When Tasmania’s tallest and most remote wind farm came online, it took the state to 100 per cent renewable energy.
When Beef farmer Royce Smith replaced his clothesline for the third time in five years due to wind damage, he knew he had the potential for a wind farm on his 1300 ha property.
But Smith wasn’t sure the developers who knocked on his door would take sufficient care of the land, which is steep and susceptible to erosion, so he joined forces with a local friend, Alex Simpson, mortgaged the farm and bought a met mast — a freestanding tower with measurement instruments — to document the wind resource.
As expected, the data confirmed the roaring forties gusting in from the Southern Ocean provided an excellent wind source.
Smith and Simpson spent almost a decade getting planning permits for Granville Harbour Wind Farm, 35 km north-west of Zeehan on Tasmania’s remote west coast.
Things moved quickly after infrastructure investor Palisade Investment Partners, later joined by John Laing and First Sentier Investors, took ownership of the $280 million development in early 2018, establishing the project company Granville Harbour Operations (GHO).
GHO appointed Ekistica, an engineering and technical advisory firm based in Alice Springs and fully owned by Aboriginal non-profit the Centre for Appropriate Technology (CfAT), to manage construction.
GHO valued Ekistica’s strategic approach to considering how location would affect the project and appreciated the firm’s plan to manage the project risks associated with the location.
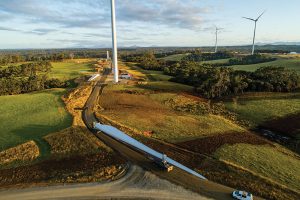
The multidisciplinary GHO project team included Ekistica as the owner’s engineers and project managers; Palisade Integrated Management Services (PIMS), who provided commissioning and operational services and supported the grid connection works; Wallbridge Gilbert Aztec (WGA), who acted as consulting engineers for the primary civil and foundation design; Entura, who undertook specialist technical reviews; SEEC, who specialised in soil and water management; Banksia who supported community engagement activities; and environmental scientist Chantel Hodgson, Principal at ECOsult.
After a 30-month build, the wind farm started commercial operations in December 2020.
When the 29th of the 31 wind turbines for the 112 MW Granville Harbour Wind Farm came online in November 2020, it took Tasmania to 100 per cent renewable energy and added enough clean energy to power about 46,000 homes per year.
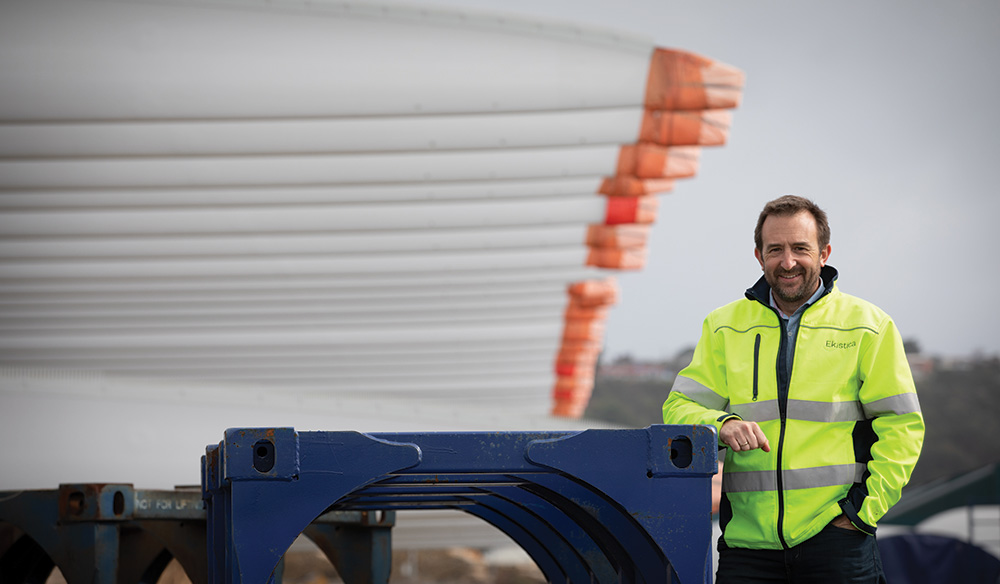
Isolation and innovation
On Google Earth, Granville Harbour Wind Farm appears as a small, cleared patch of land surrounded by bush.
Even though the site is half a continent away from Central Australia, Ekistica’s Managing Director and Project Director for the wind farm, Engineers Australia Fellow and Chartered engineer Lyndon Frearson FIEAust CPEng, said the isolation felt familiar and inspired him to draw heavily on the knowledge and capability developed over decades working with Aboriginal and Torres Strait Islander peoples to create place-based solutions.
“The environment and geography were the key drivers of the entire project and required a completely different way of thinking about the engineering and how to integrate the design into the farm,” Frearson said.
“We do complex, detailed engineering, but it’s always framed within a very specific way of thinking. We believe you solve complex technical problems through a deep understanding of context by taking the time to understand the environment in which you’re operating.”
Out-of-the-box thinking
“Building a very large piece of infrastructure on a remote property with superb environmental heritage values meant the challenges associated with the project were quite significant,” Frearson said.
One of the most significant issues was getting 372 oversized truck loads, weighing up to 150 t and some as long as 75 m, from the Port of Burnie to Granville farm via a single, very winding road.
The components for Granville’s 137 m high towers included the boxes, called nacelles, that sit on top of the turbines and house the drive train and other tower-top components, which weigh about 120 t each; the tower sections which weigh up to 65 t; and the 62 m long blades.
The turbines were manufactured by Vestas in Vietnam, then shipped to Burnie, where the project team negotiated with the Tasmanian government and the Port of Burnie to have them stored in the timber yard of an old paper mill next to the port.
Getting the equipment down the extremely winding roads, required extensive coordination with emergency services, councils and local businesses.
The project team had to ensure everyone was aware a huge truck would be coming through and put in place a plan to manage emergencies because nobody else was able to use the road.
But Frearson said getting the equipment to the site proved to be only the first of a series of hurdles they had to overcome in constructing the wind farm.
“While the wind resources are superb, the ground resource is pretty challenging. You’re not building on solid rock; it’s all weathered sandstone and poor geotechnical conditions. Rainfall of up to two metres per annum plus weathered sandstone means the soil doesn’t have much strength. That leaves you trying to build very large wind turbines on unstable ground in a very remote area,” he said.
The project team worked with Vestas and its subcontractor Menard, a global foundations solutions business, to use a technique that had not been used for a wind farm in Australia.
It involved creating controlled modulus columns by drilling 100 to 140 holes, between four and 20 m deep for each foundation, then filling them with pressurised grout. This displaced and increased the density of the surrounding soil and created a solid base for the footings.
The foundations were constructed with roughly 100 trucks worth of concrete (700 to 750 m3 of concrete per foundation) and 70 t of steel to create a base roughly 22 m across in diameter and up to five meters deep.
To keep the concrete flowing, two concrete batching plants were built on site to avoid the risk of one breaking halfway through a pour, and gravel and sand were stockpiled on site. A quarry was also built on site to source crushed rock for the roads and hardstands.
The ground conditions also created challenges for the construction of the 12 km transmission line and 220 kV switching station.
Engineers Australia member and Chartered engineer Antony Beard MIEAust CPEng, Operations Manager for PIMS, oversaw grid connection works and noted the challenges for designing and building foundations for the transmission infrastructure in such difficult conditions.
“The transmission line contractors had to develop some quite innovative approaches to foundations including utilising techniques similar to those being used on the main wind farm,” he said.
Given the remote location and difficult terrain, helicopters were used to string the high voltage conductors.
“After lots of planning, it was incredible to watch the highly skilled helicopter pilots safely complete this precision work,” recalled Beard.
Environmental risks
One of the major issues in protecting the environment was avoiding the risks associated with creating steep embankments.
The risks included erosion due to the high rainfall and clay soil, the spread of invasive weeds due to the inability of cattle to traverse the slopes and managing sediment runoff into the pristine creeks that feed straight into the Southern Ocean.
Adding to the challenge, the original designs were created by engineers in offices many kilometres away, who were less familiar with the site-specific conditions and erosion issues.
Graduate engineer Darcy Carew, the site civil engineer for Vestas, found a solution.
Carew bought himself a drone to take pictures of the stunning landscape, then found it was an effective tool for capturing site progress and monitoring potential environmental hazards.
It was so useful that Vestas upgraded the drone with mapping capabilities which, combined with geographic information system (GIS) software, were used to create extremely refined topographical maps of existing landforms and develop erosion and sediment control plans.
The team could then stand together in the paddocks and use the detailed maps to discuss how best to overcome issues.
It found that compared with traditional surveying techniques the more nuanced maps provided a higher level of resolution in a quicker time, which enabled fast and informed decisions during construction and proved a critical tool in getting consensus on the final landforms.
The end result was a seamless transition between the farm and infrastructure created by extending excavations up to 100 m into the paddocks to enable them to go right to the edges of the roads and hardstands. The gentle slopes reduced water shedding and allowed cattle to safely graze up to the edges.
Reflections
Carew pursued engineering because he was attracted to “using technology and critical thinking to find creative solutions to problems”. He hopes the use of drones and GIS mapping will be adopted for other wind farms.
For Frearson, Granville Harbour Wind Farm reinforced Ekistica’s appreciation of the importance of understanding place and how local conditions should drive a design, rather than tailoring an existing plan for the location.
“When you start with a place-based focus, it might take you in a slightly different direction, but it gets you the right outcome.”