Engineering innovation enabled a Canberra COVID-19 hospital to be built in record-breaking time.
The engineers and other staff at Aspen Medical are no strangers to pressure. After all, they’ve provided quality health care, including building the structures in which the health care was offered, in some of the most remote and unforgiving environments on the planet.
Why then, was there a sense of excitement and apprehension in the corridors of Aspen Medical when they were commissioned to build a relatively small hospital in the centre of Canberra?
“The ACT Government asked us to provide a COVID-19 hospital building that responded to the World Health Organisation’s standards,” explained Matthew Gygi, Aspen Medical’s Infrastructure Project Manager.
“So, in the design of the building, we had to implement COVID-19-specific elements and develop a facility that responded to the particular nature of this infection.”
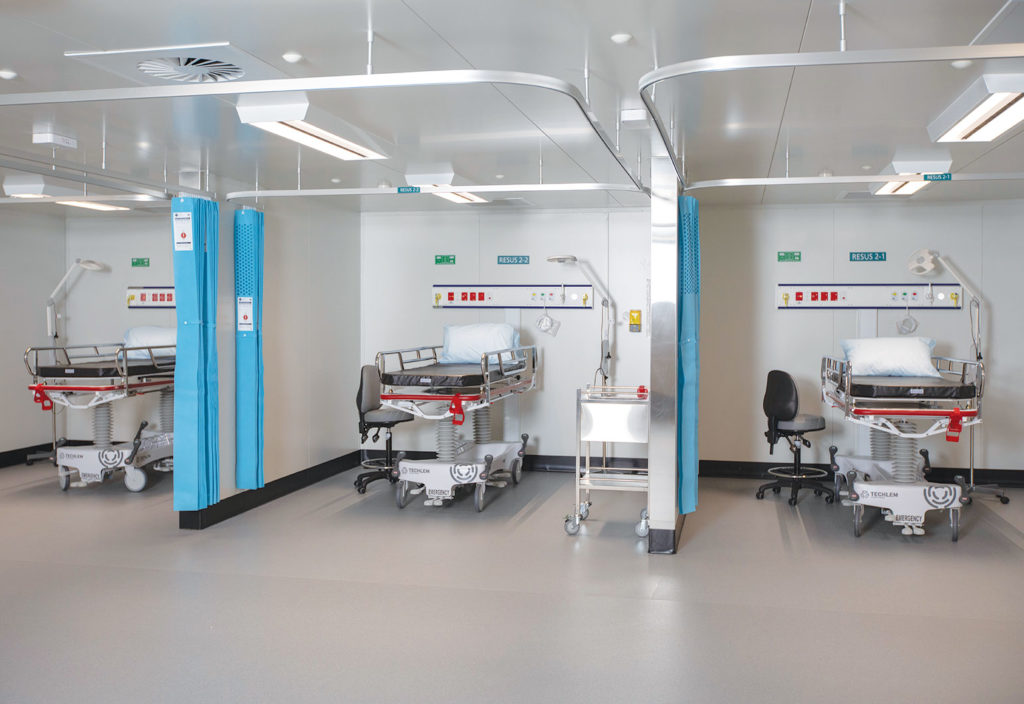
Right on time
Producing a building completely unique in its purpose was one great challenge.
The time frame, the fact that the build was happening during a pandemic, the location, and the agreement that the entire 51-bed hospital would be able to be packed down into shipping containers once the pandemic had ended were further complications Gygi would have to grapple with.
“From beginning of construction to completion we were given five weeks,” said Gygi, a civil engineer.
“While we’ve worked in high-pressure environments, such as the work we did during the Ebola crisis in Africa, our business is headquartered in Canberra. It was made very clear to me from the beginning that this would need to be a near-flawless build. It was a build in our own backyard, which was a great privilege, so there was no room for error.”
Aspen Medical had to rethink the rule book on hospital builds.
For example, Australian standards for recessed bays in most medical areas call for positive pressure aimed at preventing infections getting to the patient.
But, in this case, engineering solutions had to be developed to instead ensure the patients’ infection did not spread to others.
“In hospitals, a negative pressure room is generally a single room with walls around it,” Gygi explained.
“It isolates that patient from infecting everybody else. But in this case, we had to create 51 isolation areas, all mechanically controlled rather than using physical walls. The positive air pressure was instead in the staffing area. Air flows away from the staff and into the patients, all of whom have the same ailment.”
Engineers created a system by which the air in the building was ventilated 12 to 15 times per hour. All air leaving the building went through a heat exchange system that reduced energy requirements for heating the building in the ACT’s sub-zero temperatures by stopping heat being ventilated out.
Elevated ambition
Aspen Medical and its consultants designed the building for the Canberra COVID-19 hospital to be around half a metre higher off the ground than it might typically be.
This meant many services that would usually have to be planned into the roof area could instead be channelled under the floor.
For a similar reason, to ensure services were not fighting for space, the roof height was raised half a metre during design.
A new doorframe system was invented — one that simply snapped together. A single doorframe usually occupies 10 to 16 worker-hours to measure, cut, stand, hang and repair, explained Gygi.
But these doorframes, which showed up to the site pre-finished, took just two worker-hours each.
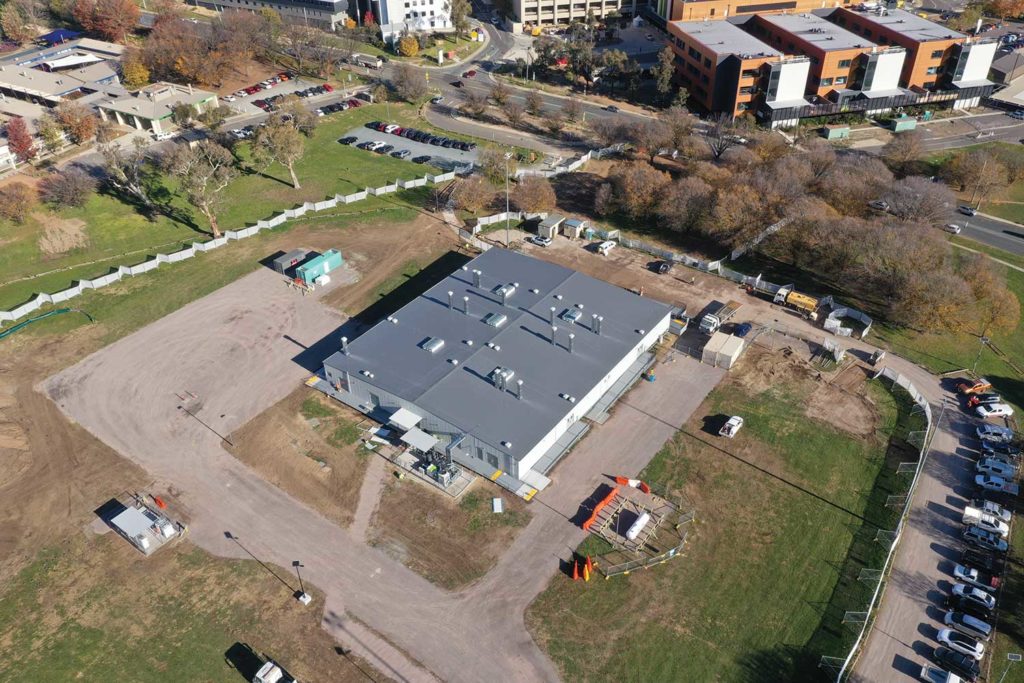
Community effort
Relationships with local businesses, many of which worked on the project over the Easter break, helped in meeting the deadline.
One other important and successful relationship, Gygi said, was with the ACT Government.
“The single greatest challenge was ensuring we were able to meet the functional requirements of the build within a fast-tracked timeframe,” said Duncan Edghill, Chief Projects Officer at Major Projects Canberra.
“We had to deliver an expanded emergency department for the community as quickly as possible during a time when everything was uncertain, from supply chains to availability of construction and operational workforces.”
Sophie Gray, Project Director of the COVID-19 Surge Centre at Major Projects Canberra, said being asked to lead this project was a “remarkable, once-in-a-career experience”.
“I think it’s fair to say we didn’t necessarily have clarity on all aspects of the project at the very beginning,” Gray said.
“Some things, such as best-practice design to support a COVID-19 response, were emerging as we progressed. But we had a very strong project management methodology and we had a very competent team containing individuals who were able to rise to the challenge.”
One aspect that assisted greatly with the success of the build, Gray said, was the fact that highly experienced, senior people worked from the site, rather than from a remote office. This meant decisions could be made on the run, rather than at progress meetings.
“This really wasn’t just a construction project,” Edghill said. “It was a community project.”
This article originally appeared as “Act fast” in the August 2020 edition of create magazine.
Gentlemen:
Heartfelt Congratulations to the Engineering Team! Well done sirs.. I also saw the advantages of a mobile COVID-19 specific testing, isolation, and treatment facility as early as February this year and even went to the extent of volunteering for free my time, skills and resources to our state- WA- for this purpose.
I have some technical questions regarding the hospital design I would like to ask the engineering team – which I do not want to be posted in this forum- is this possible?
cheers
Interesting article, but missing a critical element. Any article with “in record breaking time” should actually tell the reader how long it actually took – a critical element missing from this story.