As manufacturers pivot to produce goods that are essential for the health and safety of Australians, the industry is learning lessons about what the future might hold.
When tens of Australian Defence Force (ADF) personnel make a special trip to your manufacturing plant to analyse and boost your capabilities, it fast becomes apparent that your business is a player in a very important game.
This was the experience at Shepparton based Med-Con, Australia’s only medical mask manufacturer. At the time, Med-Con produced two million masks annually, or about five per cent of the national market. The rest came from cheaper suppliers in Asia.
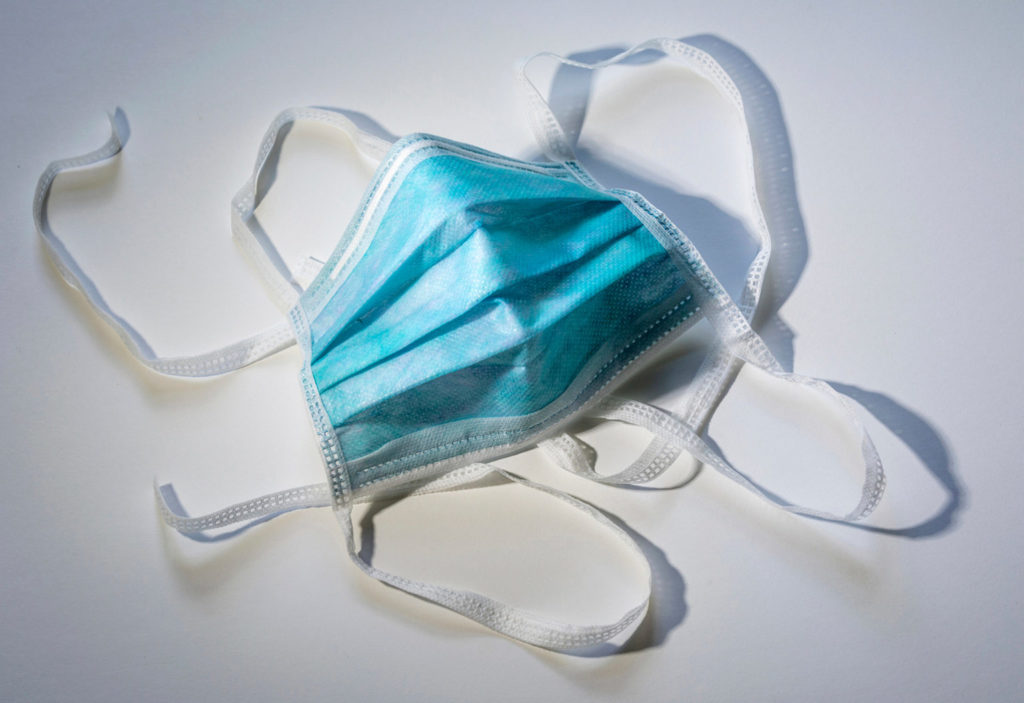
However, a secure response to the COVID-19 threat meant Australia would require its own supply, one that would not ebb and flow with the vagaries of international relations. The Victorian company would need to boost its production capacity to 50 million masks annually, but that was easier said than done.
Only two of three mask-production machines at Med-Con were operational. All were old and all would need to be running efficiently, 24 hours per day, to reach the required output.
“This equipment was built in the 1980s by local engineer Joe Carmody, who I believe is now 94 years old,” said Earle Roberts, mechanical engineer and CEO of Foodmach, the company commissioned by the government to modernise the machines.
“The original designs were lost, so the intent of the ADF was to disassemble the machine not in operation and reverse engineer [it]. They had a dozen engineers on site to disassemble and 3D-model that third machine.
“On a Monday afternoon we put forward a proposal as to how we’d attack the project. That Friday we got the go-ahead. We worked through Saturday, Saturday night and Sunday doing a handover with the ADF. On Monday we started cutting steel.”
#YourADF has concluded its support to Med-Con, a surgical face mask manufacturer near Shepparton in regional Victoria. #OurPeople commenced support at the factory on 7 March 2020 as part of #OpCOVID19Assist and have significantly increased Med-Con's production capacity. pic.twitter.com/f2iTnmHNSy
— Australian Army (@AustralianArmy) April 29, 2020
Pivot is on point
This pivot, often toward producing some form of personal protective equipment, has become a familiar story over the last few months both in Australia and elsewhere.
Local distilleries switched from gin and rum to hand sanitiser. Automotive engineers turned their attention to the production of ventilators. 3D printing groups came together to create devices and masks. Even boutique mountain bike makers got in on the act, with Yeti Cycles, based in Golden, Colorado, re-tooling their factory to produce protective face shields.
In Australia it has become a matter of national security. With much of our manufacturing talent and capability offshored over the last decade, policy makers, thought leaders and think tanks have realised some of that capability must return.
“Open trading has been a core part of our prosperity over centuries,” Prime Minister Scott Morrison said during a press conference recently.
“But equally, we need to look carefully at our domestic economic sovereignty.”
COVID-19 has revealed opportunities for improvement, and those improvements are being made at pace.
Breathing new life into the Med-Con machines, Roberts said, would typically take at least five to six months. He and his team were given eight weeks.
Similarly, said Dr Peter Meikle, mechanical engineer and CEO of Grey Innovation, a group of Australian businesses has quickly formed under his organisation’s leadership to produce ventilators in record time.
“Our business model is based on the strategic commercialisation of technologies in areas including environmental, homeland security and medical devices. This is familiar territory for us, but not in such a compressed time frame,” Meikle said.
“State and federal governments in Australia were being bombarded with offers of help, all well meaning. These came from everyone from significant corporate entities to the enthusiastic amateur. We approached the ventilator problem informed by our panel of clinicians and knew collaboration would be the key to success.”
The consortium, seeded with $500,000 from the Victorian Government, matching funds from the Advanced Manufacturing Growth Centre, and subsequently founded to the tune of $31.1 million from the Federal Government, includes businesses such as Bosch, ANCA, Braemac, Hosico, Marand, Knee 360 and many more. The goal is to produce up to 4000 ventilators.
“Engineering is central to success,” Meikle said.
“The importance of adhering to process is something engineers naturally recognise. When you can prove you are doing things that are meaningful and measurable, it means you cut through when you’re making an approach to government, or anybody else.”
Retooling a factory in record time
When we speak, Roberts and his Foodmach team are into day 32 of their reset of the Med-Con factory.
Their challenge began on day one, when they received 3D models from the ADF team during the handover. The models, although very well produced, sometimes did not show the internals of the parts, and sometimes did not allow for a deep understanding of critical dimensions such as plus or minus tolerance.
“Excluding fasteners and minor items there are 867 unique part numbers,” Roberts said.
“Across the three machines there are 5805 parts we have to manufacture or procure. In a lot of cases we have to find materials because there are section sizes we don’t use.”
Roberts said the team moved the machine shop to round-the-clock production in order to get the majority of the machine components ready.
“We partnered with some regional machine shops to give them some of the overflow [and] Melbourne’s Marand also completed some of the bigger assemblies,” he said.
“We’ve designed a completely new control system and replaced a lot of the old, mechanically linked drives with servo motors. We’ve put current-standard safety systems in, including laser zone scanners so staff can operate the machines safely and still gain access to all of the parts.”
It’s this modernisation, and the efficiencies and agility that come with it, that Australian manufacturers must consider if they are to truly prepare for similar pivots in the future, Roberts said.