Australian engineers have developed a cost-effective method to transform used plastic into nanomaterials and clean liquid fuel.
The researchers from RMIT University have pioneered a two-step technique that allows them to produce high-value products such as carbon nanotubes and clean liquid fuel from plastic waste.
First, they use high temperatures to destroy pathogens and microplastics in biosolids, and convert agricultural and organic waste into a carbon-rich form of charcoal called biochar. Then they use the product as a catalyst to upcycle used plastic.
Lead researcher Associate Professor Kalpit Shah said upcycling two significant waste streams through one circular economy approach could deliver significant financial and environmental benefits.
“Our method is clean, cost-effective and readily scaleable,” he said.
“It’s a smart solution for transforming both used plastic and organic waste — whether tonnes of biomass from a farm or food waste and garden clippings from household green bins.”
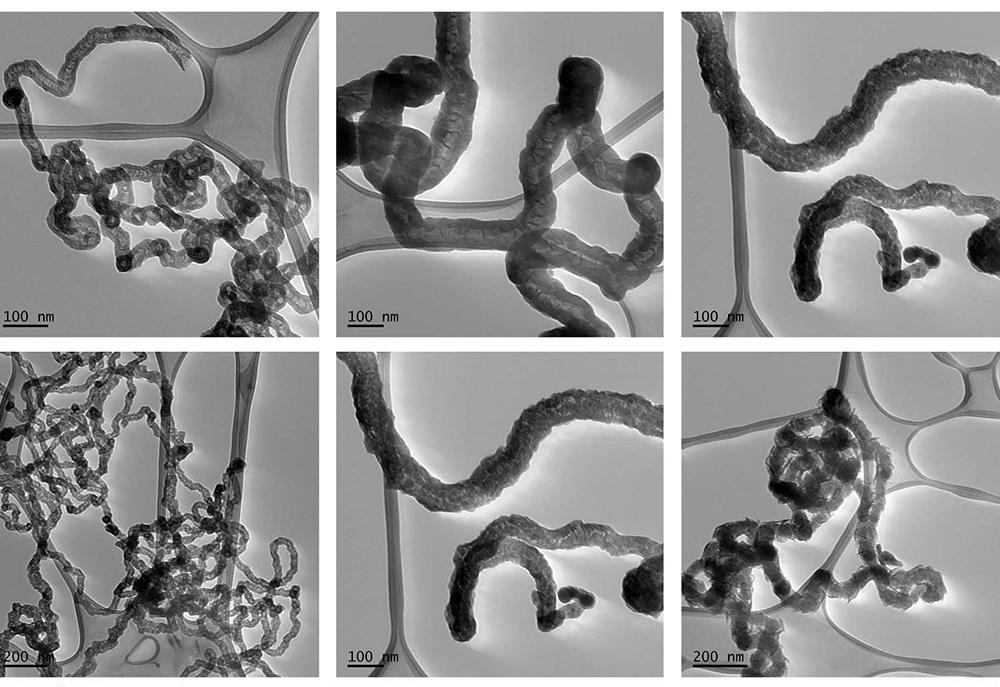
How it works
The biochar is used to eliminate toxic contaminants, such as polycyclic aromatic hydrocarbons (PAHs), as the waste plastic is broken down into its components of gas and oil. Meanwhile, the carbon in the plastic is converted into carbon nanotubes (CNTs), which coat the biochar.
These hollow, cylindrical, lightweight structures have exceptional electronic and mechanical properties. They can then be used in various industries, or the nano-enhanced biochar can be used directly for environmental remediation and boosting agricultural soils.
RMIT’s upcycling technology is a sustainable alternative for the production of these CNTs — a market projected to reach $5.8 billion by 2027.
CNTs are particularly in demand in the aerospace and defence industries, where they are used for parts. However they have a broad range of applications, including hydrogen storage, composite materials, electronics, fuel cells and biomedical technologies.
Shah said that the study has only investigated one type of plastic, however the approach would be applicable to a range of materials.
“We focused on polypropylene as this is widely used in the packaging industry,” he said.
“While we need to do further research to test different plastics, as the quality of the fuel produced will vary, the method we’ve developed is generally suitable for upcycling any polymers — the base ingredients for all plastic.”
A timely technology
The research comes as Australia moves towards a ban on exporting unprocessed recyclables from 1 July 2022.
A 2017-8 study found only about 10 per cent of plastics are being recycled, with a national target of 70 per cent by 2025.
Shah said that the technology could be used by local governments to turn waste into revenue streams.
“With Australia banning export of waste plastic from next year, it’s vital that we explore sustainable and cost-efficient alternatives beyond recycling,” he said.
“Upcycling plastic with home-grown tech would enable us to draw the greatest possible value out of our limited resources and bring us closer towards a true circular economy.”
That’s not all
Shah and his RMIT research group had a similar breakthrough earlier this year, transforming water industry biosolids headed for landfill into reusable products for farmers.
The unique pyrolysis technology (PYROCO) uses high temperatures to destroy pathogens and microplastics in biosolids, creating a similarly high-value biochar to that used in plastic upcycling.
“Developing new ways to squeeze the full value from waste resources is critical in our transition to a circular economy, so we are thrilled this Australian-first technology has reached full trial stage,” Shah said.
PYROCO is currently undergoing a “scaled-up” trial at a water recycling plant over a sustained period of time.