In the lead up to UNESCO’s World Engineering Day for Sustainable Development (4 March), create is presenting a series of discussions with experts, revealing the evidence — including major innovations and projects, challenges and solutions, opportunities and risks — that proves engineers in Australia are leading the way to a better future. Find all create’s WED22 content here.
Don’t miss Engineers Australia’s free World Engineering Day webinar at 12.00 pm AEDT on Friday, 4 March.
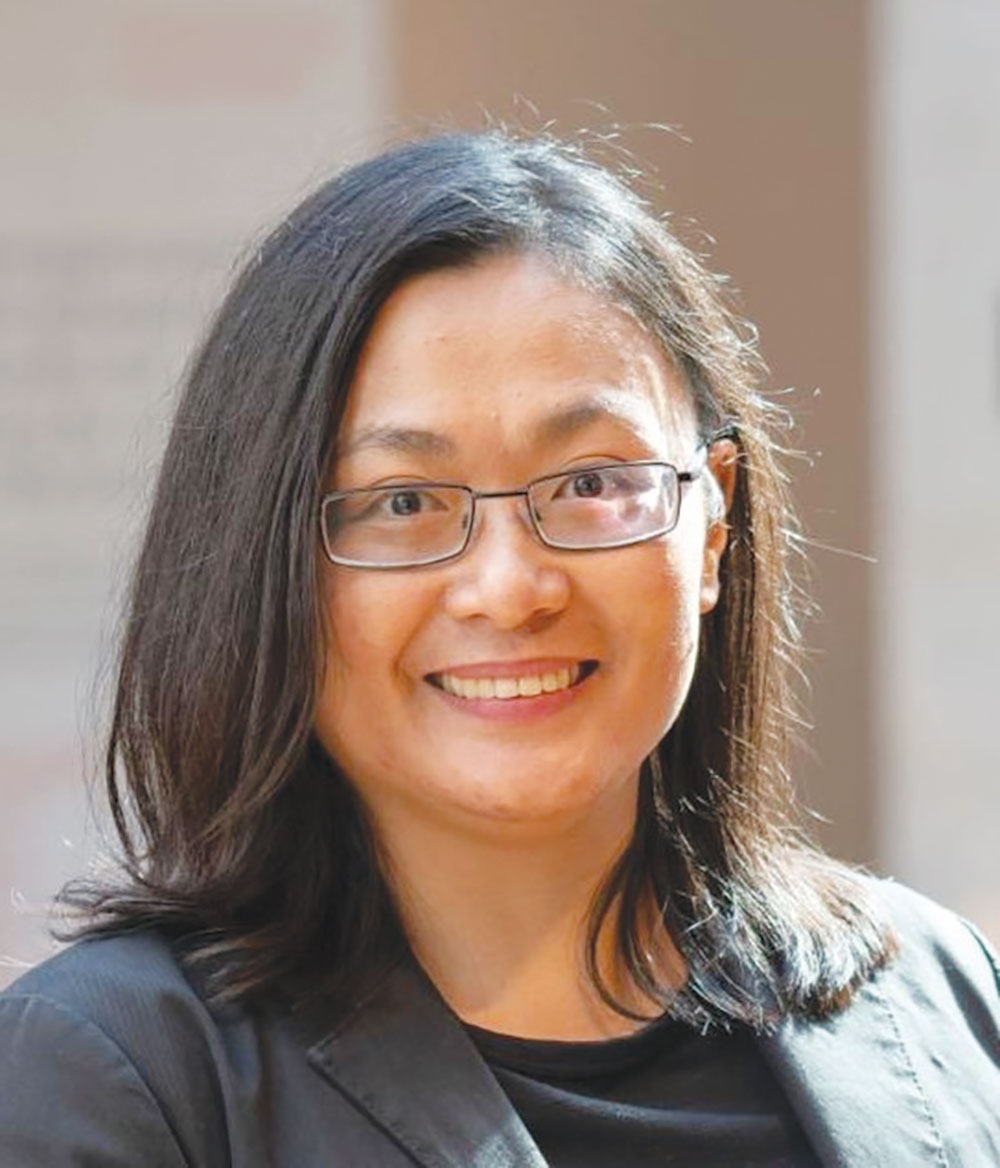
Where once concrete structures might have been expected to stand for 100 years or more, the typical lifetime is now 50 years or less as a result of regular updates and design changes, says Professor Vivian Tam, Associate Dean Research and Discipline Leader Construction Management at Western Sydney University’s School of Engineering, Design and Built Environment.
Often, once a concrete structure reaches the end of its life, the only option for most concrete waste is landfill. Only about five per cent is recycled into aggregate for low-grade pavement.
“My research looks into how waste concrete can go from being recycled into low-grade aggregate to instead being made as strong as virgin concrete,” Tam said.
Tam has developed a method to create such density and strength using recycled aggregate. It involves treating the aggregate in a pressurised chamber and injecting carbon dioxide. This increases strength and reduces water absorption, bringing the “CO2 Concrete”, as Tam calls it, up to the level of structural concrete.
At current Australian levels of production, CO2 Concrete could provide a net lifecycle benefit of $16 billion and save 2.68 billion kg of carbon dioxide emissions, she says, compared to a cost of $22 billion for using virgin concrete.
So what’s the problem?
“Engineers are reluctant to be the first to use the CO2 Concrete,” Tam said.
But things are slowly coming together, as smaller projects such as a drinking station for cows at Western Sydney University use the recycled product.
“I still don’t have an industry case study,” Tam said.
“Part of the problem is perceived risk, and part is the government not pushing projects to use it. In Japan, for example, the government says industry has to use more recycled materials on projects of certain sizes. That drives innovation.”
As a retired Civil Engineer, with 44yrs in production & erection of structural & architectural precast concrete, including research/materials testing, mix design programmes, etc, your CO2 concrete is of interest.
It does seem that there are plenty of precast products where CO2 concrete could be used but insufficient $savings would go to the users. Add to that the extra costs, delivery to stand alone CO2 treatment plants, control of input “waste concrete” structural integrity, redelivery to, and storage at ready mix plants & certification of the CO2 concrete finally delivered, are some of the inhibitors to adoption – in other words, supply chain costs, with no cost savings to the end users, and/or the specifiers.
Finally, unfortunately it does seem that the technically viable CO2 concrete appears to be not viable unless the reprocessing costs are offset by credits to all parties in the reprocessing & reuse chain, ie the $16b savings + credits for the 2.68b kgs of carbon emissions reductions, must be refunded to reduce the $22b cost of virgin concrete sufficiently to cover the extra costs & incentivise use by specifiers, and all other parties.
Well done Vivian – I can remember when Superplasticisers were considered too costly, so keep on developing your innovative CO2 concrete ; eventually an innovative way of refunding the $’s savings & carbon emissions $’s benefits will be solved.
Good answer. I am a CMT Technician and although not an engineer I agree with all of what you said. At the end of the process it comes down to cost and profit almost every time
I believe all construction materials should be recycled wherever possible. Love the idea of your CO2 concrete, I also prefer using bench tops made from recycled concrete ie Ceasarstone to those of granite.
I think recycled concrete should also be used for road surfacing and for curbing etc.
Recycled concrete is used a lot in civil construction, not just in roads but in drainage and building pads, sediment and erosion control, retaining, paving and footings to name just a few things…. Far more than just 5%.
This could be used for non structural use like pavings. Erosion control . Sea walls .with the sea level rising .it could be a saviour for some areas in every country