs look like.
Donnelley is also conducting a paediatric X-ray velocimetry feasibility study with the children’s hospital in Adelaide.
Donnelley said the research is uncovering children who score well on traditional tests but whose lungs are struggling.
“One of these kids has this spirometry value — FEV1 — of 96 per cent,” he said. “So we would say lung function is normal. But when we look at the ventilation map … we can pick areas within the lung where there’s reduced ventilation.”
Donnelley said the human lung is very resilient.
“We saw this during COVID, that people can be really, really sick but the lung still manages to cope [and] keep you alive,” he said.
Lungs can also compensate. If one area of the lung isn’t performing as well as it should, another can increase performance to make up for it. That’s something the researchers can see with the new imaging technique.
“It’s data that we’ve never been able to acquire before and never been able to see,” Donnelley said. “So being able to identify these changes is really exciting.”
He said the technology can also be used for other respiratory diseases, including asthma and chronic obstructive pulmonary disease.
“Hopefully, it’ll become that new technology that, instead of going and getting a CT or a lung function test, you go and get this [X-ray velocimetry] scan.”
Sustainable concrete
Associate Professor Ailar Hajimohammadi is leading research at the UNSW Sydney that could overhaul one of the world’s major carbon dioxide–emitting industries: cement.
She’s developing sustainable concrete that can reduce carbon emissions by up to 80 per cent. Her materials combine geopolymers with industrial glass and sand wastes to produce high-performance green concrete for the Australian construction industry.
Hajimohammadi was awarded time on the Australian Synchrotron to understand the chemical bonding structure of the green concrete.
Using the synchrotron’s infrared microspectroscopy beamline, she was able to study the local chemistry of the material and how the geopolymers interact with the glass.
“[It] helped us to understand some effects of different parameters on the distribution of the geopolymer gels, or the homogeneity of that distribution, or the interface of the binder with the aggregates,” Hajimohammadi said. “They’re things that we cannot really do in the lab.”
Concrete is the most widely used human-made material in existence. The industry is responsible for eight per cent of global emissions — far greater than aviation.
To create green concrete, Hajimohammadi uses industrial by-products and other waste materials that are high in alumina and silica. She then activates them with an alkaline product that helps everything bind together.
Along with their environmental benefits, Hajimohammadi said geopolymer concretes perform well in aggressive environments. She said they are very durable in acidic or salty environments, compared to normal concrete.
“It can have very good high temperature resistance or fire resistance … it has been used as a coating against fire as well,” Hajimohammadi said.
She said geopolymer concrete can also be manipulated and customised to give it different characteristics, such as higher strength or long-term durability.
Hajimohammadi is working on a project with construction company John Holland that will use waste glass to develop geopolymer concrete for paving. She’s also collaborating with Transport for NSW and Jacobs to explore structural applications for the materials.
For Hajimohammadi, who has been studying geopolymer concretes since 2007, broader use of geopolymers concretes can’t come soon enough.
She wants industry, academia and government to work together to speed up adoption of the technology.
“That is what I’d like to see happening quicker,” Hajimohammadi said.
Nanometre precision
Mountford started working at the Australian Synchrotron in 2003, when the facility was little more than a series of concept drawings and artist’s impressions.
A few months earlier, the synchrotron and its first employees had featured on the cover of the Engineers Australia magazine of the day.
Today, Mountford and Lin are working on the design of new beamlines as part of the synchrotron’s Project BRIGHT upgrades.
One is a new nanoprobe beamline that will allow scientists to see fine structures at resolutions as low as 15 nm. That’s about 5000 times smaller than the thickness of a single sheet of paper.
“It’s going to use a nano-focused X-ray beam to focus on almost individual atoms, and get them to fluoresce,” Mountford said. “That fluorescence can tell you a lot about what they are.”
Designing a beamline with such a small focus is a huge challenge.
“You have to consider things like ambient air temperature, air movement, we even have to consider the solar load on the building itself,” Mountford said.
“If you want to go really, really small, your problem space gets really, really big, and you have to start considering things that you wouldn’t have had to normally think about.”
The team tries to eliminate interference where they can, but it’s not always possible.
“You can’t eliminate ground vibration, for example, so you have to spend a lot of time trying to find a way to isolate it or mitigate it,” Mountford said.
“Putting damping in and under a structure to dampen the vibration — there comes a point where that’s no longer effective, and you have to start implementing another solution on top of that. And that’s when you start looking at things like active feedback.”
Lin said working at the synchrotron means finding solutions for engineering problems not faced elsewhere.
“You’re always learning new and complex scientific things,” she said.
Mountford still doesn’t consider himself an expert.
“I always tell the new starters on my teams — don’t try and learn it all at once, because you’ll never learn it. It’s a bottomless pit of both interesting experiments and — from an engineering point-of-view — an interesting set of challenges. It just changes so much.”