Converting plastic and polystyrene into durable railway sleepers could help reduce waste – and show how vital engineers will be to a circular economy.
According to Victorian company Integrated Recycling, which has been operating a factory at Mildura since 2010, a kilometre of railway track laid with its Duratrack railway sleepers uses 64 t of recycled plastic.
The sleepers are 85 per cent made of recycled material, a mix of “polystyrene and agricultural plastic waste, including cotton bale wrap, vineyard covers and pipe from the mining industry”.
They also have a lifespan of 50 years, compared to 14 years for timber, and are resistant to rot, fungus and termites.
In June, 190 of these sleepers were installed at Melbourne’s Richmond Station for an 18-month trial. It continues the apparent progress towards mainstream use of recycled composite sleepers.
Alternative sleepers are gaining acceptance worldwide, but, as Cong Qiu and Graham Tew of Monash University’s Institute of Railway Technology (IRT) wrote in 2017 in the magazine Newsrail, a “major issue within Australia is that there is no standard or code that currently exists for the use of these products”.
“There are some standards overseas, but they were developed for main-line operations,” Ravi Ravitharan, Director at IRT, told create.
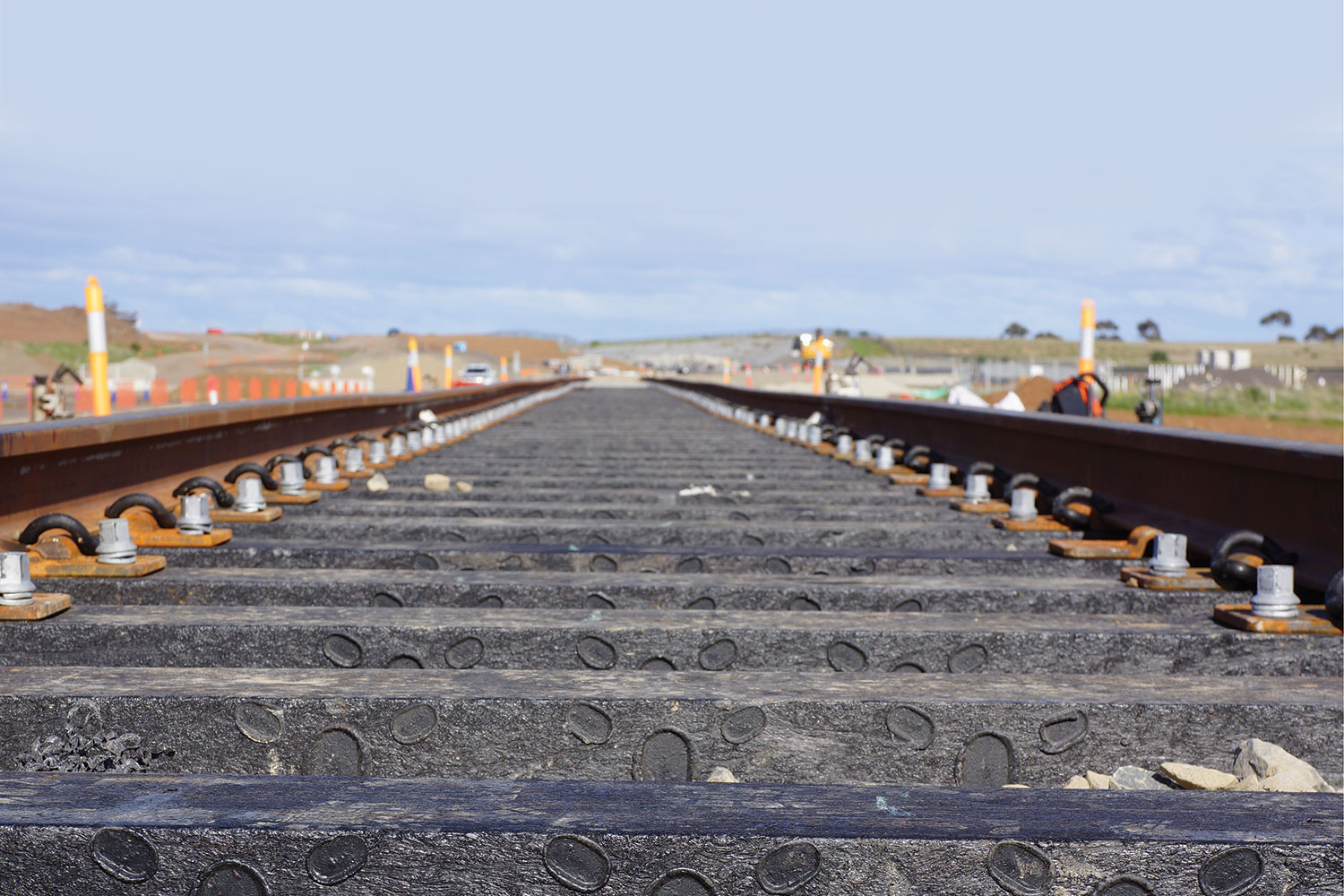
Since 2015, however, IRT has worked closely with industry to explore some of the issues requiring consideration when developing a new standard.
Standard bearer
IRT has worked with Integrated Recycling, beginning with a project supported by Public Transport Victoria (PTV) on recycled plastic sleepers for Tourist and Heritage (T&H) railways.
The shortage of timber for sleepers and the resulting high maintenance demands from using secondhand sleepers has forced operators to rethink their options. The outcome of this project was the development of guidelines for testing plastic sleepers to ensure adequate performance within T&H railways.
“A testing program of Integrated Recycling’s Duratrack product against these guidelines saw their product certified for use,” Ravitharan noted.
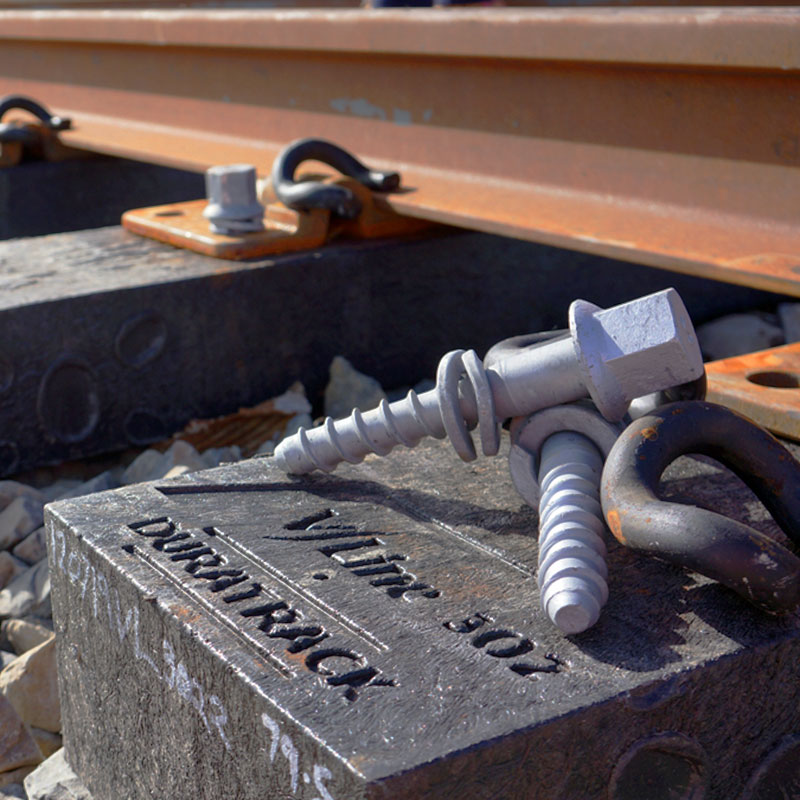
Ravitharan has more than three decades of experience in applied research in railway technology, beginning at BHP-Melbourne Research Laboratories, which turned into IRT in 2000.
His awards include an Academy of Technological Sciences and Engineering Clunies Ross Award in 2014, shared with Peter Mutton and Graham Tew.
“In the absence of transparent standards, it is difficult under the regulatory framework to introduce new products into the railway environment due to potential safety and risk concerns,” Ravitharan said.
“Innovation has to go hand in hand with clear standards and guidelines to support the implementation of new technologies into any railway operation.
“IRT is a major contributor in standards development groups broadly in Australia and is a key member of the development group now drafting a new standard for alternative material sleepers (AS1085.22) by the Rail Industry Safety and Standards Development Board, for consultation and introduction into the Australian railway environment.”
Ravitharan notes that a paper presented by IRT researchers at the Railway Technical Society of Australasia Conference on Railway Excellence in 2018 gained the attention of the Rail Industry Safety and Standards Development Board, which has led to the Richmond station trial and the drafting of the new standard.
Circular future
Whether it’s in infrastructure or elsewhere, the move to create value out of what was once waste and move towards a circular economy seems likely to continue.
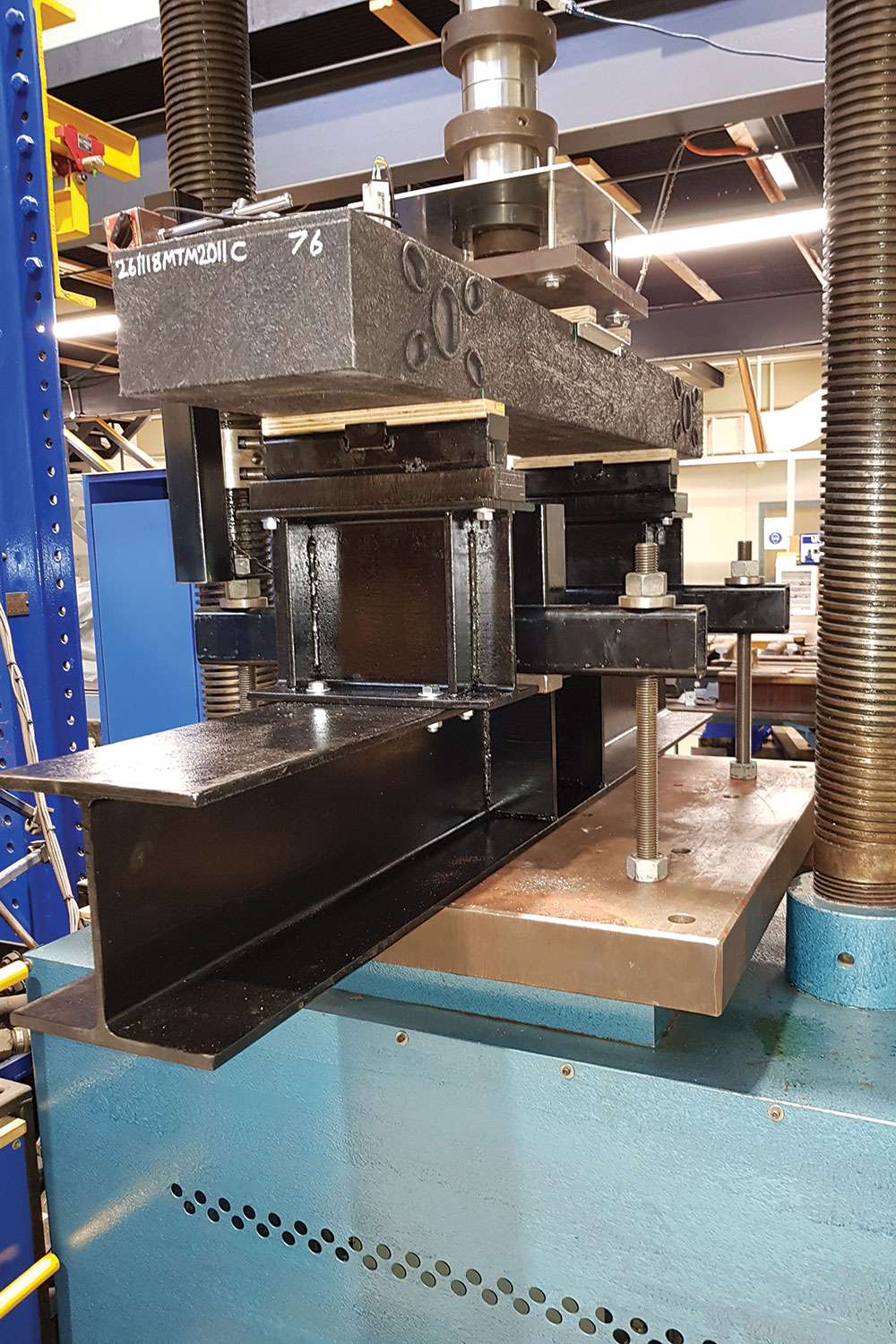
Time will tell how rapidly recycled plastic sleepers are adopted by state governments and others.
Ravitharan believes engineers will be crucial to the success of this adoption.
“We need to really invest heavily on the development of engineering capabilities well before we start thinking of capital projects,” he said.
“For me, I think engineers are extremely important in the development and creation of new technologies and innovations for the railway industry, and it’s a profession which has to be nurtured and continuously developed.”
Northern trial
Ravitharan said that though the interest in alternate materials for sleepers came initially from tourist and heritage railway operators, the technology has since gained attention from Queensland Railways (QR), who began exploring the development of a new sleeper suitable for QR operations.
“IRT was approached to assist Integrated Recycling in the preparation of documentation with the use of alternative composite sleepers for this particular tender,” he told create.
Investigations on the possible suitability of Duratrack sleepers are underway in Queensland, with 150 sleepers installed in October and in November 2018 for in-track trials east of Toowoomba between Helidon and Gatton, and in the Western Downs region between Chinchilla and Miles.
Two other companies have qualified for in-track testing with QR. These tests are expected to finish by the end of 2020, according to QR Post-trial, QR plans to replace 700,000 hardwood timber sleepers.
Sounds like a good idea.
My questions:
– How do they hold up to bushfires (including toxicity)?
– How are they disposed at the end of their life span?
I had thought of that 15 years ago,But instead use recycled chopped and shredded tyres. Reform them under huge heat and pressure into sleepers.They would then handle heat and extreme cold and be great to travel on
Love the concept … fire risk is an issue after the fire damage caused to indigemous artworks by recycled plastic walkways in WA … but I’m sure our talented engineers can build in a fire retardant.
I’m also interested in how it behaves with fire. Especially after the recent news about ancient rock paintings being destroyed from bushfire on recycled plastic boardwalks, leading the QLD government to remove such installations.
https://www.abc.net.au/news/2020-01-08/ancient-rock-art-lost-after-plastic-walkway-explodes-in-bushfire/11848938
Timber is a renewable resource and trees absorb carbon from the atmosphere and store that carbon in the woody matter of the tree.
When milled into a sleeper the carbon remains trapped for the life and after use in rail track it may have another life as a garden sleeper. Following that it is useful for firewood saving our fossil fuels.
All the while our regeneration forests are growing and sequestering more carbon from the atmosphere.
How much carbon is created and recreated with the use of plastic??
I hope this does not go the way of most great Australian inventions and ended up being made in China once the Australian engineers have solved the fire-retardant issue.
The miniature railway world (typically 185mm gauge) has been using recycled plastic sleepers for about 25 years. They are termite-resistant, rot-proof, UV resistant and appear to survive fires well as they are mostly buried in the ballast.
Dimensional stability is important, as any shrinkage can affect the railway gauge and there was a report of a bad batch causing such a problem about 15 years ago.
The experience “in miniature” is very positive, so it is good to see the concept extending into the full size railway world.
Success of such sleepers will hinge on having sufficient depth of clean well drained ballast below the underside of the sleeper. The American experience as long ago as the 1970’s required 200 mm of ballast below new concrete sleepers to avoid destructive conditions.
Replacing spiked timber with elastic fastened rigid materials alters the operating dynamics significantly, requiring close attention to supporting ballast to avoid conditions like the current extensive failures on the north east
The proposal looks very promising
Brilliant uses waste and saves the forests
Sounds like a good idea.
Timber sleepers develop cracks with age, which catch embers.
Plastic sleepers presumably retain their smooth surfaces as they age, giving embers little chance of igniting the sleeper.
Also, plastic sleepers can be embossed with useful information such as:
* owner
* maker
* date of manufacturer
* etc.
AK 2020-03-25/20:58
PLASTIC RAILWAY SLEEPERS Q&A
Wendy asks How are they disposed at the end of their life span?
* Well they can used for garden sleepers that do not rot, unlike timber ones;
* They can be recycled into new plastic sleepers.
Jason asks:
* What kind of plastic was used in the boardwalks that ruined pre-historic paintings? Depends, doesn’t it. Maybe the wrong kind of plastic was used?
“Track+Signal” magazine (V23 N3; Aug-Oct 2019 on pages 75-76) has an article on Plastic Railway Sleepers.
AK 2020-03-25/21:22
I have invented a New Water Saving Wheelie Bin the bin we are using now it uses 30 to 40 litres of water per bin, per week! Times 40 Million ltrs of water per week
There are over 40 million bins in Australia let alone other countries.
This New Water Saving Wheelie bin only uses 30 seconds of water to clean plus you will be able to disinfect your rubbish while it is still in the bin. Stops the stink and maggots.
If you would like to view this New Water Saving Wheelie Bin working, simply Google Martin Hayllar and a short vid will show you how easy it is to use.
I own the standard patent to this new wheelie bin.
We need to save water. Its going to run out sooner rather than later
The wheelie bin we now use can be refurbished or a new bin can be made.
If we refurbish the bins we use now, new jobs will be created by picking the bins up, cleaning the bins before refurbishment, and delivering them.
This could create thousands of jobs per town all over Australia.
We still need to clean our wheelie bins, using less water to achieve the same result.
All we have to do to clean this New Water Saving Wheelie Bin is bring your bucket with your cleaning fluid and your broom for cleaning, when empty, then scrub it out and connect your hose to the lid, turn the hose on and in under thirty seconds its clean. What we do now is leave the hose in the bin and scrub and half fill the bin with filthy stinking water. Then we have to tip it over to empty it, then we rinse it to get all the leftovers out! What a waste of water and effort. With this new bin, there is no lifting to empty it.
Great new project after the virus cost for the moulds is approximately $30 to $40 thousand. we can refurbish the bins we have
Why are all the comparisons of these new sleepers with timber sleepers. The industry standard is now concrete sleepers, so I would like some information on cost and longevity of these sleepers compared with concrete sleepers.
In my opinion, this is a better type of use for plastic than roadways. Tyre wear on roadways creates microplastics which then run off into waterways ?