An international team led by engineers from the University of New South Wales (UNSW) has made a breakthrough in reducing CO2 emissions.
The researchers discovered that liquid gallium can convert CO2 into oxygen and a high-value solid carbon product that has uses in batteries, construction and manufacturing of parts for vehicles and aircraft.
“Liquid gallium is super catalytic; it interacts with many things,” Professor Kourosh Kalantar-Zadeh from UNSW’s School of Chemical Engineering told create. “One observation we had was that when it interacts with high pressure CO2 it creates solid carbon and that can be easily lifted off the surface of the liquid gallium.
“As a solid this produced carbon is no longer greenhouse gas. You can use it in different industries, or you could bury it back under the ground if you like.”
Kalantar-Zadeh’s team worked with other Australian academics from RMIT, the University of Melbourne, Queensland’s University of Technology, and ANSTO’s Australian Synchrotron facility. Researchers from the University of California, Los Angeles (UCLA) and North Carolina State University were also involved.
How it works
Gallium exists in a liquid state at above 30°C, meaning it doesn’t take a lot of energy to produce liquid gallium – unlike other super catalytic metals such as platinum.
The process dissolves captured CO2 gas into a solvent around nanoparticles of liquid gallium. The CO2 is submitted to a triboelectrochemical reaction through nano-sized silver rods. Therefore the liquid gallium is mixed with silver fluoride at a 7:1 mass ratio.
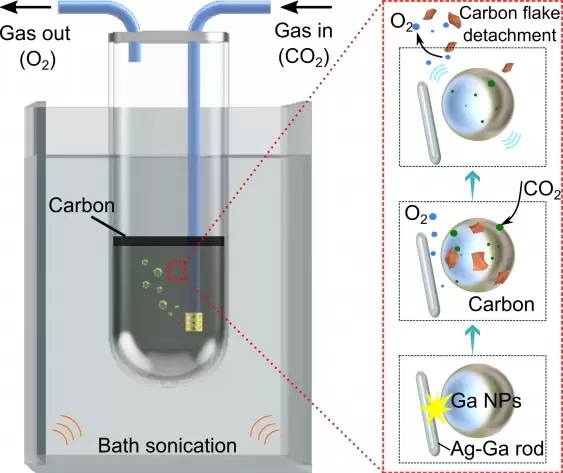
“To get the most out of the process we needed to find a way to maximise the surface area of the liquid gallium droplets. Therefore we mechanically agitate the liquid droplets to make them small in size and keep them from re-merging,” Kalantar-Zadeh said.
The result produces a carbonaceous sheet which floats to the surface of the container and is easily extracted.
These sheets are a high-value material that can be used in a number of products, such as to create electrodes in batteries, or to create carbon fibre for use in high-performance products like aircraft, racing cars and vehicles of the future.
Reducing emissions from cars
According to the research, published in Advanced Materials, the process was 92 per cent effective in converting CO2.
However, Kalantar-Zadeh is quick to point out that the CO2 needs to be pressurised to create the desired outcome. It can’t just absorb CO2 from the air or out of a power plant with low pressure.
“It could be something we retrofit to cars to capture the CO2 they emit,” he said.
Vehicles could be the perfect application for this research, particularly in cities like Melbourne and Sydney. A 2017 light vehicle produces nearly 180 grams of CO2 per kilometre.
“The heat engine of a car is already high pressure,” Kalantar-Zadeh said. “If we can connect it to a reactor with the liquid gallium, we could capture the CO2 before it can pass into the air.”
The next step for Kalantar-Zadeh and his team is to build a larger proof of concept to demonstrate the industrial implications of the technology.
Currently, the team has trialled a 2.5 L system that can process roughly 0.1 L of CO2 per minute. Now it’s a matter of making it even bigger.
“We’ve created a company called LM Plus to commercialise the scaling of the project,” Kalantar-Zadeh said.
“We’ve increased the volume by 10 times, the next step is to make it 50 litres and show that it works for at least three months without any degradation in performance.”
The LM Plus team hopes to have the new prototype developed within 15 months.