Becoming a green energy society that meets its net-zero goals will require mining copper at a faster rate than ever. How can this paradox be solved?
One simple fact sums up the vastness of the challenge facing the mining sector and its related industries as the world races towards a 2050 net-zero deadline.
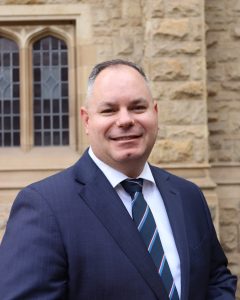
The lofty net-zero goal requires massive renewable electrification. Renewable electricity generation demands a great deal of copper. And to reach the 2050 goal, the world needs to mine more copper in the next two-and-a-half decades than has been mined in the history of mankind, said Professor Michael Goodsite CPEng.
“Copper is essential for us getting to a green and modernised society,” Goodsite, Professor of Civil and Environmental Engineering at the University of Adelaide and Director of the Institute for Sustainability, Energy and Resources, told create.
“Let’s take a common, coal-fired power plant like one we have on the east coast of Australia and replace it with wind power. To get the same amount of energy the current plant produces, we’ll need to build approximately 17 wind farms, each with about 100 windmills. Each windmill alone requires about eight tonnes of copper. And we haven’t even begun to connect the windmills to the grid with copper wire.
“So we need eight tonnes multiplied by 100 windmills, multiplied by 17 wind farms, to replace one coal-fired power plant. With current mining techniques and methods and the grade of copper necessary, you’d have to mine about 110 t of ore to get those eight tonnes of copper. Multiply that by 100 and then by 17 and you get what could be a very large hole in the ground.”
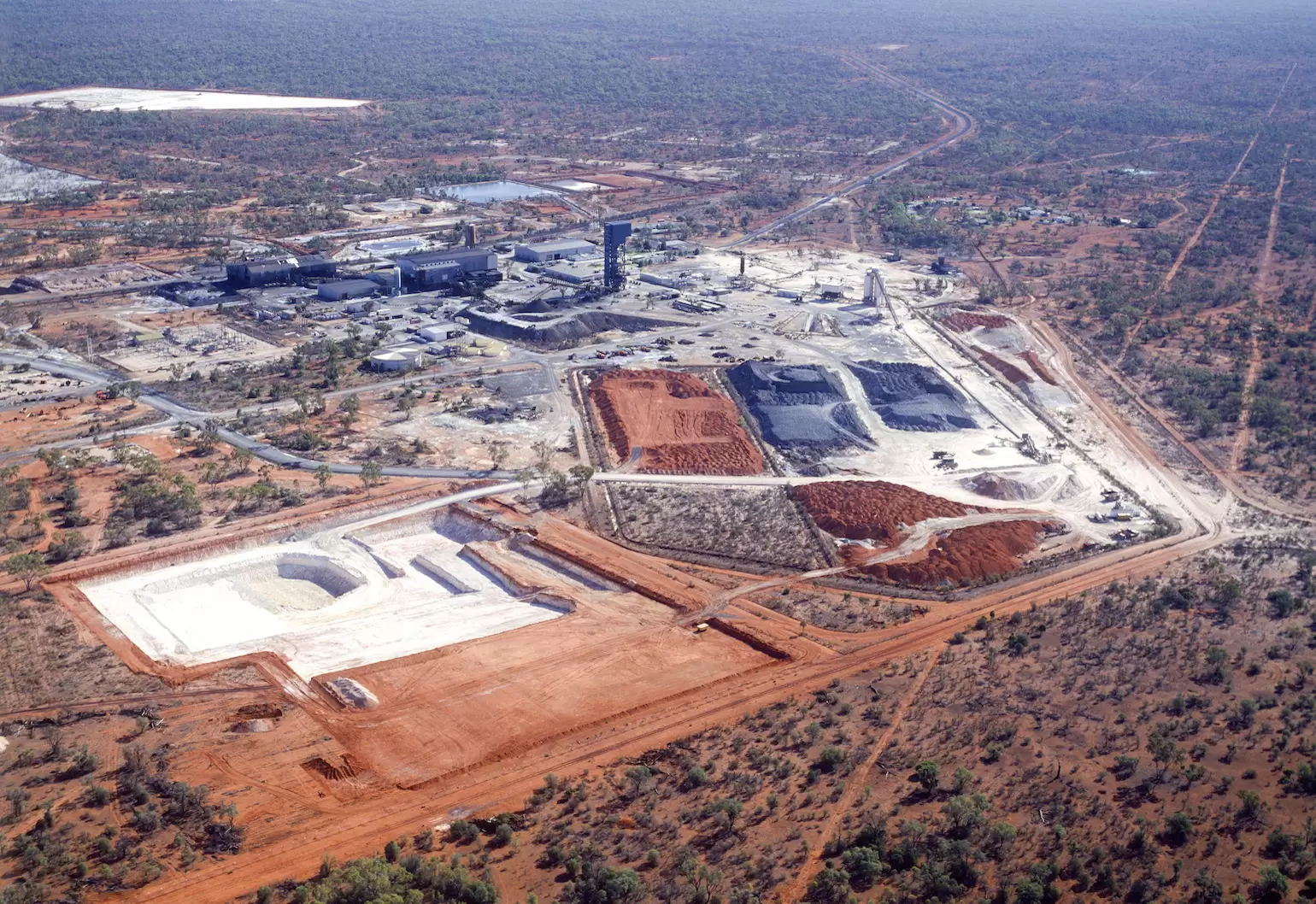
A recent report by global research and consultancy business Wood Mackenzie, Red metal, green demand: Copper’s critical role in achieving net zero, said that under the Paris Climate Agreement targets, 9.7 million tonnes of new copper supply from projects not yet sanctioned — over and above what is being mined right now — will be required over the next 10 years.
“To successfully meet zero-carbon targets, the mining industry needs to deliver new projects at a frequency and consistent level of financing never previously accomplished,” said Nick Pickens, Research Director of Copper Markets at Wood Mackenzie. “It’s the significant pull on the metal’s existing and potential supplies, and the investment required, that needs urgent attention.”
The Wood Mackenzie team estimates more than US$23 billion annually over 30 years will need to be invested to deliver the new projects.
Mission impossible? Some would say so. But many specialists in the area have confidence that new technologies, improved mining techniques and better processes will provide the solutions the world requires to meet Paris Climate Agreement goals.
Old dog, new tricks
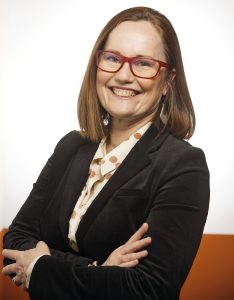
Methods of copper extraction have remained largely unchanged over many decades, said engineer Clare Sykes, Managing Director of LarkinSykes Advisory.
But those in the copper space are now urgently rethinking how they can best meet demands for a net-zero future. This will come through new projects, new processes, new operations, and from recycling.
Engineers are at the centre of each and every one of these areas.
“I’ve been doing work over the last few years with the International Copper Association Australia, where we’ve been looking at technologies that could be required to not only meet the resources demands of the energy transition but also to consider whether a copper operation could actually have a zero-emission profile in its own right,” Sykes said.
Sykes and other researchers have been looking at five parts of the copper mining value chain:
- Discovery: to find and define copper in the most responsible and sustainable way
- Water: optimising water-use and energy requirements in the extraction processes
- Material movement: how materials can be fragmented, sorted and hauled in a zero-emissions environment
- Ventilation: exploring technologies to more efficiently ventilate mines or mitigate ventilation demands and optimise a safe working environment
- Mineral processing: how valuable minerals can be separated from crude ores more efficiently.
“A typical, significant innovation in the industry could take 15 to 20 years to be fully embedded in the operational setting. But we don’t have that long,” Sykes said.
“There are many pathways via which engineers can play a very important role to unlock and commercialise innovations, to transfer technology from research into industry, and to implement those technologies on operating sites.”
Net-zero emission mining

In a report series recently published with the Clean Energy Finance Corporation, Erin Coppins, Research Portfolio Manager at the Minerals Research Institute of Western Australia, investigated emissions reduction options for a model copper mine.
She and her colleagues looked at different pathways and technology options for decarbonisation of the mine before 2050.
“It was a model brownfield operation,” she said. “The purpose of the report was to demonstrate what is possible even in the most challenging contexts for decarbonising a mining operation.
“There were four different pathways that were modelled, based around three core investment phases. All demonstrated that net-zero emissions could be achieved by 2040 with different levels of cost parity. Three of the four reached cost parity with business-as-usual by 2040. The pathways took into account a range of technology choices, including electrification and options for hydrogen and ammonia.”
On paper, at least, it is possible to turn an existing mine into a net-zero emissions operation in less than two decades.
“We looked at what are the key sources of energy usage and their emissions profiles,” Coppins said.
“Where do they occur within an operation and what are the levers that are available to address those?
“The key is to look at the challenge from an asset level.
Lots of decarbonisation targets might be set at a group, strategic level, but you really need to identify where the asset is now and where the main sources of energy use are. In line with industry commitments, the model mine in our report was able to reach net-zero by 2040 via several pathways, with electrification the most cost-effective route.”
That’s excellent news. But it doesn’t solve the big problem: the sheer volume of copper required to meet the demands of electric vehicles and windmills, battery storage and electrical networks. That challenge is being stared down by the Copper for Tomorrow Cooperative Research Centre bid.
Green energy society
Currently raising $4 million per annum from stakeholders, including mining and related companies and industry organisations, and seeking an additional $40 million in matching funds from the Australian Government’s CRC Program, the Copper for Tomorrow CRC bid recognises the copper paradox.
“How do we increase the production of copper needed for a green energy society? How do we achieve this while processing lower grade ores — a complicated and resource-intensive process — while also meeting environmental, social and corporate governance goals?” the CRC’s website asked.
Goodsite is the Research Director of that CRC bid.
“It takes 16 years, on a global average, from the discovery of the new commodity to the first shovel going into the ground in an operational mine,” he said. “So new mines discovered today won’t come online until about 2038.
“To reach our net-zero targets, we have to get better at mining deeper and extracting copper from more complex ores more efficiently, that is, meeting the copper — and other minerals — we need without further impact on the environment. That’s what we call the copper paradox. We might have to use more energy and more water. So, it’s a real challenge, and that’s why we’ve set up a collaborative research effort.”
The CRC intends to bring industry together with government, universities and external expertise from around the globe to address how to meet copper demand more sustainably.
“We will have to put a lot of knowledge together to achieve many of these goals,” he said.
“We want to use a lot less energy from the grid during extraction. We might consider blasting more and grinding less. We must use chemical and biological systems and their energy, instead of grid energy, to get to the copper in the ore.
“We’ll have to work with entirely new business models around the sale and export of green copper. Will people buy it at a premium? Every indication is that they will, since they do with aluminium. So what is that worth? And how do we prove it is green?”
Finally, Goodsite said, the geopolitical situation changes daily.
“How is that going to impact demand? And will people even be concerned if there are bigger security issues?” he asked.
“Currently, there may not even be enough critical minerals to enable more than one out of four drivers to own an electric vehicle. So, we’ve got a lot of work to do, and not much time to do it, if we are to meet the net-zero goals.”
Perhaps windmills are not the way?
An open minded researcher would surely be investigating gasification of coal and biomass, carbon capture and use/sequestration, nuclear power. On top of this your writer ignores the base load batteries/capacitors needed for when the sun does not shine, and the wind does not blow.
Open your mind to all the ramifications. Beyond this we need to consider the risks inherent in changing before economic and technical/practical solutions are assured, example overcoming hydrogen embrittlement.