Bringing the tallest residential building in the Southern Hemisphere to the Melbourne skyline involved a lot of ingenuity — and its immense height was not the only challenge.
At close to 319 m, Australia 108 is the tallest residential building in the Southern Hemisphere, rising 21.4 m above the neighbouring Eureka Tower.
Designed by architects Fender Katsalidis and built by Multiplex, the 100-storey tower has 1105 apartments, and its clean lines are punctuated by a glistening gold starburst that contains such resident amenities as a gym, a theatre, reading lounges and two infinity swimming pools.
Inspired by the Federation Star on the Australian flag, the starburst structure cantilevers up to 8 m from the building façade on levels 70 and 71.
It is the feature that presented the greatest engineering challenge, but it wasn’t the only challenge to overcome.
Securing the foundations through a deposit of Coode Island silt, for instance, required a complex concrete piling system that took almost 12 months to complete. Plus there was Melbourne’s gale-force wind to consider: coming off Port Phillip Bay, it can blow to more than 100 km/h.
There was also the issue of building upkeep. How do you integrate maintenance units above a sky-high cantilevered starburst? How do you clean the windows up there?
Digging deep
Ask these questions of almost any of the engineers who worked on Australia 108, and they’ll be well equipped to explain.
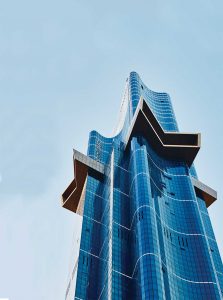
The various engineering disciplines — from structural to wind, façade to geospatial and more — worked hand-in-glove to complete the building, which is a 2021 finalist for Engineers Australia’s Australian Construction Achievement Award.
Structural engineer John Bambino, Southern Region General Manager of Robert Bird Group, which, along with a team of experts, was responsible for the building’s structural engineering, describes the collaborative approach as “absolutely amazing”.
“I’ve designed a significant number of high-rise structures over the past 30 years, but this was the most challenging and we all had to work together,” he said.
“It was a massive undertaking cantilevering a starburst on a building at that height. Can you imagine how challenging that was? The temporary work and deck, which had to be collaboratively designed and built, was a very substantial structure in itself.”
Australia 108 was built in four stages, and site excavation started in 2015. To accommodate adequate tower support through the site’s Coode Island silt, a combination of continuous flight auger (CFA) and bored concrete piles spanning up to 2.1 m in diameter were drilled up to 47 m deep into bedrock — and 10 to 15 m of that was rock socketed.
“You have to get the piling and rock sockets right, because they’ve got some pretty substantial forces in them,” Bambino said.
“We did a complete collaborative wind, structural and geotechnical study to ensure that the ground movement and soil-structure interaction was not going to exacerbate the overall movement of the tower.”
Solid to the core
A structure this tall requires more than a strong core to hold it in place. Australia 108 features a complex structural system that Multiplex Project Manager Darcy Holden described as a “technical beast”.
It includes a concrete core with 6 m tall, 900 mm thick outrigger walls located at levels 42 to 43 and 68 to 69. These structures transfer huge lateral loads from the core to a series of precast mega columns and a mega frame.
The outrigger walls contain 75 mm diameter Macalloy bars, which pass through the core and span the building’s width.
“Those outrigger walls are on steroids,” Holden said.
“They are almost a metre thick and the Macalloy bars have 120 mm stainless steel couplers that we had to design and have fabricated in Germany and shipped back to Australia.”
In collaboration with formworker Form 700, the outrigger system was prototyped and installed in a factory, before being disassembled and then reassembled onsite. Bambino explained that every element of the building was modelled using 3D drafting and finite element modelling programs to mitigate potential clashes on site.
“We then applied all the loads to the model and fed that data to the wind engineers who built their model,” he said. “They’d then test it and we’d feed it back into our model. It was an iterative process to get it 100 per cent right.”
Australia 108’s floors are flat, two-way, post-tensioned plates on a ring pattern of precast columns and mega columns of up to 100 MPa.
The use of precast columns saved approximately one day per floor compared to in-situ; however, Bambino said it required additional layers of quality control.
“We were initially concerned that if we accepted a design approach that utilised 100 MPa precast columns without a very strict quality control process to ensure full grout coverage, it could potentially result in an unwanted bearing failure mechanism,” he said.
“The team investigated alternative grouting procedures adopted in similar circumstances around the world and eventually adopted a customised procedure with a strict quality control system that allowed accurate measurement of the amount of grout being used for full cross-sectional coverage. The procedure also utilised individual indicators to ensure each starter bar and grout tube was adequately filled.
“The final assessment and acceptance of this strict quality procedure was based on a full-scale prototyping with grouting volume analysis and assessment. We simulated a full-sized column with a glass base and grouted it and tested how the measurement indicators would work on site.”
When the wind blows
To counteract motion in the building and promote occupant comfort, a 300,000 L precast concrete tuned liquid column damper tank was incorporated into the design between the 98th floor and the underside of the penthouse level.
“The building’s designed to stand up safely in its own right without a damper tank; however, the occupant comfort criteria — the feeling of motion — would not be improved without it,” Bambino said.
“The occupant would feel more motion without the damper tank because it is a very effective and proven measure adopted to counteract the driving wind forces and improve occupant comfort. The damper also helps alleviate some of the in-service sway — up to 600 mm — which the building would experience without it.”
The tower’s glass-plated façade also had to accommodate movement. It comprises 14,854 panels and features a high-end unitised curtain wall system with a double silver low-emissivity coating on a double and laminate glazing.
The panels were prefabricated in China and packed into steel stillages, which were hoisted on to the scaffolding deck on every floor.
A series of stack joints on each floor allows the façade panels to open and close to absorb the building’s vertical movement.
Rickard Engineering provided façade engineering services to Minesco, which supplied the building’s aluminium and glass curtain wall. Each panel of the façade was drawn in AutoCAD to model the movement.
Even though the glass panels are flat, the building has a curved geometry, affecting the building movement. The Rickard team drew each panel as it would move to see how it was going to deflect, and then made sure that the façade could accommodate the deflection.
Star attraction
The building’s distinctive starburst comprises four sections that project out of the building envelope.
The sections are designed as integral systems, consisting mainly of steel beams and trusses. Composite slabs form the top and bottom of the starburst, which are connected on each side by trusses. The gold aluminium panels are only about 3 mm thick and were installed on trusses in a factory and transported to the site at night by truck. The heaviest truss weighs about 16 t.
“The starburst was probably the single biggest challenge of the project from an engineering point of view,” Holden said.
“Looking back, I’m still amazed at how we did it and how well we executed it.”
The starburst had its own Multiplex team, which explored safety and design for about 18 months prior to its construction.
Meanwhile, Robert Bird Group had a temporary works division to engineer the temporary structures needed to install the starburst, such as a construction platform and protective screens.
Holden said 3D modelling and a five-minute animation video detailed the installation of the temporary decks and screen, as well as the installation of the gold aluminium panels and the steel trusses.
“The animation also showed how we’d deconstruct the temporary works, take off the screens, remove the decks,” Holden said. “It’s not easy to get a crane in to pull these platforms out, so we had to use temporary motorised winches to hook up to the main chains of the crane and skate the big decks out.”
Maintenance matters
As Australia 108 is classified in a super tower category, fire engineering requirements are what Holden describes as “above and beyond what you’d see in a normal building”.
While residents located on level 67 and below would use the stairs to exit the building in case of emergency, those on level 72 and above can use the lifts.
“The building has been designed to have smoke curtains that drop down and basically segregate a section of the lobby,” Holden said. “Residents can enter through a door and take the lifts straight down to the bottom floor.”
Building maintenance also required special considerations. The building has five maintenance units, including four located below the starburst at level 68 and a telescopic unit on the roof level, which cleans from level 100 down to level 72 above the starburst.
Li Yang, Project/Technical Director at Aurecon, was the company’s lead façade engineer on the project.
He said integrating the maintenance units presented a significant challenge as the maintenance rails above the starburst puncture the façade. As a result, the maintenance was integrated prior to installation.
“The common thing about façades when they are not done well is that you get leakages,” Yang said. “So we prefabricated panels as much as possible in the factory to have less site work, because at that kind of level and with that kind of wind, it can be difficult to control.”
For Bambino, creating one of the tallest landmark structures on this side of the world presents “a nice talking point”.
“It’s still pretty exciting,” he said. “One of the most satisfying moments was when we tested the building using cast-in real time monitoring gauges and we discovered that we were pretty much spot on with our engineering theory.”
The real building is slightly stiffer than theory would suggest.
“Which is where you want it to be,” Bambino said.
“The cast-in gauges in the building measure the displacement in high winds and they show that we were better than our theory in reality. That’s really satisfying for an engineer.”
Audible concerns
Australia 108 has been in the spotlight after residents complained of loud creaking noises in the building.
“We are aware that some residents experienced noise generated by an extreme wind event in June,” a Multiplex spokesperson told create.
“We have reassured those residents that there are absolutely no structural issues at play. Buildings are designed to move in extreme wind and the noise recorded by some residents was simply the building behaving as it should.”
The non-structural components of tall buildings — from partition walls to pipes and electrical components — are also designed to accommodate movement. And, while occupants may not always feel this movement, they may hear it.
“When two floors move relative to each other, for instance, all the non-structural elements have to move with the floors, which can create friction and creaking noises,” explained Professor Emad Gad, Dean of the School of Engineering at Swinburne University of Technology.
“Most of the noise heard in tall buildings is generated from non-structural components and should not cause alarm in terms of overall building integrity and safety. But, from an occupant comfort and amenity point of view, it’s a concern.”
Gad and colleagues Dr Javad Hashemi and Dr Scott Menegon at Swinburne’s Smart Structures Laboratory recently developed and validated solutions with industry partners via the Multi-Axis Substructure Testing (MAST) system.
The MAST system simulates complex loads on structural components to assess performance. The researchers investigated the behaviour of full-scale 3D non-structural components, such as wall partitions and ceiling systems.
“We’ve been able to reproduce realistic building movements, generate the same noise that is heard in buildings using full-scale building components, and work with manufacturers of building components to see how their systems behave,” Gad said.
“From there, we’ve worked with system developers to come up with solutions.”
The solutions can also be retrofitted to existing buildings, Gad said.