Completing the city portion of the project involved the technically demanding task of building the tunnel beneath Sydney Harbour.
This article was originally published in the February 2025 issue of create with the headline “Crossing the harbour”.
On 19 August 2024, the latest city-shaping section of the Sydney Metro opened and the list of awards so far is almost as long as the line itself: the National Infrastructure Award for Operator & Service Provider Excellence, NSW Sustainability Award, the NSW Premier’s Award for Building Infrastructure, among a host of other notable mentions.
The Sydney Metro is Australia’s biggest public transport project, delivering a network of four metro lines, 46 stations and 113 km of new metro rail at an estimated cost of $21 billion.
Under the harbour
The new section extends the railway from Tallawong in the city’s north west beyond Chatswood, below the harbour and under the Sydney CBD to Sydenham.
Completing the city portion of the City & Southwest project involved the technically demanding task of building the tunnel under Sydney Harbour.
“This had never been done before, and there were significant associated risks because of the ground conditions under the harbour and the tunnelling technology that needed to be used,” said Hugh Lawson, who was Project Director of Sydney Metro City & Southwest.
“The under-harbour tunnel is a critical part of the project that enables the metro to move people quickly between the city’s north and the Sydney CBD, with a metro trip from Victoria Cross Station in North Sydney, underneath the harbour, to Barangaroo a three-minute journey. It’s part of what makes the metro connect the city in a way that’s never been done before,” said Lawson who recently moved to the role of Head of Customer, Operations & Outcomes at Sydney Metro.
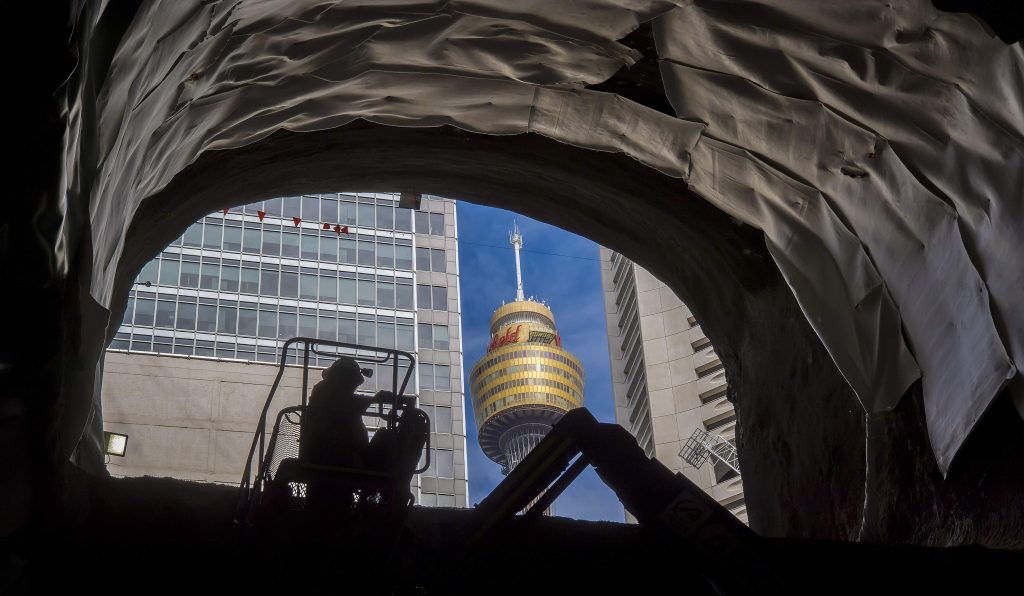
Local conditions
Work on the project started years before a shovel hit the ground when divers conducted geotechnical investigations deep under the harbour.
“By the time I came on to the project, top-class geotechnical surveys and analysis had been done to really understand the geology of the channel through Sydney Harbour,” said Lawson. “Coming from the UK, I was perhaps a bit more familiar with soft-ground tunnelling techniques, but clearly appreciated that it was not necessarily the norm here.”
The erosion channel under the harbour is filled with soft sediments, plant material, silts, peats and clays.
“It would be like tunnelling through material with yoghurt or jelly-type consistency, rather than the hard sandstone that we’re more used to,” said Lawson. Clearly, a different type of tunnel boring machine (TBM) technology was required.
The project team employed a mixed shield (slurry) TBM, specifically designed for the project to excavate in the highly pressurised conditions under Sydney Harbour. Clogging of the cutting wheel in the first section reduced the advance rate somewhat. But Sydney Metro, alongside tunnelling and excavation contractor John Holland CPB Ghella Joint Venture, and German TBM manufacturer Herrenknecht, reacted quickly to the prevailing conditions by adapting the cutting wheel design and flushing process.
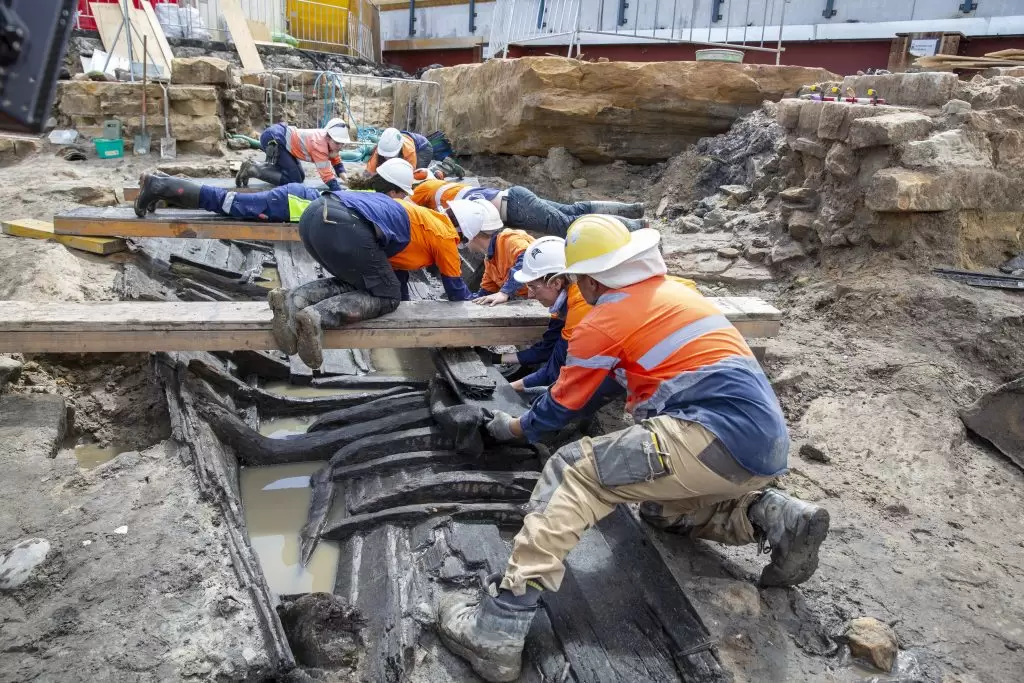
Under pressure
The TBM needed to travel 40 m below sea level and was designed to manage the high water pressures under the harbour, including allowing for the precise control of the support pressure with an automatically controlled air cushion. Two independent pressurised chambers known as “human locks”, each with two airlock doors, were installed for safe access to the pressurised cutting head of the TBM to enable inspections and cutting tool changes.
Before the construction team could use the specially designed 975-t mixed-shield TBM, the 50-strong crew had to undergo training, under medical supervision, in a hyperbaric chamber that simulated the conditions. This type of TBM was also used in the European Alps to build the longest railway tunnel in the world.
There were some tense moments during the tunnelling, especially when bubbles started appearing on the surface of Sydney Harbour – directly above the TBM which was stopped deep below water.
“When that kind of call comes in, you worry about what it might be, and the worst scenario is water coming into the tunnel,” Lawson said.
“In this case, it was just the opposite. We’d created a high-pressure air bubble in front of the TBM that was keeping the water out as it progressed. The air bubble was at such a high pressure, it had found a route out through the soft sediments. Once we established that, the team was able to, within a few hours, stop the air leak and be confident we could proceed safely.”
Read more: How does Sydney Metro manage cybersecurity?
Obstacle course
Tunnelling under the Sydney CBD was particularly challenging as the construction had to happen without shutting down the city.
“We did a lot of work at the design stage to determine the tunnel alignment and exactly how deep we needed to go,” Lawson said.
The team worked out what loads might transfer from the bottom of building foundations or piles onto the tunnel, whether that would be vertical or lateral load, and made sure the tunnel was strong enough to take those loads.
“We also had to ensure the tunnelling wasn’t going to cause settlement or damage to buildings or infrastructure. As well as heritage buildings, many utilities and pieces of infrastructure are hidden underground. In addition to the Tank Stream, underground water courses, sewers, gas pipes and data cables, there are high-voltage power cable tunnels critical to grid resilience and major infrastructure like the Cross City Tunnel.”
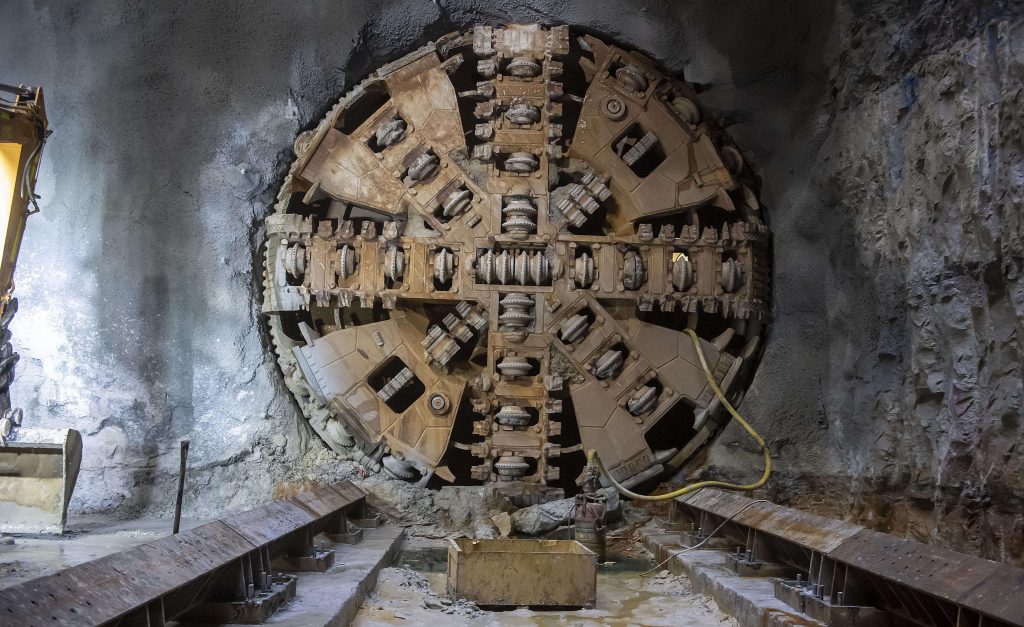
The TBMs had to traverse this obstacle course, and Lawson credits these behemoths with a large part of the project’s success. “When you see the photos of the breakthroughs of the TBMs, some of them have travelled multiple kilometres underground and they enter the station within millimetres of the planned alignment. And the ability to know the precise location of the TBM, to control its alignment with such accuracy, is one of the keys that enabled us to weave in and out of these different bits of infrastructure and be confident that we can undertake this work safely.”
Sydney’s geology also posed a challenge, as the city sits on sandstone and tunnelling through this type of sedimentary rock releases silica and quartz dust that can pose a health risk. TBM manufacturer Herrenknecht modified the air filter systems by placing them as close as possible to any source of dust, for maximum effect.
Above ground, the project was pushing boundaries. To lift the massive TBMs, the team deployed the Favelle Favco 2480D – the largest-capacity luffing tower crane in the world. With a standard lift capacity of 330 t, the tower crane was able to lift 100 t to a 45 m radius with around 130 m of hook height and no support ties.
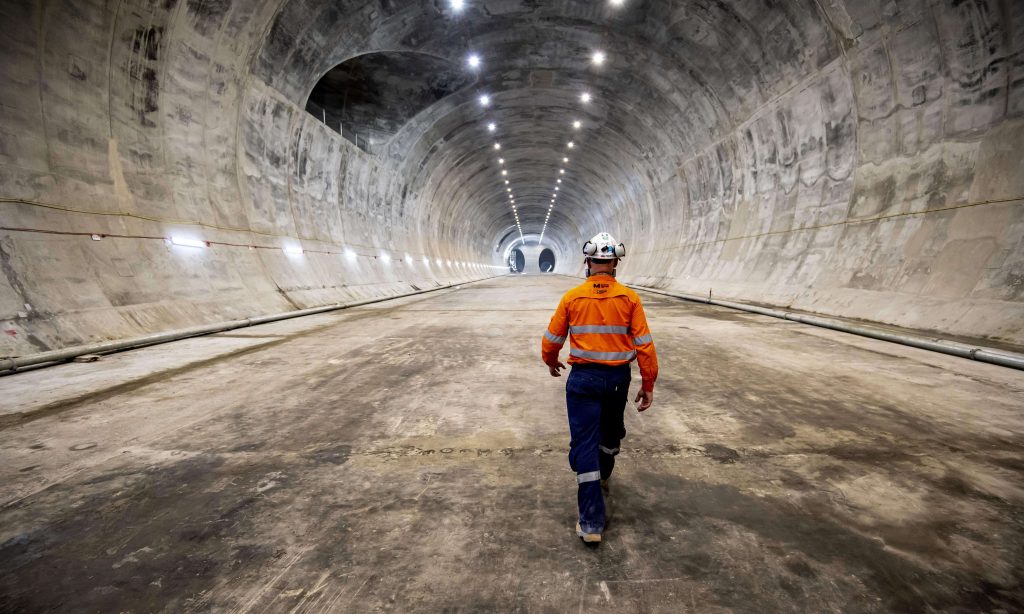
In the cavern
Another first for Sydney Metro was building Victoria Cross, which is Australia’s largest underground railway cavern.
“I remember going down during the tunnelling phase at a unique point in time where we had two TBMs in the cavern at Victoria Cross,” Lawson said. “Coming down the temporary access ramp, I came into a huge single open space with two TBMs having a quick stop for some maintenance. I remember standing with one of my colleagues and looking down, and it gave me a sense of the scale of the TBMs and the technology we use to build these tunnels. TBMs are huge, complex, mobile factories, just incredible pieces of technology that allow us to tunnel quickly and safely, and create the railway we’ve got now.”
The Victoria Cross cavern is 300 m long, 25 m wide and 16 m high, although what customers see now is much smaller than what was excavated because they don’t see all the back-of-house areas. The north end of the station is built 50 m deep. The station has 14 lifts and 19 escalators.
Transforming 117-year-old Central Station was particularly challenging. Work above and below the ground had to be carried out with minimal disruption to the country’s busiest rail station. Despite the challenges, the construction did not cause any train delays over the six years of the project.
Read more: Redesigning a heritage Sydney landmark
Delivering a mega project at this scale called for system engineering closely integrated with the logistical construction delivery.
“We had to build everything at the right time, and the configuration of the railway had to come together at key points to enable us to progress from construction to energisation of the high-voltage system, and then to dynamic testing with trains, to progressively handing over the assets to the operator,” Lawson said. “Sydney is now more connected and has a city metro system that is up there among the best railways in the world.”
A fascinating insight into some of the complexities of tunnelling under Sydney harbour. Thank you.
How did the financials fare? On budget, on time?
A similar article on the Snowy Hydro Mk2 tunnels would be great.