Engineers from New South Wales are combining their 3D-printing capabilities to produce vital personal protective equipment (PPE) for healthcare workers responding to the COVID-19 pandemic.
Researchers from the University of Wollongong (UOW)’s Translational Research Initiative for Cell Engineering and Printing (TRICEP), ARC Centre of Excellence for Electromaterials Science and UOW’s Makerspace worked together to design a face shield to protect medical workers.
Once the researchers determined exactly what was needed, they went through a few iterations of the shield to make sure it was practical, TRICEP Director Professor Gordon Wallace explained.
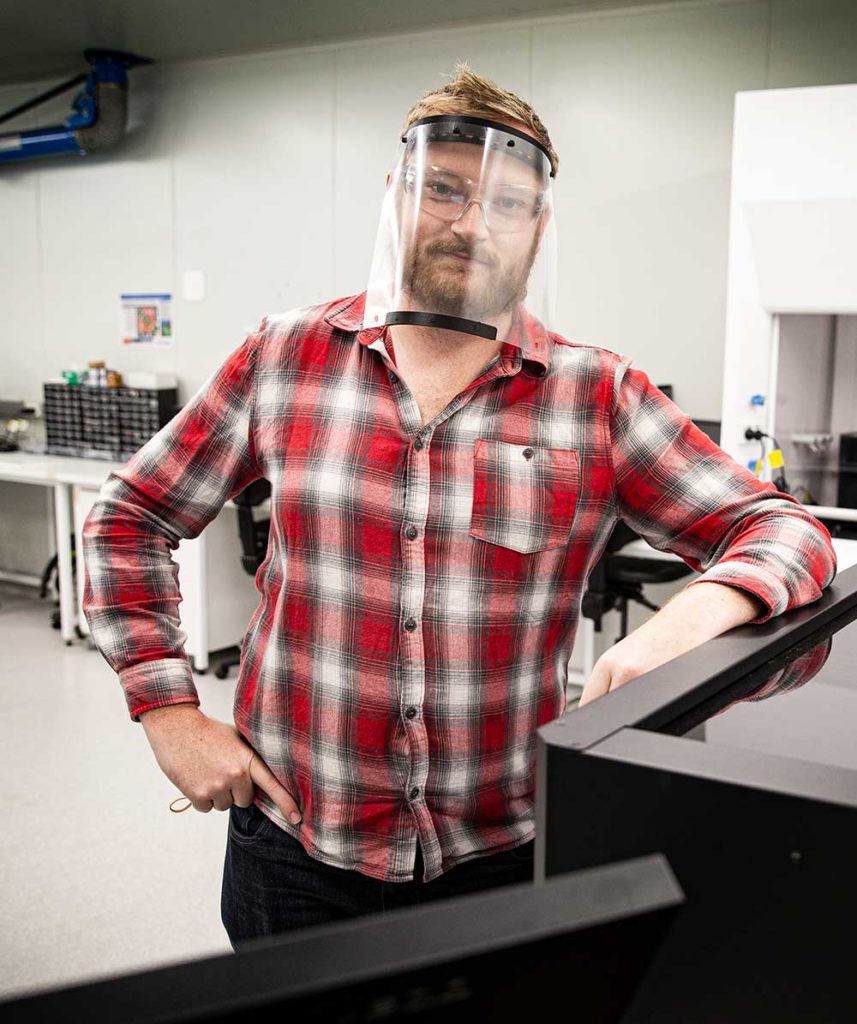
The shields have now been tested and approved for use in hospitals in the Illawarra region.
“We worked to get the design right for manufacturability, comfort and effective use in the health service, and now we are ramping up production,” Wallace said.
“At the same time, we needed to think about how we could make it in the shortest time period and use the least amount of material as possible.”
The initiative followed a call for help from Dr Bruce Ashford, who is leading Wollongong Hospital’s response to COVID-19.
“We floated the idea past the team at the University of Wollongong and TRICEP and sure enough they were able to help,” Ashford said.
“And we recognised pretty early on in the preparation phase for COVID-19 within the health service that face shields were a pretty critical part of PPE that was not going to be easily accessed for us.”
UOW Makerspace Manager Jessica Grozdanov said the initiative highlighted the importance of collaboration between researchers and medical institutions to solve challenges quickly.
“Makerspaces and other innovative manufacturing initiatives are increasingly playing an important role in the response to crises, as we can respond quickly to a particular need and can offer innovative, local solutions in high-priority scenarios,” she said.Cam
Production of the shields began with 40 machines in an empty lecture theatre at UOW and quickly scaled to more than 100 machines, with the team expecting to be able to produce 2000 per day.
Local startup joins the effort
Wollongong-based startup Me3D is also helping with production.
What began as three uni friends tinkering in a garage became Me3D, a business with a mission to expand STEM education by creating and designing 3D printers for school children.
But with schools closed, Me3D co-founder and engineer Matthew Connelly said the business was able to join the production effort.
“We’ve had quite a lot of stock left over, so one of the things we are doing with it is taking it out of storage and manufacturing some critical PPE for our nurses and doctors,” Connelly said.
The team is also testing more sophisticated 3D-printing designs, including prototyping components for ventilators.
“The next challenge for us will be whatever challenge the local area health service brings to us, whether that is in the area of valves or splinters for ventilators or other components that they need,” Wallace said.
“We are looking at our capacity to do some of these more sophisticated things should that need arise … It has been amazing how people have come together so quickly. That spirit of collaboration across the health service and university is really enabling us to move forward very quickly.”
Is the print file available for the 3D printing of protective equipment for hospital workers? If so, can the developers share it with others who can print protective equipment for hospital workers in other regions?
I’m actually the guy in the red shirt, Gordon is the one with the soul patch.
Hi Cameron,
Sorry about that! Captions have been updated.
Best,
Ruth
the designs are adapted from the PRUSA face shield.