A new truss bridge over the Nepean River let BG&E push the limits of an unconventional construction technique.
A new footbridge linking Emu Plains and Penrith provides a safer alternative to the neighbouring Victoria Bridge for walkers and cyclists.
Among other things, the recently opened bridge, the Yandhai Nepean Crossing, was a chance for engineering firm BG&E to extend its history of using one alternative bridge building method.
“We were the first to really bring incremental launching to Australia back in the early ‘80s,” Joe Turner, Principal Bridge Engineer at BG&E, told create.
Ernie Evans, the E in the 48-year-old engineering firm, came out of retirement to help Turner build the steel truss bridge — with its main span of 200 metres — on shore, and then launch it across the river in sections to be fastened into its final resting place.
This method reduces the need for temporary in-river structures and provides other cost and time savings.
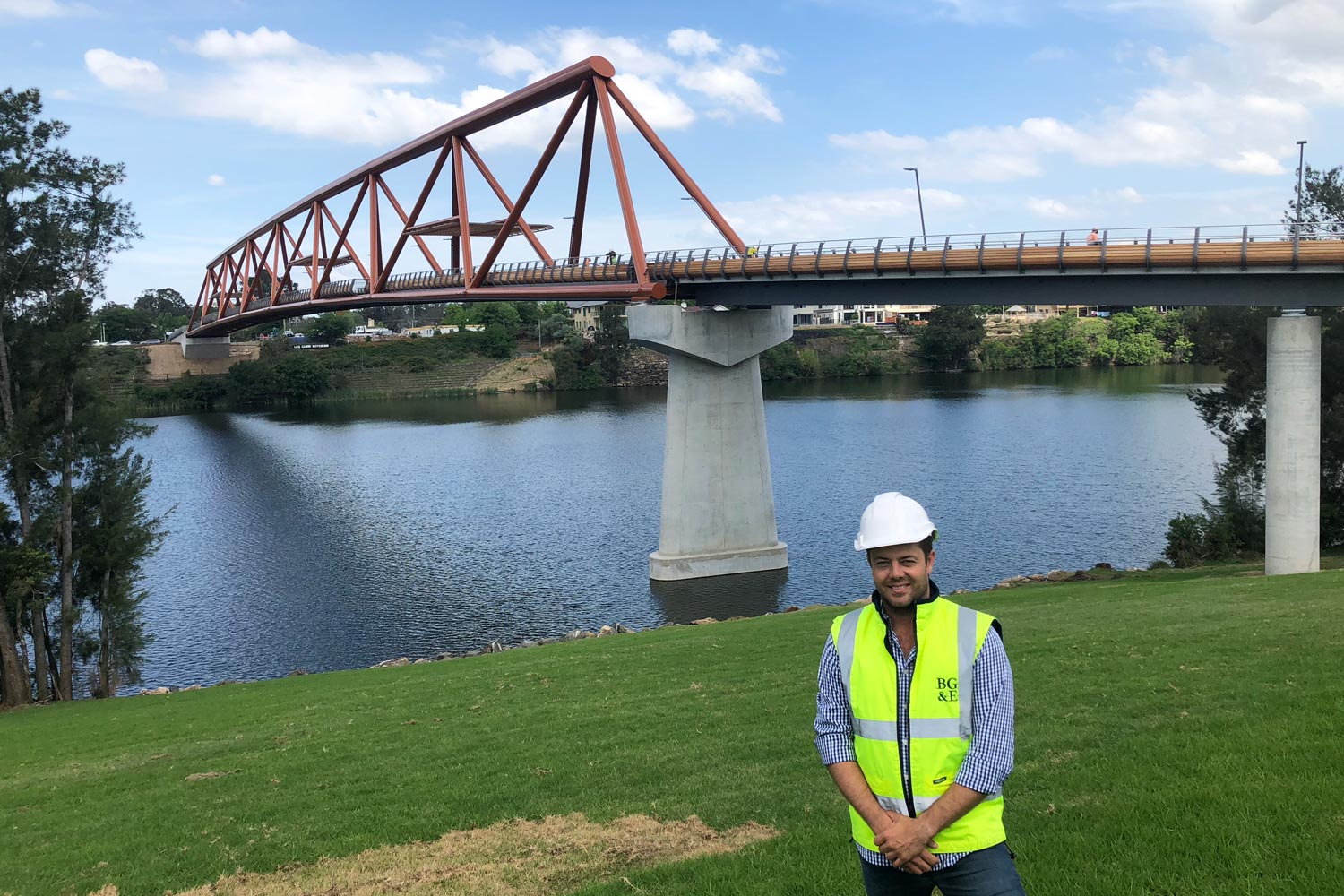
The technique is used by several accomplished engineering firms around Australia, said Turner, but generally for concrete box girders that “are dead straight or on a constant single curvature”.
These are situations for which BG&E has also employed incremental launches.
“Where we liked to innovate and colour outside the line is: how do we push that construction technique further?” he said.
“It means that you get to build the bridge in the one spot safely, not over the water.”
Dreaming it up
The complexity of the Yandhai Nepean Crossing meant that modelling in Revit was carried out “to the nth degree”. Building information modelling has been strong in BG&E’s Sydney office, which handles a lot of building work, and has filtered through to the rest of the company.
The bridge’s bright ochre-coloured structure includes an unusual amount of detail, including tuned mass dampers, complex feature lighting, handrails, balconies and architectural timbers. Capturing this before building has been advantageous.
“Because it’s such an aesthetically different structure, having that 3D model just allows you to visualise better and to make sure all the elements fit together and will be accessible for future inspection and maintenance,” Turner said.
Turner adds that geometry control for the massive steel structure was very complex.
“This bridge is so big that it’s changing and moving all the time in 3D space due to temperature,” he said.
“Adding new truss segments during construction was kind of like pin-the-tail-on-the-moving-donkey, but the donkey’s a 200-metre long, 13-metre tall truss.”
This article originally appeared as “Launch ready” in the April 2019 issue of create magazine.