The major automotive manufacturers may have left the country, but this new ute still speaks with a distinctly Australian accent, thanks to the Australian designers and engineers who lead the company’s global T6 platform development.
When Ford Engineer Pritika Maharaj and her colleagues whisked the covers off the 2022 Next-Generation Ford Ranger ahead of the first media drives in early July, it was the culmination of a five-year journey for the team involved in the design and development.
But it was also merely the end of the beginning, since the Australian launch of the Ranger, one of Ford’s most important global models, precedes its roll out to more than 180 markets worldwide, to be closely followed by the related Raptor pickup and Everest SUV.
As the program manager for the Ranger and its stablemates, Maharaj and her colleagues have lived, breathed and sweated the details of the Australian-developed third generation T6 body-on-frame global architecture, upon which the Ranger, Raptor and Everest are based.
Maharaj tells create that she started with Ford Australia as a graduate engineer. During her extensive career at the company, she has worked in practically every area of vehicle development, including test engineering, engine design, powertrain warranty, vehicle interior, cost engineering, and product development quality engineering with the Ranger and Raptor manufacturing plant in Thailand.
Engineering the platform from start to finish
Maharaj returned to Australia in 2021 to take up her current role as T6 program manager, which entails being across every aspect of the Ranger, Raptor and Everest development.
“As program manager, I span the entire T6 platform. My job is to make sure we deliver the program on time, with quality, to the budget, and it’s really all the different elements that come into that,” says Maharaj.
“As we go through the program it involves different things at different stages. Right now, it’s all about making sure that we meet all the deliverables for the launch. But before that there’s a lot of changes we need to make along the way, plus of course the base engineering at the start of a program.
“When you get to the back end of the program, like we’re at now, there are still changes needed, but it’s critical to work out which ones we must do and which ones we don’t, because stability is the key at launch.”
Maharaj says a lot of her time is spent working with teams looking at the changes they want to make, acting on things they’ve learned about the process and supporting manufacturing plants.
“The rest is around making sure all the elements are delivered, which can be anything from an owner’s manual to spare parts,” she says.
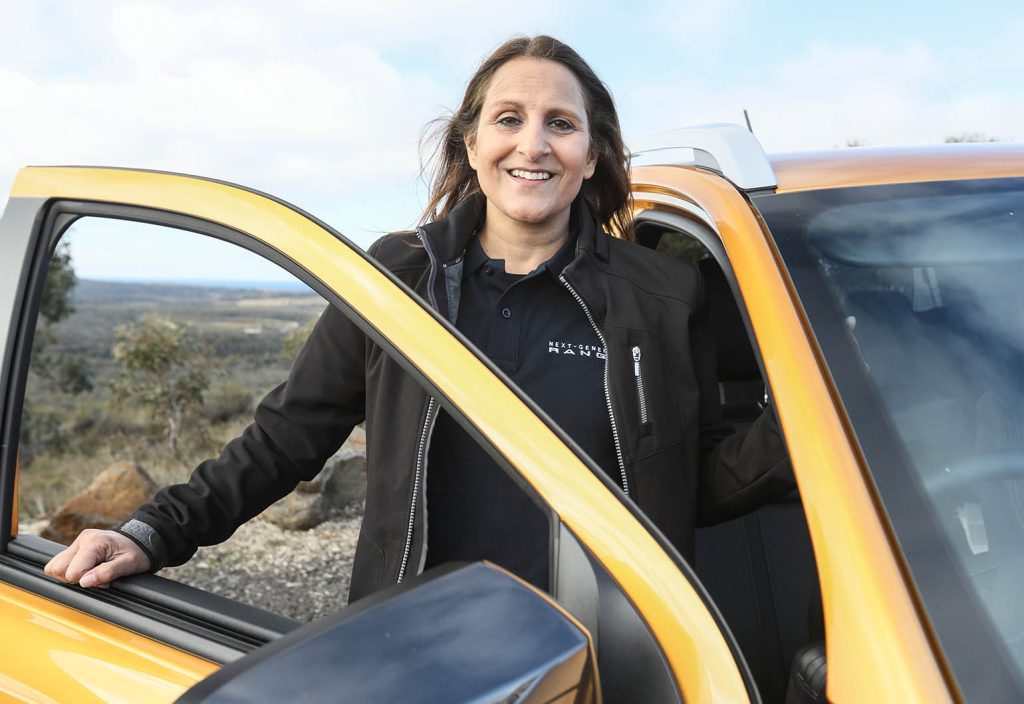
“All these elements come under my remit and my responsibility is to make sure we close them off robustly and that we’re ready to go when it hits the road.”
One of the many big challenges for Maharaj and her colleagues has been the sheer breadth of the Ranger model portfolio, with the Australian model range comprising three engines, two transmissions, three body styles, in two and four-wheel drive variants.
Ford says its aim is to have a Ranger for practically every use-case, hence a 22-model range that starts with the construction-site-ready two-wheel drive single cab XL and culminates with the top-of-the-range Ranger Wildtrak dual cab 4×4.
Diversification of engineering skills
Among many changes Maharaj has experienced during her time at Ford Australia, one of the most significant has been the transition from a largely domestically focused operation to a design and engineering centre of excellence for global products.
This has necessitated a change in the diversity of engineering disciplines required.
“We have such a diverse range of skills in Ford Australia today,” she says. “When I first started, mechanical engineers were the main part of our engineering team from a product development perspective, with a few electrical engineers thrown in for good measure. The manufacturing guys had their robotics and their manufacturing engineering, but there was only a small group that really covered the wiring, the electronics, all of that.
“Now, that side of the business is huge, so it’s a much more diverse range of engineering skills that we have, and that you need to have for the vehicles that we build today.”
These include, she says, mechanical, mechatronics, electrical and electronics engineers.
“A chassis engineer used to just be able to do the greasy bits. Now, a chassis engineer also must be able to talk to the modules that then talk to the rest of the car,” Maharaj says.
“And that’s true for any of the systems, powertrain, chassis. All the traditional ‘greasy’ parts of the vehicle now have to be able to talk and work together.”
One of the other ongoing changes is the industry’s attempts to lower or eliminate tailpipe carbon emissions, which, in the case of the T6 platform, means it has been “protected” or future-proofed for electrification.
“We’ve future proofed the Ranger for new technologies, and I think we’ve even gone so far as saying that we’ve protected the Ranger for electrification. That’s really all about the platform. The platform is our basis for what we can and can’t do,” Maharaj says.
“When we talk about future proofing, we’re saying that the platform has been designed and developed in a way that we can migrate when, and if, we need to other technologies and electrification.”
Maharaj says the engineering team has developed in tandem with the technology and the size of the department handling electrical and electrification has expanded significantly.
“I think it’s just evolutionary,” she says. “As the technology and as the vehicles moved into more of that space, with all the different modules, connectivity and so forth, our team has had to develop as well.”
Australian engineers working at a global scale
Maharaj believes Australia’s multicultural society is something of a superpower that sees us well placed to work on global, collaborative projects such as T6.
“There’s more than just technical skill involved in being a good engineer. There are certain other elements, like communications, that are also important. When I first started at Ford, we worked pretty independently in Australia and were able to do our own thing. Now, we’re a much more connected company globally. Our supply base is very diverse and we’re working with a huge diversity of cultures, languages, geographical locations,” she says.
“I think that fits well for Australia because we’re used to the multicultural aspects, and that gives us an advantage when we’re working with different markets like India, Thailand, the Philippines, and Malaysia, as well as European countries like Germany.
“You’ve got to have strong communication skills. You’ve got to have a bit of empathy and understanding for different cultures to be able to work successfully with them. And I genuinely believe the Australian team is very well positioned to be able to work in this kind of environment.”
With the Ranger sold in more than 180 markets worldwide and manufactured at plants in Thailand, Vietnam, South Africa, North and South America, Maharaj and her colleagues have become adept at working with engineering and product teams around the world.
Another particular strength of the Ford Australia engineering team is the fact they have such diverse and often practical backgrounds, says Maharaj.
“Many of our engineers have come from practical backgrounds including auto-mechanics, racing and farming. These experiences and interests make for a very resourceful and adaptable engineering team.”
The future for Ford in Australia
Maharaj declines to discuss Ford’s long-term engineering future in Australia but does confirm small groups are working on mid-term engineering programs.
“The things I can say are that we are continuing to invest in our engineering facilities. The design studio recently had a massive upgrade, so that’s really expanded both in terms of technology and footprint. And from an engineering perspective, we’re continuing to develop our facilities at the Proving Ground, which is our main technical development hub now,” she says.
“We’re also continuing to invest in our graduate program. We’ve got grads coming through all the time, including as part of my team, where I have a balance of very experienced engineers, but also some of our newer engineers that have only been with the company a couple of years.
“While we are continuing to see all this activity, that gives us confidence in general. So, there’s no promises, there’s no assuredness, but certainly, I’m not sitting here feeling nervous about what the future holds.”
For more of the latest engineering news sign up to create’s weekly newsletter.
Utility is more important than cheezy software & hardware loaded into these trucks … Obviously, ford engineers forgot the ranger was supposed to be a work truck.