At a new facility in South East Queensland, innovative textile recovery processes will help reduce landfill pileup by turning worn-out fabric into raw materials.
Australians are the world’s second-largest consumers of new textiles, behind the United States. Many of these goods end up in landfill, with the Australasian Circular Textile Association estimating nearly one million tonnes of leather and textiles are sent to landfill in Australia each year, with the average Australian contributing close to 40 kilograms of waste.
Globally, an estimated 92 million tonnes of textiles are sent to landfill each year.
At a national roundtable on textile waste hosted by Federal Minister for the Environment Sussan Ley in May, fashion industry leaders agreed a circular economy, in which textiles are reused and recycled, was critical to combat the issue.
“We want to keep clothing out of landfill, where it can take hundreds of years to break down, releasing harmful carbon emissions along the way, and we do not want to bombard our charities with clothes that are not fit for reuse,” Ley said.
“Clothing charities can be a great place to thrift shop, but they are not the place to send our tatty, pre-loved clothes that are barely hanging by a thread, and no amount of ‘wishcycling’ will change that.”
But the mixture of different natural and synthetic fibres in blended textiles makes effective recycling difficult.
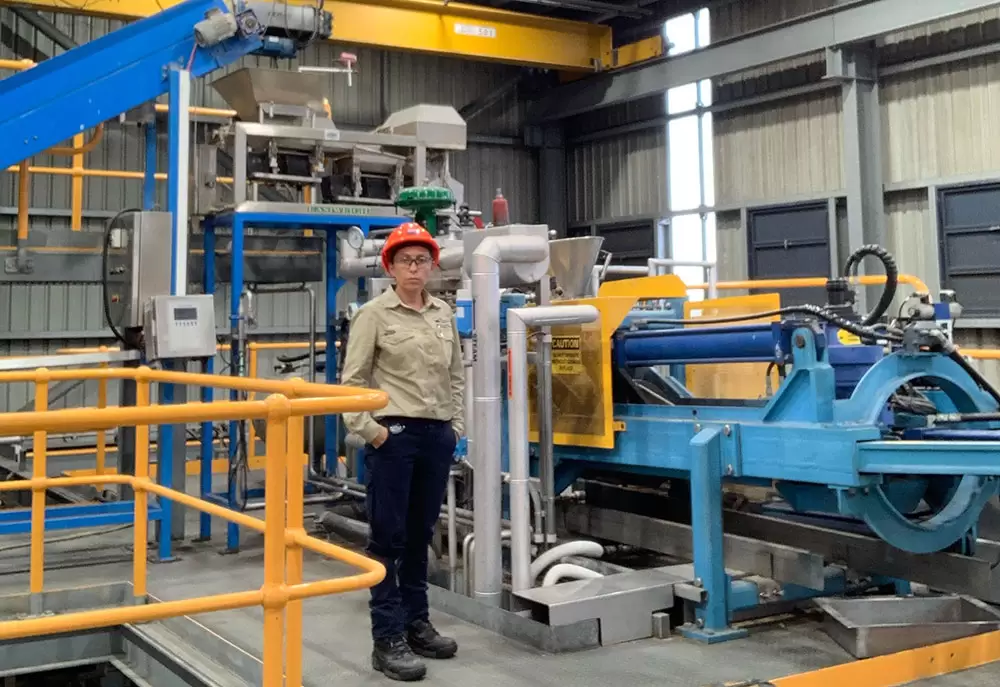
This is something clothing and fashion industry veterans Graham Ross and Adrian Jones set out to change when they founded BlockTexx, with a mission to transform old textiles into a valuable commodity.
In 2018, they began working with researchers at the Queensland University of Technology (QUT) to create a process that could separate the cotton and polyester commonly found in clothing. The result was a chemical separation process called SOFT (separation of fibre technology), which turns cotton to cellulose and polyester to flake for industrial uses such as injection moulding.
The patent-pending technology will be used at BlockTexx’s new facility in Logan City, which is set to commence commercial-scale operation in early 2022, after the startup raised $5.5 million through private investment and government funding to bring its vision to life.
Chemical engineer Karen Cardona was recently appointed BlockTexx General Manager – Engineering and Technology and will oversee the new facility. She is currently setting up the operations and procedures at the plant, including managing trials with suppliers, working with project delivery partners and assisting the executive team with business development.
Getting everything up and running is a “very big job”, Cardona told create, but one she is passionate about.
“The proof of concept for the facility and its operations is coming together nicely, and in our minds it can’t come quickly enough,” she said.
“To make real impacts right now, we need to move with urgency and are preparing all the resources and planning to allow us to have those impacts as quickly as possible.
“As you read this, tonnes of textile waste are being sent to landfill, so the sooner we can get these processes going, the better tomorrow we face.”
Recovering and reusing raw fibres
The Logan facility is expected to recycle 4000 t of textile waste through the SOFT process during its first year of operation, which BlockTexx says will offset about 120,000 t of CO2 equivalents.
“BlockTexx focuses on the component materials in discarded clothing, sheets and towels, which are predominantly made from polyester and cotton. Our process recovers these raw fibres so they can be reused,” Cardona said.
“The repurposing of these fibres ensures they get a second life across a variety of new products, spanning textiles, packaging and building products.”
Cardona, who will commission the build for the facility, said “customised engineering equipment” will be needed to deliver the scale required.
“I can see how it all needs to be structured — from the management of facilities and working with consultant engineers in considering where everything will fit and how all elements will be well resourced, through to developing policies and processes including risk assessment, hazard identification, standardised safety procedures, incident reporting and communication flows,” she said.
Although the company is starting small, the aim is to scale up, with the BlockTexx team envisaging licensing the technology globally.
“We’re in a unique position to make a real impact,” Cardona said.
“This is the first time this industry has seen a commercial-scale solution that creates a true circular economy.”
A no-waste mentality
Cardona grew up in Guatemala, where she says her family was “always appreciative of what we had”.
“We didn’t have a wasteful mentality. If we had chickens, we knew they would feed us and realised the sacrifice. We grew a lot of food, shared food and took pride in composting,” she said.
“We had three generations living close by and shared clothing between the houses. When you grew out of something, it went to another member of the family and many pieces were unisex.”
Today, Cardona has more than 15 years of experience in both chemical and industrial engineering roles across the ethanol, mining and sugar industries. It was during her time in mining that she developed a greater passion for the circular economy.
“The mine I worked for had ceased operations and I remember going up to the peak and looking down over the earth and feeling a sense of devastation,” she said.
“‘What have I done?’, was all I could think.”
From then, Cardona knew she wanted a job where she could use her engineering skills to make a positive difference to the planet.
“I had that vision of the mine in the back of my head and knew that to make impacts over the next 5 to 10 years, I needed to pair with a business that matched my time, energy and passion in bringing things together for measurable change,” she said.
“That’s what I’m doing with BlockTexx now — realising the full potential of proven research and transforming that into commercially viable processes that will reduce textile waste.”