Advances in generative design and AI are changing the way NASA creates some of its most complex machines.
While traditional computational design starts with a predefined shape or idea that is then refined and optimised, generative design begins without a concept, and uses the specific objectives and constraints set by the engineer to create a design.
In other words, generative design allows engineers to focus on defining what a design needs to do, and AI can then produce concepts that comply with their requirements.
NASA, a pioneer in the field, calls it their “evolved structures process”, and to date it has demonstrated a reduction in development time and cost of more than ten-fold, while structural performance has been enhanced three-fold.
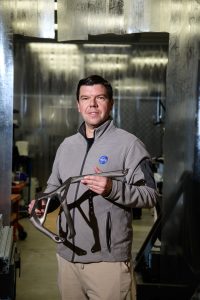
Ryan McClelland, a research engineer at the NASA Goddard Space Flight Center, told create that the “text-to-spaceship” vision is a bold way of thinking about what the agency can develop with AI-powered generative design.
“At Goddard, we start with the science need, such as imaging exoplanets, and then that gets broken down into requirements, such as a certain size of mirror or kind of orbit,” he said. “That is then broken down into the requirements of the systems, such as what is needed from a detector.”
It’s called requirements decomposition, and NASA uses generative AI to help “radically speed up” that process.
“Once you have those requirements – if you have computational design systems like text to structure – then you can almost fully automate making the structures,” McClelland said.
Evolved structures
Generative design finds areas where the material isn’t stressed and it removes them, before creating a surface that encompasses all the higher-strength areas.
“It uses things like gradient descent to figure out what the next step is, but it isn’t generative AI in the same sense that LLMs [large language models] are generative,” he said.
In fact, the inspiration for what NASA calls “evolved structures” came from the engineers noticing that the parts “looked like alien bones”.
McClelland said that people tend to associate generative design with additive manufacturing, but for NASA, this usually isn’t the case.
“For most of our applications, additive is not the way to go. When we’re CNC machining, it is made within plus or minus 75 microns in metric units.
“One of the most surprising things that we found is that because of software advances, CNC milling of parts has a lower cost, lower schedule, better tolerances, higher strength.”
Rocket science
To demonstrate how NASA is using generative design, McClelland showed create a part called the Evolved Optical Bench for an earth science mission currently in development. The original design for the part weighed 3.6 kg, but after it went through the generative design process, it now weighs around 600g.
“It has a lot of interfaces, and the AI combined about 10 parts into a single part, CNC machined from a single block of aluminium,” he said.
NASA is unable to comment on the cost of specific parts.
McClelland added that with so many interfaces facing in different directions, it would be incredibly difficult for a human to come up with such a design.
Describing generative design as being “enabling at a systems level”, he said that one benefit for engineers is that they don’t need to keep track of different parts and figure out how to bolt them together.
“In terms of heat flow, if you have a bolted interface, it tends to be very thermally insulating. Having it just be one solid part of aluminium means that it has a smaller thermal gradient.
“In this case, we use generative design to determine the best place to put our bolts. The software walks through the joints in mechanical structures that are fastened or bonded.”
Next evolution
For most of NASA’s generative design applications, which now number 60, the agency uses Autodesk Fusion 360. McClelland said that NASA is now turning its generative design guide into code through Synera, a low code programming tool.
Helping engineers overcome the common pain point of multiple CAD or computer engineering software with different user interfaces, the program “simplifies the process where text input leads to mechanical design output”, McClelland said.
“One of the nice things about Synera is that it’s the glue that attaches a lot of different Computer Aided Engineering software together and favours things that have APIs that you can tap into.”
While NASA is making “awesome looking parts”, McClelland pointed out that the agency can’t take any chances when it comes to mission success.
“We have to have ways of making sure that people are right through validation, through things such as finite element modelling and vibration testing.
“You have to start from a place of understanding what the requirements are, especially for something that’s more complex. This often looks like ensuring material doesn’t ‘grow’ in an undesired location, or if there are thermal requirements.”
For McClelland, it’s a tremendous opportunity to both accelerate mission development and unlock game-changing performance improvements.
“Generative design has completely changed the way that engineers look at design.”
Videos edited by Joseph Harding.