Ensuring patients can be transferred to and from aerial emergency vehicles safely and at speed is a life-saving endeavour. Integrating digital software and simulation tools allowed this Australian company to fulfil this mission.
When it comes to emergency services – whether medical retrieval, search and rescue, or firefighting – time is of the essence.
Every minute counts during an emergency, when the timeliness achieved in reaching a patient and transporting them to hospital can mean the difference between life and death.
In Australia, emergency missions can become more complex in rural remote areas, where access can be stymied by long distances, rugged terrain and wild weather.
To enhance emergency service fleet to cope with challenging conditions, Australian company Helir HeliMods, founded in 2002, configures aircraft for end customers globally. Local clients include the Royal Flying Doctor Service (RFDS) and the Royal Automobile Club of Queensland’s LifeFlight.
In 2022, RFDS’ Beechcraft King Air B360, decked out by HeliMods, was transformed into a flying intensive care unit – with the cabin’s control system facilitating the process of monitoring medical battery, oxygen capacity and flow rates, which doctors and nurses can do from their seats – as the cockpit’s digital pressurisation controller maintains patient comfort.
Key to the refit was the aircraft’s new stretcher system, which can be integrated into ambulance services for quick and easy transferral of patients.
But at the heart of HeliMods’ modification capabilities is Siemens’ technology – from digital software to simulation tools.
Samantha Murray, Vice President and Managing Director ANZ Siemens Digital Industries Software, sat down with create to discuss how the partnership between HeliMods and Siemens led to the development of a world-first Powered Aero Loader (PAL) system, used in emergency service fleets worldwide.
Simulating scenarios
The HeliMods PAL system, an automated stretcher system, can lift and transport up to 318 kg without any manual effort required. Integrating with road ambulances, PAL simplifies patient handovers between air and ground transport – saving vital time in emergencies while boosting paramedic safety by eliminating the need for physical lifting.
To support the complex design requirements of the system, computer-aided design (CAD) software, comprising advanced tools for 3D modelling, simulation (using Siemens’ Simcenter) and analysis, were applied, Murray said.
“The CAD software allows engineers to meticulously plan weight distribution, ensuring the structural integrity of the PAL system by providing real-time feedback on potential stress points and material choices,” she said. “This ensures that the system meets the rigorous demands of aeronautical applications, balancing performance with safety.”
Prior to physical prototyping, digital twins helped HeliMods to create a virtual replica of the PAL system, allowing for extensive virtual testing and refinement.
“This included simulating real-world conditions such as load stresses, aerodynamics, and operational scenarios,” Murray said. “By identifying potential issues early, the technology reduces the need for costly physical prototypes and accelerates the development process, ensuring the final product is both reliable and efficient.”
But given HeliMods technology is used in demanding conditions for emergency medical operations, simulation tools to conduct stress analysis were required to ensure the reliability and durability of the PAL system, Murray said.
“Simcenter allows engineers to model various scenarios, to assess how the system performs under extreme conditions,” she said.
“The simulations help identify potential failure points and optimise the design for maximum durability, ensuring the PAL system can reliably withstand the demanding environments it will encounter.”
Teamwork makes the dream work
During the development of the PAL system, cross-functional collaboration between design, engineering, and manufacturing teams was essential.
To enable seamless collaboration, teams and processes were linked via a digital thread using Teamcenter, Siemens product lifecycle management (PLM) solution.
“By providing a centralised platform for data management, Teamcenter ensured all stakeholders had access to the latest design iterations, specifications, and documentation,” Murray said. “This real-time sharing of information streamlined workflows, ensuring that the PAL system development was both efficient and aligned with project goals.”
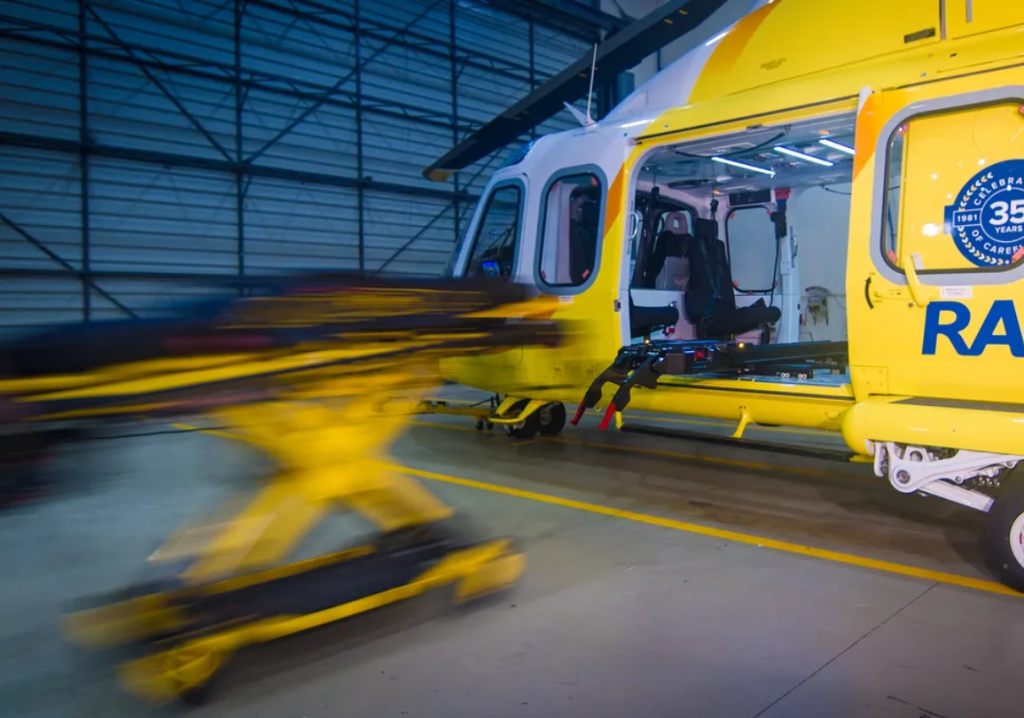
All iterative design changes were meticulously tracked and communicated to the relevant stakeholders.
“This ensured everyone involved in the PAL system’s development had access to the most current information, reducing the risk of errors or miscommunication,” she said. “[Using] version control and automated workflows allowed for smooth transitions between design iterations, supporting an efficient and controlled development process.”
Precision manufacturing
During the manufacturing process, Computer-Aided Manufacturing (CAM) was able to translate digital designs directly into manufacturing instructions, enabling the production of complex parts with tight tolerances.
“This ensures each component meets exact specifications, which is critical for the reliability and safety of the PAL system, especially in its critical applications,” Murray said.
Automation was integrated throughout the production process of the PAL system. By automating routine tasks and ensuring precision in machining, assembly, and quality control, production speed was increased and consistency maintained.
“The digital twin allows for integration of design, manufacturing planning and manufacturing execution in one integrated process,” Murray said. “This automates the update of manufacturing programs such as CAM and Manufacturing Operation Sequencing, and the utilisation of these programs and procedures on the shop floor by machines and operators.”
This results in shorter lead times, reduced human error, and a more efficient manufacturing process.
“All of [these elements] combined contributes to the high quality and reliability of the PAL system,” she added.
Scaling and customisation
The adoption of PAL has been increasing globally. DRF Luftrettung in Germany recently announced plans to introduce PAL on their H145 helicopters. Flexibility from the outset was required by HeliMods to appropriately scale the system.
“Teamcenter’s data management and configuration control, allowed HeliMods to adapt the PAL system to meet diverse customer requirements and regulatory standards worldwide,” Murray said.
Having design consistency and a managed digital twin across the design and manufacturing process allows for the efficient update of the design based on customer requirements and the feed through of those changes through engineering and planning through to manufacturing in a controlled manner.
“This means multiple customised designs can be managed and evaluated in the same environment … and configured as required using Teamcenter.”
HeliMods also leverages Siemens Opcenter Manufacturing Operation Management (MOM) software to enhance its manufacturing operations, ensuring that production processes are efficient, traceable, and aligned with quality standards.
“This provides real-time visibility into the manufacturing floor, allowing HeliMods to monitor production activities, manage resources, and ensure that every step in the manufacturing process adheres to the required specifications,” Murray said.
Future software advancements, including AI-driven capabilities, enhanced digital twin capabilities, and more integrated Internet of Things solutions, are expected to further enhance the design, manufacturing, and scaling capabilities of the PAL system.
“These innovations will likely improve operational resilience, business agility with predictive maintenance, real-time monitoring, and adaptive manufacturing processes – enabling HeliMods to continue delivering cutting-edge solutions in the aerospace industry,” she said.
With the right tools, Australian companies can accelerate innovation and solve problems that otherwise would be out of their reach.
“In the case of HeliMods, the outcome means precious seconds and minutes shaved off getting critically injured patients to the expert care they need,” Murray said. “In other cases, it can drive incredible productivity gains and therefore increase their competitiveness. And in other cases we can improve efficiencies, reduce precious raw materials, reduce weight, increase quality, reduce operating costs, improve safety and even address the full lifecycle of the product to have a full circular economy view.”
But in all cases, digitalisation is at the heart of achieving these outcomes.
“The good news is that the enabling tools are becoming far more accessible to a much wider range of businesses,” she said. “Engineers are at the centre of these incredible outcomes so it’s more important than ever that they look to rapidly harness digitalisation.”