The world’s oceans are estimated to contain more than 170 trillion pieces of plastic. Enter Uluu, an Australian company aiming to change that fact.
In Watermans Bay, a quiet Perth suburb best known for its million-dollar houses and ocean views, something is brewing. A team of scientists, engineers and entrepreneurs has assembled a beachside laboratory with a walk-in freezer of seaweed from around the world.
There are cultures of sensitive saltwater microbes, and a basement full of pressure vessels tended by the team’s resident “seaweed cooker”.
The team is trying to develop an alternative to plastic that’s good for the world.
In charge of the laboratory is Uluu co-founder and co-chief executive Dr Julia Reisser. She started Uluu to produce new materials from farmed seaweed.
“We’re still missing a truly compelling alternative [to] fossil plastic,” Reisser told create. “And the reason for that is twofold. One is on the feedstock [raw material] side … we currently [produce] more than 400 million tonnes of plastic a year.
“Then on the material side, we can’t live without plastic as a modern society.”
Uluu uses seaweed to produce polyhydroxyalkanoates, or PHAs, a material with the potential to replace many if not all plastics.
“PHAs is a natural material, just like cotton and silk and paper, that nature knows and can get rid of,” Reisser said. “But it has this superpower of mimicking those properties that we love about plastic and that we need. It’s lightweight, durable, it melts and re-melts, it has good oxygen and moisture barriers … with the big difference of being biocompatible and truly biodegradable.”
Reisser points to timber as an example of a material that’s strong and durable, yet biodegradable.
“A wooden table is not going to last forever like a plastic one will,” she said. “But because it’s so thick and used in an environment where the moisture is low [and] there [are] not so many microorganisms, it can last a long time. If you dump a whole table in the ocean, it’s going to take months to degrade. But it will eventually — and it’s the same with PHAs.”
Reisser, a marine scientist, began studying plastic pollution after discovering turtles eating plastic in her native Brazil.
She was one of the earliest members of The Ocean Cleanup, a Dutch not-for-profit developing technology to remove plastic from the seas.
But as time went on, Ressier realised she was tackling the symptoms rather than the problem.
“I wanted to be more upstream,” she said. “It’s such a massive problem that it’s hard to just clean it up.”
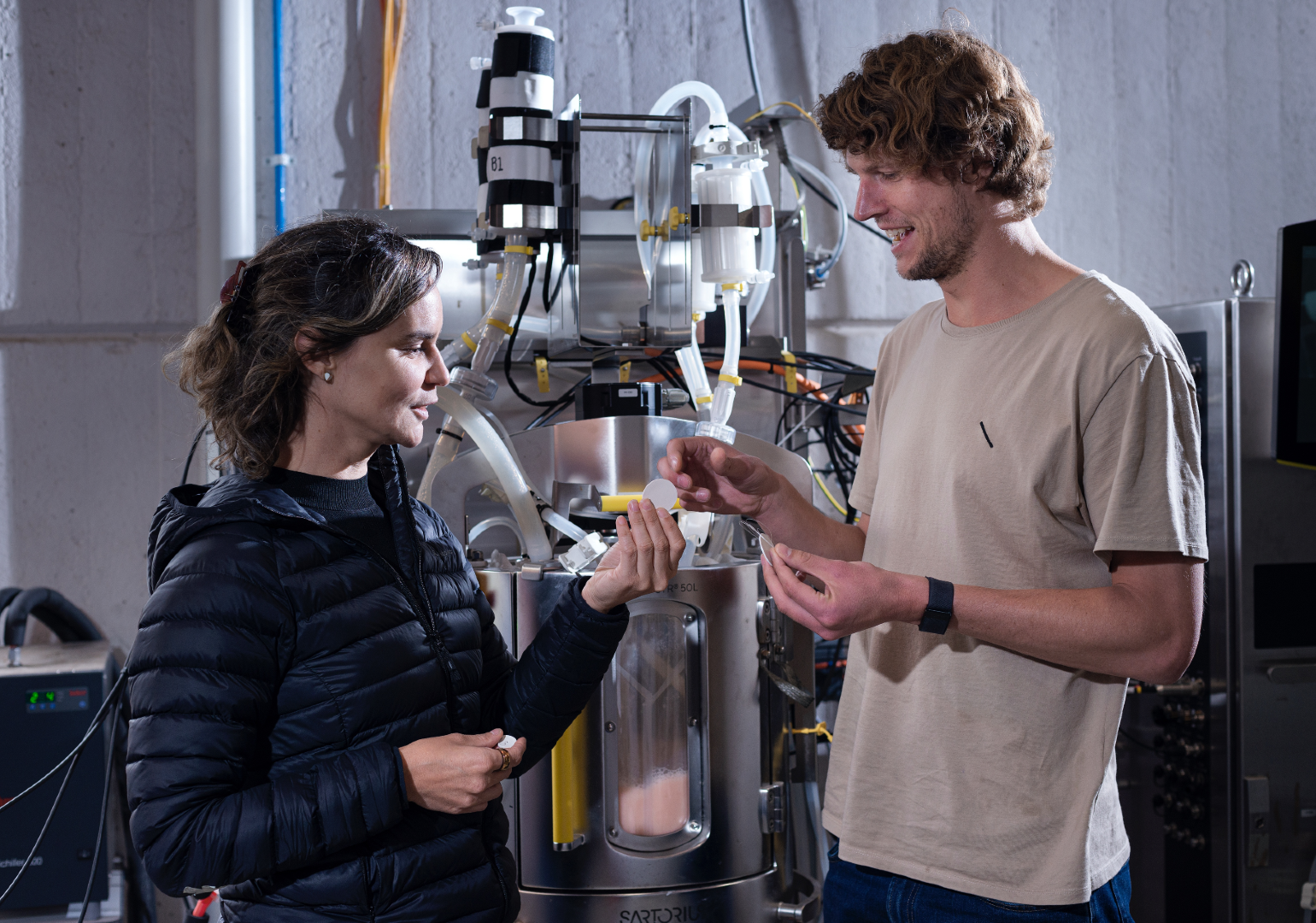
A beautiful idea
Dr Jesús Rodríguez, an agro-industrial engineer from Venezuela, moved to Australia to join the Uluu team.
Rodríguez had been researching PHAs in Italy but wanted to use his expertise to start PHA production rather than write reports.
“The idea of Uluu, for me, was beautiful,” he said.
Rodríguez was attracted to the idea of using farmed seaweed. Companies in other parts of the world are producing PHAs, but they’re made with glucose from corn or sugarcane.
“The cost of the PHAs is too high, and you interfere with the food of the people,” Rodríguez said.
PHAs are natural polymers and are very versatile. Through bioprospecting, many different kinds have been discovered in nature.
According to Rodríguez, different microbes produce different types of PHA, and what the microbes are fed also changes the material they produce.
Most of what is currently being commercialised is a PHA named polyhydroxybutyrate (PHB). It’s strong but too brittle for most applications.
Instead, Uluu’s seaweed-eating microbes produce poly(3-hydroxybutyrate- co-3-hydroxyvalerate) — PHBV — a co-polymer that’s more flexible than PHB.
One research and development area on which Rodríguez is focused is fine-tuning the properties of Uluu’s PHAs for different applications by adding tiny amounts of secret ingredients to the Uluu fermenters. That includes producing PHAs that could replace polyester in the fashion industry.
Ambitions the size of Uluu’s don’t come without risks. Global production of farmed seaweed would have to increase dramatically to replace the plastics produced each year. It takes about 10 kg of seaweed to produce one kg of PHAs.
“We have a few million tonnes per year of seaweed that’s produced,” Reisser said. “But if we want to fulfil our ambition, we really need to be working on the ground with the farmers and finding ways to scale that.”
The technology also has challenges. Uluu is currently piloting its technology with premium fermenters used in the pharmaceutical industry to produce vaccines. But, to scale the technology, Uluu will have to employ giant fermentation facilities more akin to the ethanol and brewing industries.
“It’s a journey,” Reisser said. “But I’m a true believer that fermentation, or synthetic biology … is going to be the future for a few commodities. Not only biopolymers, like us, but also lab-grown protein.”
Reisser believes Uluu can one day compete with the cost of plastics produced from fossil fuels. That path includes selling the protein-rich, vegan by-products of the production process as aquaculture feed or protein powders.
“It’s very risky, the kind of thing that we’re doing, and we need the best engineers, the best scientists,” Reisser said. “But I think the great thing is: if you do nail that, you can turn a problem into something that’s actually good.”
The 2023 Hydrology and Water Resources Symposium aims to improve our understanding of the inherent complexity of water sources, hydrologic and ecologic systems in uncertain times. Register today.