A team of Australian scientists has become the first in the world to develop a carbon fibre-based composite material that incorporates sensors, energy storage and radiation protection.
The pioneering work at Melbourne’s Swinburne University of Technology is being led by Dr Nisa Salim, a Senior Lecturer at the School of Engineering, and has significant implications for multiple industries, including aviation, electric vehicles and space exploration.
Composite materials have existed for decades, but demand has surged in recent years as costs declined and manufacturers sought more sustainable solutions for a range of products made from aluminium or other metals.
The fuselage, wings and tail of Boeing 787 Dreamliners contain more than 30,000 kg of carbon fibre-reinforced plastic (CFRP) composites manufactured using 23 t of carbon fibre.
Switching from aluminium led to a 20 per cent weight reduction while the superior frame strength means the model boasts the largest windows of any passenger aircraft.
Meanwhile, an Airbus A350’s CFRP frame means it burns a quarter less fuel than its competitors.
The material is also used in canoes, tennis racquets, surfboards, safety helmets and bicycles.
“Fibre-reinforced composites provide lightweight but strong mechanical properties,” Salim told create. “We’ve found ways to use specialist coatings and functionalisation methods that further increase efficiencies and incorporate new functional features into the structures.”
Inbuilt sensors
Among those functionalities are sensors that automatically send alerts when they detect cracks or when the material is under strain.
It’s set to be particularly useful for the operation of wind turbines.
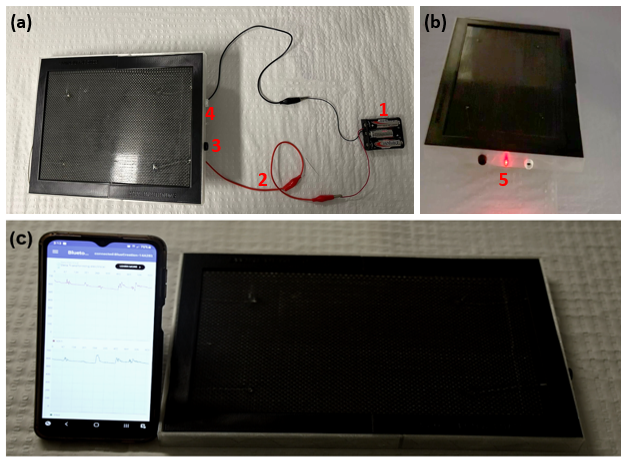
“The blades are typically 45 m long and advances in carbon fibre technologies mean they’re likely to get even bigger,” Salim said. “Currently, the most common method to find out if a wind turbine blade has suffered cracking is a visual inspection, but most turbines are in remote areas or at sea so inspecting them is costly. And even then, a small crack may go unnoticed.
“Our composites sense changes in the health of the material, so the fabric itself acts as a real-time monitor without the need for a separate device that would add weight.”
Invisible batteries
What Salim terms an “invisible battery” that could revolutionise the design of aircraft, boats and electric vehicles.
Traditional lithium batteries can account for a quarter of the total weight of an EV and half that of a drone. Devising ways to reduce their mass is critical to boosting battery efficiency and range.
“As carbon fibre naturally conducts electricity, composite manufacturing can integrate energy storage in the form of the invisible battery, converting the fabric into electrodes and supercapacitors,” she said.
“The idea is to utilise the existing components of a car, boat or rocket and provide them with in-built energy storage capabilities rather than having a separate battery.”
In an aircraft, incorporating energy storage into the carbon fibre on the wings could reduce the total mass by 17 per cent. Salim and her team are in the process of integrating these functionalities into an unmanned aerial vehicle wing to demonstrate the innovation.
Salim has published more than 95 high-impact journal papers and five edited books with a few book chapters on the subject as well as winning a slew of prestigious awards including the Royal Society of Victoria’s Philip Law Post-Doctoral Award (2020), Australian Institute of Nuclear Science and Engineering (AINSE) Gold Medal for Outstanding PhD, a Fellowship from Australian Academy of Sciences and the International Hydrogen Research Collaboration Fellowship.
“We’re the first team in the world to incorporate sensors, energy storage and radiation protection into composite materials,” Salim said. “Now we’re working on commercial applications with several industry partners including wind turbine producers, coating manufacturers and corporate research centres.”