A Queensland engineer has created a 3D-printed material to help protect buildings from damage caused by high impacts.
An off-the-shelf bioplastic used to 3D print geometric shapes could help protect buildings from collision damage and other high impact forces, equivalent to a car travelling at 60 kilometres per hour.
Dr Tatheer Zahra from Queensland University of Technology (QUT) told create that she has long been fascinated by the unique behaviour of auxetic material.
“The term auxetic refers to a material which tends to show negative behaviour, meaning they contract laterally when compressed in one direction or expand in all directions when stretched,” she said.
“This behaviour is mechanically defined as negative Poisson’s ratio behaviour — that is, a negative ratio of lateral strain versus longitudinal strain in any material — which enables auxetic materials to absorb shock and impact energies.”
The geometry of these materials plays a key role in their properties. Auxetic materials are often called metamaterials as these can be rationally designed to achieve high properties through advanced manufacturing methods, especially 3D printing.
“The recent surge in 3D printing of auxetic materials has inspired me to develop these geometries using sustainable polymers especially for making cementitious auxetic composites for building protection, which is a flexible and in-house alternative to manufacture these materials,” Zahra added.
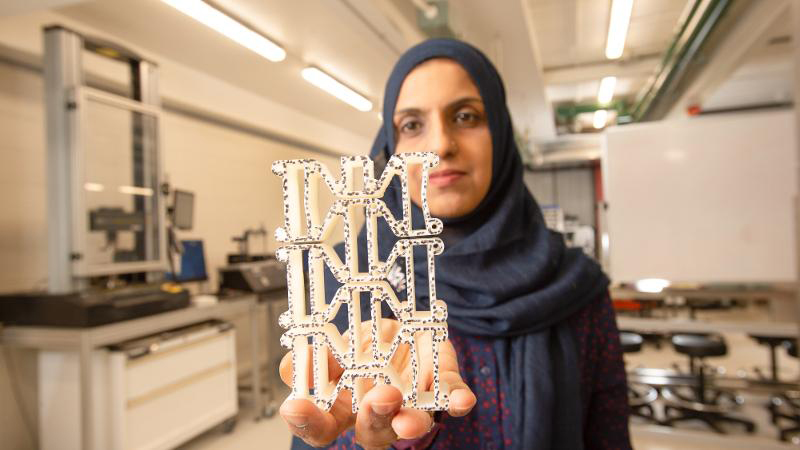
A material solution
At scale, composites embedded with these geometries could theoretically resist high impact or shock energy caused by gas explosions, earthquakes and wind forces, and car collisions.
“If auxetic geometries were embedded into the mortar to make protective composites, they would also be protected from microorganisms and temperatures over 60°C, and should last the design life of the structure,” Zahra said.
There are an estimated 2000 vehicle crashes each year in Australia alone. Zahra estimates that the direct building damage cost at 2.5 per cent means housing damage costs around $39 million per year — not to mention loss of life.
Her research was able to exploit a characteristic in the material to make composites that protect buildings from extreme loads such as impact forces caused by objects colliding with the building.
“Mechanical characterisation of one of the auxetic geometries I designed showed a negative Poisson’s ratio of -9 in compressive loads, meaning its lateral dimension can reduce 9 times compared to its long direction when subjected to compressive loads, which enhanced its density and energy absorption,” she said.
From concept to reality
Zahra used similar materials in the form of foam to make cementitious auxetic foam composites for civil engineering applications for the first time during her PhD.
One of the major challenges she has had to overcome in her research is problems with existing auxetic fabrics. Either they need to be imported from overseas, at a cost of about $400 per square metre, or the foam needs heat treatment for manufacturing and has low strength and stiffness, rendering it nonbiodegradable.
“As a structural engineer, the field of additive manufacturing was a completely new area for me. The first challenge was to learn about this technology, 3D printing filaments, and the available resources,” she said.
“I also wanted to use an ordinary 3D printer to control the cost of manufacture and, therefore, the second challenge was to develop a geometry as per the tolerance of these printers. I also refreshed my 3D CAD skills for designing these geometries.”
Only the beginning
Zahra noted that the process was highly collaborative, working with a multidisciplinary team through the design and testing.
“My research student Zane Gomez helped me design the geometries in CAD, while QUT lab technician Melissa Johnston provided guidance on both the selection of sustainable filament — bioplastic or polylactic acid filament — and manufacturing,” she said.
“QUT lab technician Glen Barnes also helped me test the mechanical properties according to standards specification for polymers.”
As for what comes next, Zahra said her research is only the beginning. For starters, these geometries can be further modified to suit their application for different protective applications because the production process is flexible and materials are readily available.
“The technology has a potential to be used in many other fields, such as crash worthiness of cars from collisions, biomedical implants and sports safety gear such as helmets and body shields,” she said.
“My vision is to employ them for making cementitious auxetic composites for making resilient infrastructure such as buildings and bridges to survive disasters such as earthquakes and collisions.”