Engineers at RMIT are designing bricks for construction using rejected material from the paper recycling process such as glass, plastic and aluminium.
The CSIRO has stated that circularity in Australia’s economy is only half the global average. For example, despite glass being an infinitely renewable resource, Australians only recycle around 60 per cent of the material, with the rest ending up in landfill.
This problem, combined with the goal to reduce emissions, has motivated a team of RMIT University engineers to research more efficient ways to produce construction materials.
The result is energy-efficient bricks, made with a minimum of 15 per cent waste glass and using 20 per cent combusted solid waste – the ash left over from burning landfill – as a substitute for clay.
More efficient construction
Associate Professor Dilan Robert CPEng said the team started working with recycling company Visy in 2020 to find a solution to the one million t of glass waste and 40 million t of municipal solid waste generated each year – and also realised that traditional manufacturing processes consumed a significant amount of energy.
“One way of approaching this was to see if we could use base materials to come up with an efficient construction product – and at the same time bring us more environmental benefits compared to the commercial bricks in the market,” Robert explained.
“While there are many projects using these base materials, from our understanding this is the first time an energy-efficient brick has been produced that satisfies compliance standards for fired clay bricks.”
Traditionally bricks are made from clay, sand and water – the mining of these resources can result in environmental degradation and land use changes.
Plus, clay is a diminishing resource; Victoria is predicted to have a significant clay deficit by 2050.
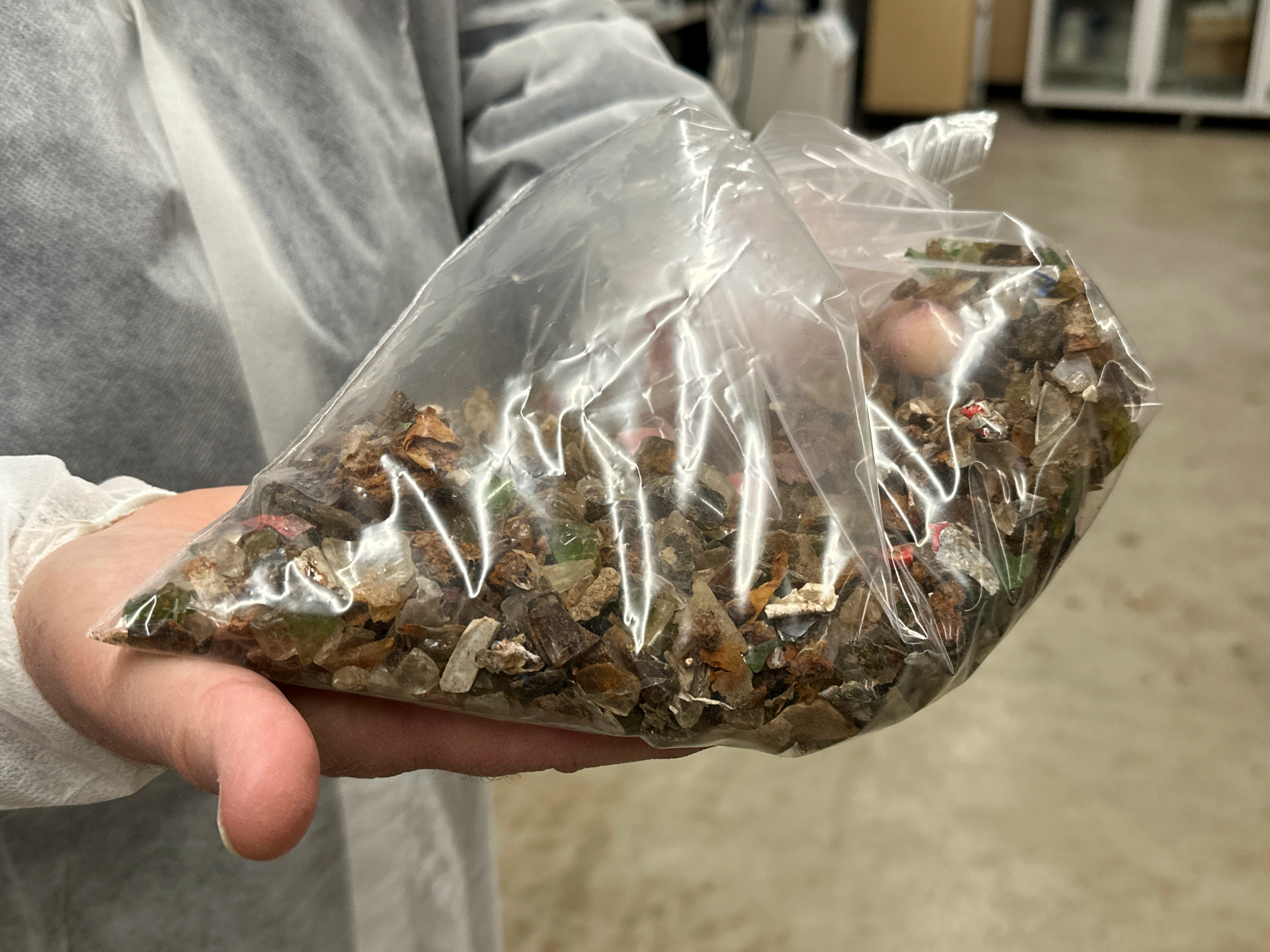
For the smart bricks, the RMIT team experimented using rejected material from the paper recycling process, known as RCF waste, which comprises mostly glass (more than 92 per cent), staples, aluminium, plastic, paper, stone and ceramic. The large majority of RCF waste glass is smaller than 8.9 mm.
X-ray fluorescence analysis showed that RCF waste has a SiO2 percentage of 49.30 per cent and waste glass dust has a slightly higher SiO2 percentage of 52.47 per cent. As the SiO2 in clay soil is 46.92 per cent, the team found RCF waste and waste glass dust were potential candidates for replacing clay.
In all, the team tested bricks using four different compositions of RCF waste and waste glass.
In situ benefits
The brick is not only efficient in the way it helps keep waste out of landfill. Robert said another unique feature of the project was that during manufacturing, calculations show that it can save about 20 per cent energy compared to the conventional manufacturing of the bricks.
“We predict firing temperatures to be less compared to commercial brick manufacturing,” he said. “Based on our inhouse testing, it will require about 10 per cent less [heat].
“For example, 10500C is the typical furnace temperature in brick manufacturing facilities, but we require [a] much lower temperature of about 9500C based on the properties of the brick.”
So far the bricks have only been produced in RMIT lab facilities, however predictions indicate that lower firing temperature can cut tonnes of CO2 compared to traditional manufacturing methods.
“The construction sector in Australia contributes about 18.1 per cent of Australia’s carbon footprint, so decarbonising the construction industry in Australia was another motivation behind this project,” Robert said.
Once the bricks are in situ, the benefits continue. Test results indicate that using these bricks in the construction of a single-storey building could reduce household energy bills by up to five per cent compared to regular bricks, due to improved insulation.
In addition, as the bricks are lighter, there are savings related to transport energy, and they are easier to handle on site.
One of the main challenges of the project was to ensure that the processed industrial waste ash didn’t further harm the environment. This involved testing the ideal conditions for production, the optimum dosages of each base material, and the heavy metal leachates to ensure the bricks complied with EPA regulations.
Powering circularity
The team’s next challenge is to trial the brick as part of the manufacturing process with a commercial manufacturer, and to find a way to work with the large volumes and manufacturing schedules.
Robert said that, now, as word is getting out about their innovation, they have been approached by several large manufacturers interested in trialling the energy-smart bricks to see if they can replicate the product to the same compliance standards as the RMIT prototype.
As adjustments to the formulation can result in colour variations including white, yellow and red, Robert expects there to be strong interest once the technology is adapted to large-scale production. He said about 1.4 trillion bricks are used annually in construction projects globally.
Paul Andrich, Innovation Project Manager at Visy, said the company was thrilled to find a solution for material that cannot be recycled into food and beverage packaging.
“Diverting this waste into bricks with added insulation, rather than landfill, is another way we are powering the circular economy,” he said.
Solving problems for humanity’s benefits are engineers’ bread and butter. The upcoming Climate Smart Engineering Conference 2024 (CSE24) brings together some of the profession’s best thought leaders to navigate the clean energy transition.