How automation, advanced technologies and renewable energy adoption are fuelling the development and uptake of electrified equipment and processes across Australian mine sites.
Mine sites are power-intensive, with energy required across a range of different equipment types and processes throughout the mining value chain.
In many cases, diesel is the predominant fuel source to create baseload power for a mine site, said Clare Larkin-Sykes, mining engineer and Managing Director of Forelight Advisory.
“Depending on where the site is located, it may not have access to grid power,” Larkin-Sykes said. “So often mine sites require the use of diesel as well or other fuels to fulfil the power requirements onsite.”
However, there is currently a “big shift” in the industry towards mine site electrification, with a key driver being to mitigate Scope 1 and Scope 2 emissions.
“A key priority for the industry is the mitigation of diesel use, which can generate between 30-80 per cent of Scope 1 emissions at a mine site,” she said.
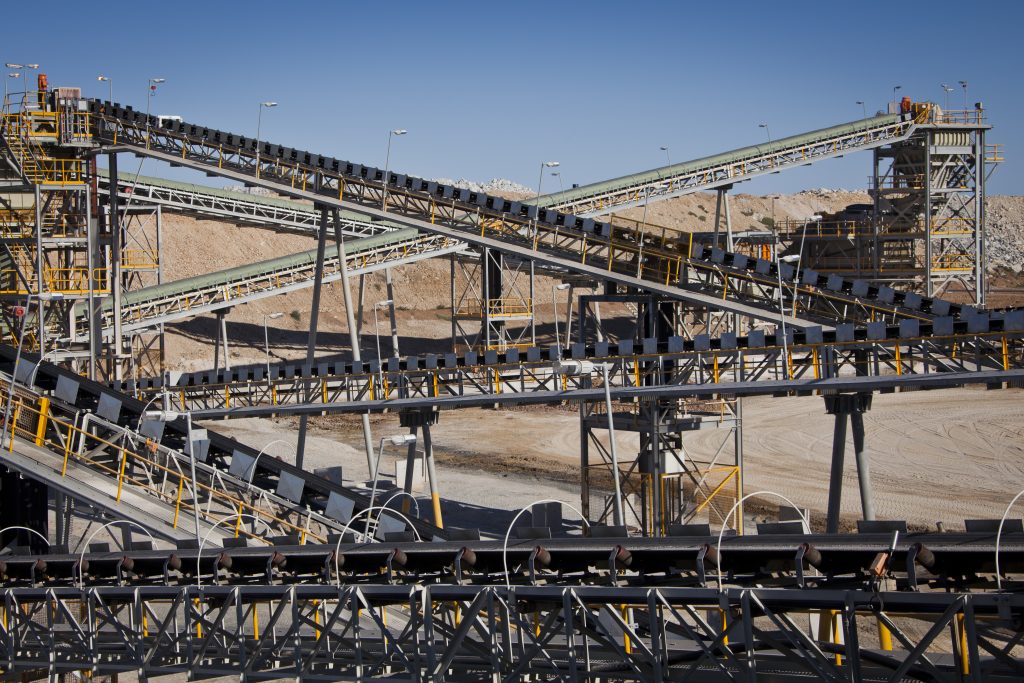
This has led to an evolution of electrification across the whole mining value chain, encompassing a broad range of technologies. Central to the uptake of electrification on mine sites is that the use of electric power is very mature in mining operations.
“For example, a mineral processing system is power-intensive and can’t operate without electric power,” Larkin-Sykes said.
“In many cases the new technologies coming into play seek to adopt renewable energy or remote power systems to create base load power to electrify those types of systems.”
Here’s a look at some of the technologies and processes that are currently undergoing electrification in the pursuit of net zero.
1. Haulage trucks
Haul trucks are used to transport ore or extracted materials from a mining site or the point of extraction to either a waste facility or ongoing mineral processing.
However, a number of things are required to shift haulage systems away from the use of diesel to an electrified system.
“You have to be able to power a large vehicle which is transporting in excess of say 240 t of ore, in a single haulage shift – which could span a couple of kilometres in terms of the drive from the base to a processing facility,” Larkin-Sykes said.
“There must be an ability for steady load as well as the ability to charge batteries effectively… for reliability over the course of a shift.”
A range of technologies are being introduced to meet those challenges, including large tier-one mining companies including Rio Tinto, BHP and Newmont partnering with original equipment manufacturers to address full-scale electrification across a range of different equipment types.
For example, BHP and Rio Tinto have collaborated on electrified haul truck trials in the Pilbara to fulfil a shared goal of reaching net zero operational greenhouse gas emissions by 2050, which entails a pilot of two two CAT 793 haul trucks later this year and two Komatsu 930 haul trucks in 2026 across mine sites in the region.
2. Charging and storage systems
To facilitate the use of electric vehicles such as haul trucks onsite, a number of specialised solutions are being developed.
“For instance, solutions that can quickly change out a battery on a haul truck, or rapidly create a fast charging system for a truck or vehicle on site,” Larkin-Sykes said.
Australian companies such as 3ME Technology and Ampcontrol are pioneering the development of bespoke solutions for the mining industry.
For example Ampcontrol’s MegaWatt Charger – a versatile dual-mode device – can deliver charging power of up to 1 MW. Featuring a hybrid power electronic stack, it can charge multiple vehicles via a single unit.
A whole-of-process view is also beginning to emerge, considering how mining will operate with these new technologies in place, factoring in a shift to greater automation.
“There has been implementation of technologies such as Epiroc and ABB’s augmented trolley systems, where an electric network is installed along a haul road and the haul truck latches on to it and will be powered up a haul road,” Larkin-Sykes said.
3. Renewable energy adoption
With remote mine sites heavily relying on diesel generators to power electrified equipment, there is a range of activity happening in renewable energy adoption in these areas.
“Many mining companies are choosing to either implement renewable energy technology as an asset, or take out power purchase agreements with an energy provider to create solar farms on site as well as battery storage systems to create and store power on site,” Larkin-Sykes said.
For example, in 2022, Rio Tinto announced it would build two 100 MW solar plants and install 200 megawatt-hours of battery storage in the Pilbara region by 2026.
Meanwhile, BHP activated a 38.1 MW off-grid solar system with a 10.1 MW battery to power its Nickel West operations. At WA’s GoldFields’ Agnew gold mine, EDL Energy built a 46 MW hybrid microgrid combining solar, wind, battery storage, and gas power.
“We’re also seeing hybrid systems, where there are renewable energy and battery storage systems onsite alongside diesel generators – which is a lower-emissions option to a full diesel-generated system,” Larkin-Sykes added.
4. Advanced technologies
Many advanced technologies used at mine sites, such as drilling and exploration systems, have benefitted from electrification.
There are also opportunities to electrify remote operating systems, including mapping systems, satellite technology, unmanned aerial vehicles and remote operating centres, Larkin-Sykes said.
“Automation brings about a whole new opportunity for electrified solutions on a mine site … which could ultimately replace the use of diesel at remote operating sites.”
Take mapping technologies as an example. The advent of advanced technologies, data integration, data management, data modelling, analytics and digital twinning are creating opportunities for such applications to bring real-time advanced knowledge and be better able to discover new ore bodies.
To facilitate the discovery and extraction of new mineral deposits, the University of South Australia, in collaboration with MinEx CRC, is developing virtual and augmented reality platforms to create digital redesigns of mining operations that mimic processes such as drilling.
“Broader electrification is creating more advances in computer processing, and is creating the ability to transform mine sites to adopt advanced technologies.”
5. Integration of electrified systems
As yet, no one solution provider nor mining producer is providing an integrated solution to connect electrified equipment or processes across the whole mining value chain.
However, work is being done to find effective models for solution development, requiring strategic collaboration across the industry that has not been seen before.
“Tier-one mining companies are coming together to tackle solutions in partnership, and as a consortium with solution providers, to provide a range of different programs to tackle electrification and emissions reduction at mine sites,” Larkin-Sykes said.
For example, ABB and mining services group Perenti are working on a project to achieve full underground electrification of mine operator IGO’s Cosmos Nickel Project in Western Australia. The whole-of-system project incorporates aspects such as design optimisation for electric operations, fleet selection, power distribution and infrastructure design, electrification system and battery management, and cost modelling.
“These models of strategic collaboration are creating a big shift in the industry – accelerating the application of technologies, trialling, testing, failing – and bringing broader, holistic programs to accelerate electrification in mining.”
6. End-of life transformation
Alongside the implementation of renewable or hybrid energy solutions to power operating mines, there have also been considerations about rehabilitation towards the end of the mining cycle or closure phase of a project.
“A site with a large hole in the ground at significant depth could also create an environment for solutions such as pumped hydro,” Larkin-Sykes suggested.
Solar farms can also be developed on decommissioned tailings dams or other areas which are traditionally seen as unable to be reused or mine waste sites.
“There is an interesting appetite for looking at non-traditional methods of post-mining land use, and what could be possible for a mining operation that is facing closure,” she added.