Researchers have developed a conductive touch screen sheet 100 times thinner than existing materials – using items you could buy from a hardware store.
Pliable enough to be rolled up as a tube, the ultra-thin and ultra-flexible electronic material was developed by a Royal Melbourne Institute of Technology (RMIT) University-led research team.
Lead researcher Dr Torben Daeneke said most mobile phone touch screens were made of indium-tin oxide, a transparent material that is very conductive but also very brittle.
To address this, the team used liquid metal chemistry to shrink the thin film from three-dimensions to two-dimensions, resulting in nano-thin sheets.
“We’ve taken an old material and transformed it from the inside to create a new version that’s supremely thin and flexible,” Daeneke said.
“You can bend it, you can twist it and you could make it far more cheaply and efficiently than the slow and expensive way that we currently manufacture touch screens.”
This increased flexibility means the new material could potentially be manufactured through roll-to-roll processing, used in the production of newspapers.
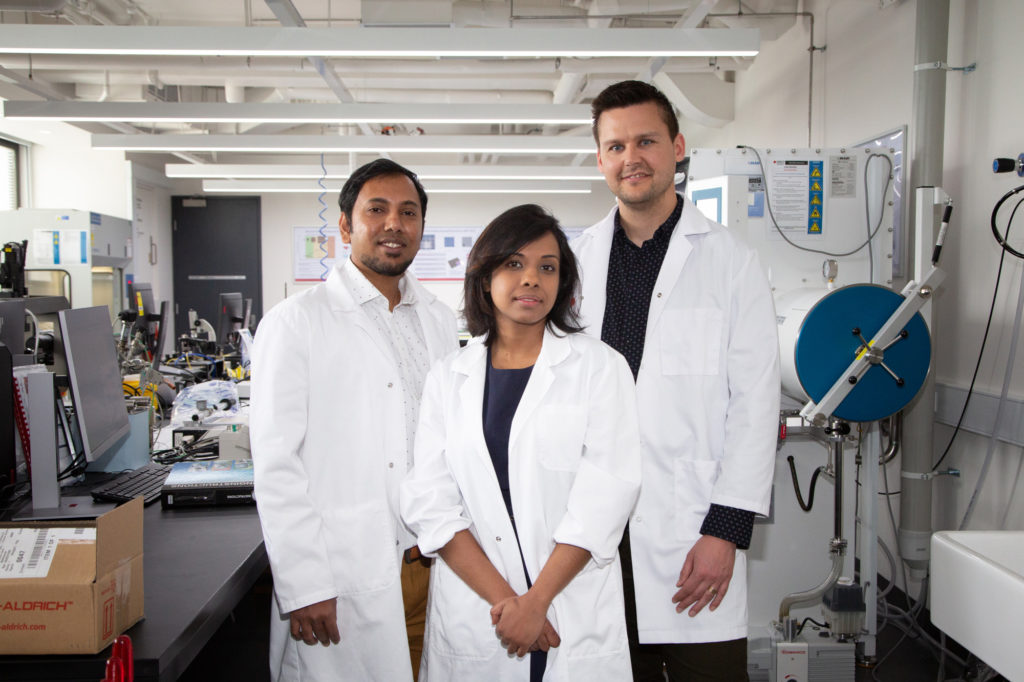
How does it work?
Liquid metal printing was used to create the new material. This involved heating an indium-tin alloy to 200 degrees before rolling the liquid over a surface to print the nano-thin sheets.
With the same chemical make-up as standard indium-tin oxide, the new material is not only fully flexible but is also more transparent. The new material absorbs just 0.7 per cent of light, compared to the 5 to 10 per cent typical of standard conductive glass.
“Turning it two-dimensional … makes it more transparent, so it lets through more light,” Daeneke said.
“This means a mobile phone with a touch screen made of our material would use less power, extending the battery life by roughly 10 per cent.”
This approach represents a contrast to the current method of manufacturing standard touch screens, which is typically conducted in a vacuum chamber through a slow, energy-intensive and expensive batch process.
“The beauty is that our approach doesn’t require expensive or specialised equipment – it could even be done in a home kitchen,” Daeneke said.
“We’ve shown it’s possible to create printable, cheaper electronics using ingredients you could buy from a hardware store, printing onto plastics to make touch screens of the future.”
Into the future
The team has created a working touch screen using the new material and applied for a patent for the technology. They also envisage the material could be used in LEDs and touch displays, and could even have applications in solar cells and smart windows.
“We’re excited to be at the stage now where we can explore commercial collaboration opportunities and work with the relevant industries to bring this technology to market,” Daeneke added.