Textiles for soft robots, wearables and human-robot interfaces is a booming field of engineering research. No longer considered ‘passive’ materials, a new generation of fabrics are being put to work.
Until recently, robotic fabrics were attached to external machines that modulate factors inside them, such as shape, sensors or air pressure. Now, the emergence of fibres that can sense and alter structurally means that engineers can impart robotic functions into textiles — and open up a world of possibilities.
Garments that can regulate breath
A new fibre could help athletes and performers train their breathing, and be developed further to help hospital patients.
Researchers at Massachusetts Institute of Technology and Uppsala University and KTH Royal Institute of Technology in Sweden have created clothing that senses how much it is being stretched or compressed, and provides immediate tactile feedback in the form of pressure, stretch or vibration.
Multilayered fibres similar to polyester are thin and flexible enough to be used in standard commercial machines. They contain a fluid channel in the centre, which is activated as the system pressurises and releases compressed air or water into the channel, allowing the textile to act as an artificial muscle.
They also contain flexible sensors that can detect and measure the degree of stretching of the fibres. Researchers envisage that the resulting garments could help train singers or athletes to better control their breathing, and even help patients recovering from diseases such as COVID-19.
One of the researchers who helped develop the fibre, design engineer Ozgun Kilic Afsar, said the team was able to transfer the fabric from an expert singer to someone learning to improve their breathing patterns.
“We eventually were able to achieve both the sensing and the modes of actuation that we wanted in the textile, to record and replay the complex movements that we could capture from an expert singer’s physiology and transpose it to a non-singer, a novice learner’s body,” she said.
Afsar added that they hope to further miniaturise the whole system, including its control electronics and compressed air supply, to make it more practical.
Wearable soft robots to help injury rehabilitation
A multidisciplinary group from Harvard University’s Wyss Institute for Biologically Inspired Engineering, John A Paulson School of Engineering and Applied Sciences, and Department of Chemistry and Chemical Biology has developed what they call Smart Thermally Actuating Textiles (STATs) — soft textile robots that could enable new therapies for injury rehabilitation.
STATs work by inducing pressure changes through electrically controlling liquid-vapour phase changes in robotic textiles, eliminating the need for pneumatic tethers. For injury rehabilitation, they can activate nerve fibres to repair tissue damage, or prevent injuries in the first place by applying forces at certain frequencies, for example, preventing pressure sores in wheelchair users or bed-bound people.
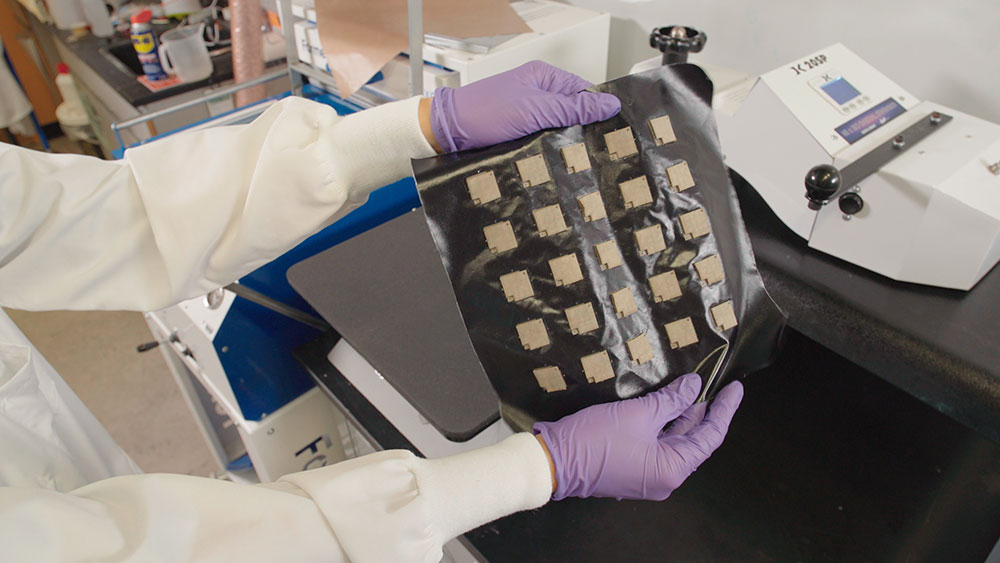
The researchers manufactured sealed pouches using a commercially available woven textile membrane coated with a layer of heat-sealable thermoplastic polyurethane and incorporating embedded electrically active components. The STATs’ electronic components were then powered through an enclosed engineered fluid vaporised by heat, which expands its volume up to 100-fold, allowing the fabric to increase and decrease its internal pressure significantly.
Study co-author Vanessa Sanchez said that STATs are lightweight and unobtrusive smart fabrics that she believes could enable a new range of robotic approaches.
“Our aim was to engineer robotic fabrics that can electronically sense and actuate, use integrated closed-loop feedback control to regulate themselves, and be manufactured in arbitrary shapes and large batches,” she said.
“They could be utilised in mechanotherapeutic wearables that, by applying defined pressure patterns, could accelerate tissue repair, in responsive cushions that could help prevent pressure sores… or even as dynamic garments in the fashion industry.”
Robotic fabrics that can create self-deploying shelters
At Yale University, researchers have turned their attention to the uses of robotic fabrics for space travel, such as in compression garments.
They have developed a material that includes actuation, sensing, and variable stiffness fibres while retaining all the qualities of soft textiles, such as flexibility, breathability, compactness, and low weight.
Funded by the Air Force Office of Science Research, demonstrations have shown that the design can turn itself from a flat fabric into a standing, load-bearing structure and even a small aeroplane.
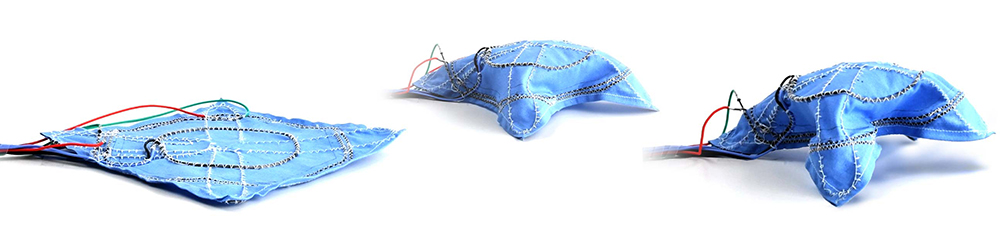
The research was published in Proceedings of the National Academy of Sciences last year. Lead author Trevor Buckner said the key to the design was processing functional materials into fibres that could be integrated into fabrics, through methods such as an epoxy embedded with a metal alloy that liquifies at relatively low temperatures.
“Our Field’s metal-epoxy composite can become as flexible as latex rubber or as stiff as hard acrylic, over 1000 times more rigid, just by heating it up or cooling it down,” he said. “Long fibres of this material can be sewn onto a fabric to give it a supportive skeleton that we can turn on and off.”
Buckner and the researchers also developed a conductive ink based on a Pickering emulsion to paint sensors directly onto the fabric, creating a material that detects changes and responds appropriately. The conductive composite self-coagulates around the individual fibres while maintaining porosity.
In order to make the fabric move, the researchers used shape-memory alloy wire, which can return to a programmed shape after being deformed, allowing for smooth bending motions.